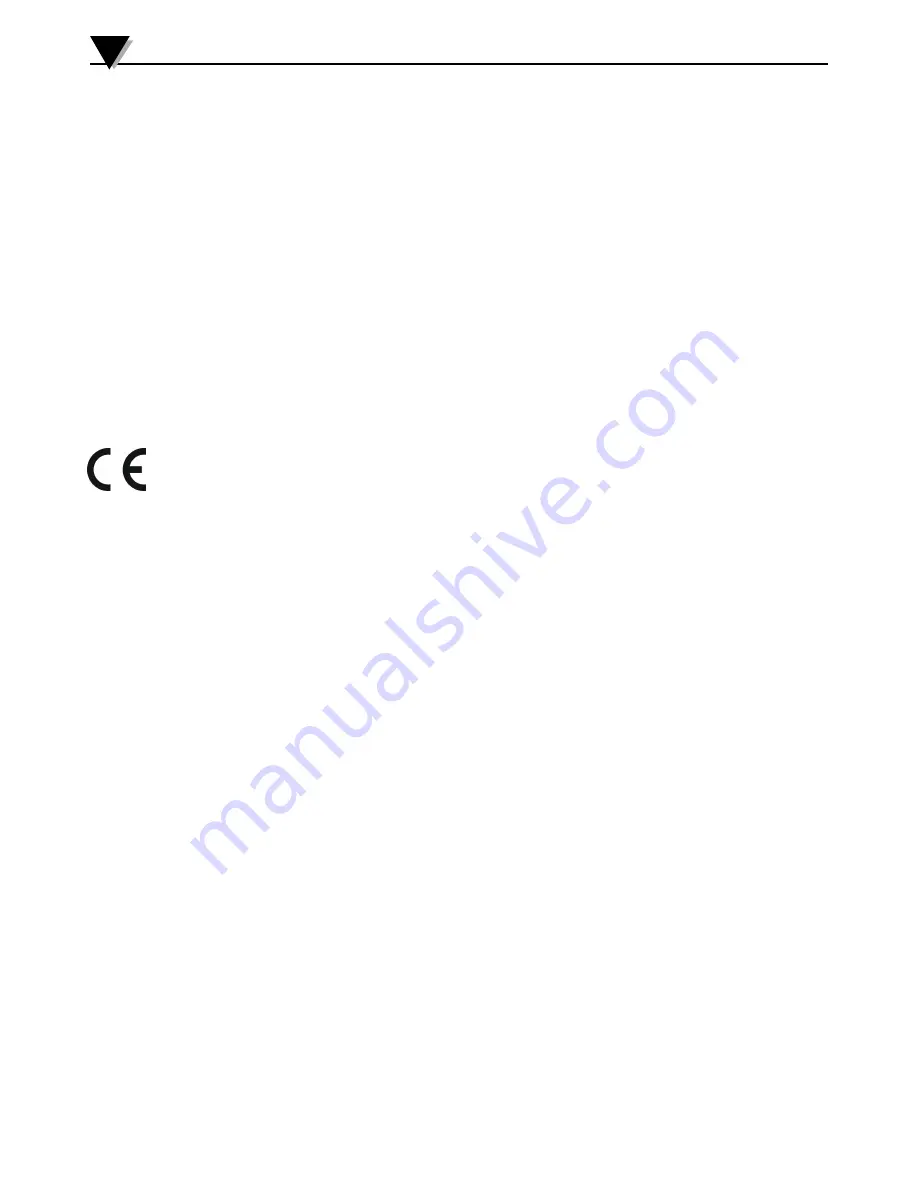
PRODUCT CERTIFICATIONS
FACTORY MUTUAL
INTRINSIC SAFETY:
The (I/P Models I/P211-X15-ISF and I/P211-X27-ISF) transducers are rated intrinsically safe by FM for:
- CLASS I, DIVISION 1, GROUPS A,B,C,D T6, Ta=40˚C HAZARDOUS LOCATIONS when installed in accordance with
interconnection drawing 990-440-000, and the specific barrier models.
NOTICE: The above ratings only apply when installed per Interconnection Diagram 990-440-000
- Nonincendive for CLASS I, DIVISION II, GROUPS A, B, C, D.
CANADIAN STANDARDS ASSOCIATION
INTRINSIC SAFETY:
The I/P (I/P211-X15-ISC and I/P211-X15-ISC) are rated intrinsically safe by CSA for: Class I Groups A,
B, C, and D; Class II Groups E, F, and G; and Class III, when connected through certified diode safety barriers in accor-
dance with Interconnection diagram, 990-440-000
ELECTRICAL CONNECTIONS
PRECAUTIONS TO BE OBSERVED DURING INSTALLATION
M4110/0519 IP211, EP211 SERIES
A
4
The Transducers were tested at the EMC Test Centre, Dunfermline, Fife, KY11 5LB to the Electromagnetic
Compatibility Directive effective January 1, 1996. The relevant EMC specifications tested were the following: EN
50081-1 (1992) and EN 50082-1 (1992). A Technical Construction File, Serial #107 was written and Certificate of
Conformity issued by a Competent Body.
EN 50081-1 (1992): Test results confirmed that no precautions need to be observed during installation regarding electro-
magnetic emissions from the I/P & E/P 211 Transducers.
EN 50082-1 (1992): The following precautions should be taken during installation to maintain the advertised accuracy
specifications for the Transducers. The input wiring to the transducer should be isolated from other high voltage transient
wiring. The momentary switching on and off of nearby relays, motors, or other high capacitive or inductive loads can have a
minor effect on the terminal based linearity specification (1.0% of span, standard range models). Any change in output
pressure is minimal and momentary, and is considered to be within its performance capabilities. Use of a ferrite bead collar on
the input wires entering the transducer is recommended should installation next to high electromagnetic interference be
necessary.
Connect electrical signal to the wires exiting from the side of transducer through the 1/2" NPT conduit fitting.
For
DIRECT ACTING
: (where increasing the input signal increases output pressure), connect the positive input signal to the
black
transducer lead, and the negative to the
white
transducer lead.
For
REVERSE ACTING
: (where increasing the input signal decreases output pressure), connect the positive input signal to the
white
transducer lead, and the negative to the
black
transducer lead. Agency Approved Models may also be operated in either
mode.