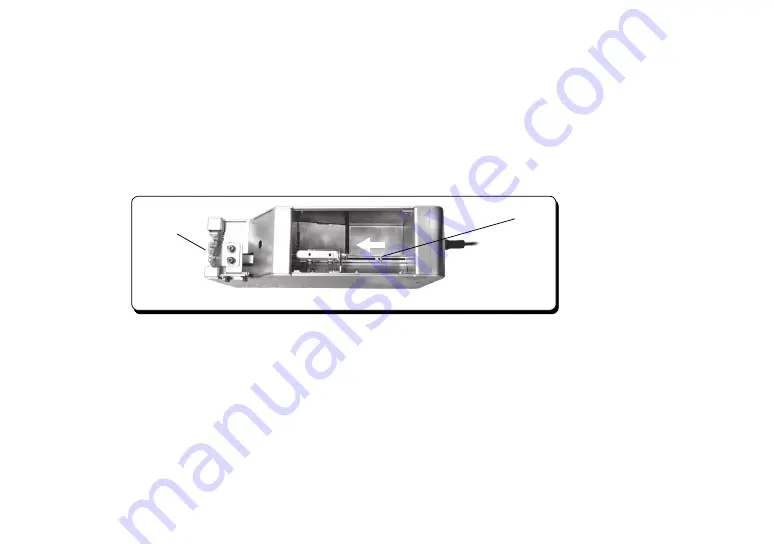
- 12 -
● Adjustment is necessary if the screw flow is not smooth or if there is too much rail vibration.
○ Adjust the Amplitude control dial on the back of the machine using the precision screwdriver.
○ Adjust the Vibration frequency control dial on the back of the machine using the precision screwdriver and find the
resonance point.
Adjust these dials to locate the optimum conditions for smooth movement of screws.
● Maximize the amplitude and adjust the vibration frequency to locate the resonance point (frequency when the rail vi-
bration is at a maximum.) Then turn down the amplitude to locate the optimum conditions for smooth movement of
screws.
● Although it is not recommended, the rail vibration can be adjusted while the machine is operating.
● During control dial adjustment, do not force the screwdriver beyond its rotation limits.
● The rail vibration has been adjusted before shipment using screws that correspond to the rail size.
(Refer to the label number on the rail for the nominal screw diameter: e.g. 17 is φ1.7)
● Put 2 or 3 screws into the rail groove and turn the machine on.
● No adjustment is necessary if the screws move to the stopper position smoothly. (See Picture 13)
●When the number of screws is low and no screw is picked up in a given period of time, vibration will become the
maximum and it will stop operation after that. (Refer to 4-2 “Basic Operation.”)Adjustment of volume is not effective
at the time of a forced oscillation.
● After it stops, turn on the machine again and repeat the above procedure.
5 - 5. Rail Vibration Adjustment
Stopper
Adjust the rail vibration so that the screw moves
smoothly in the direction of the arrow.
Screw
Picture 13