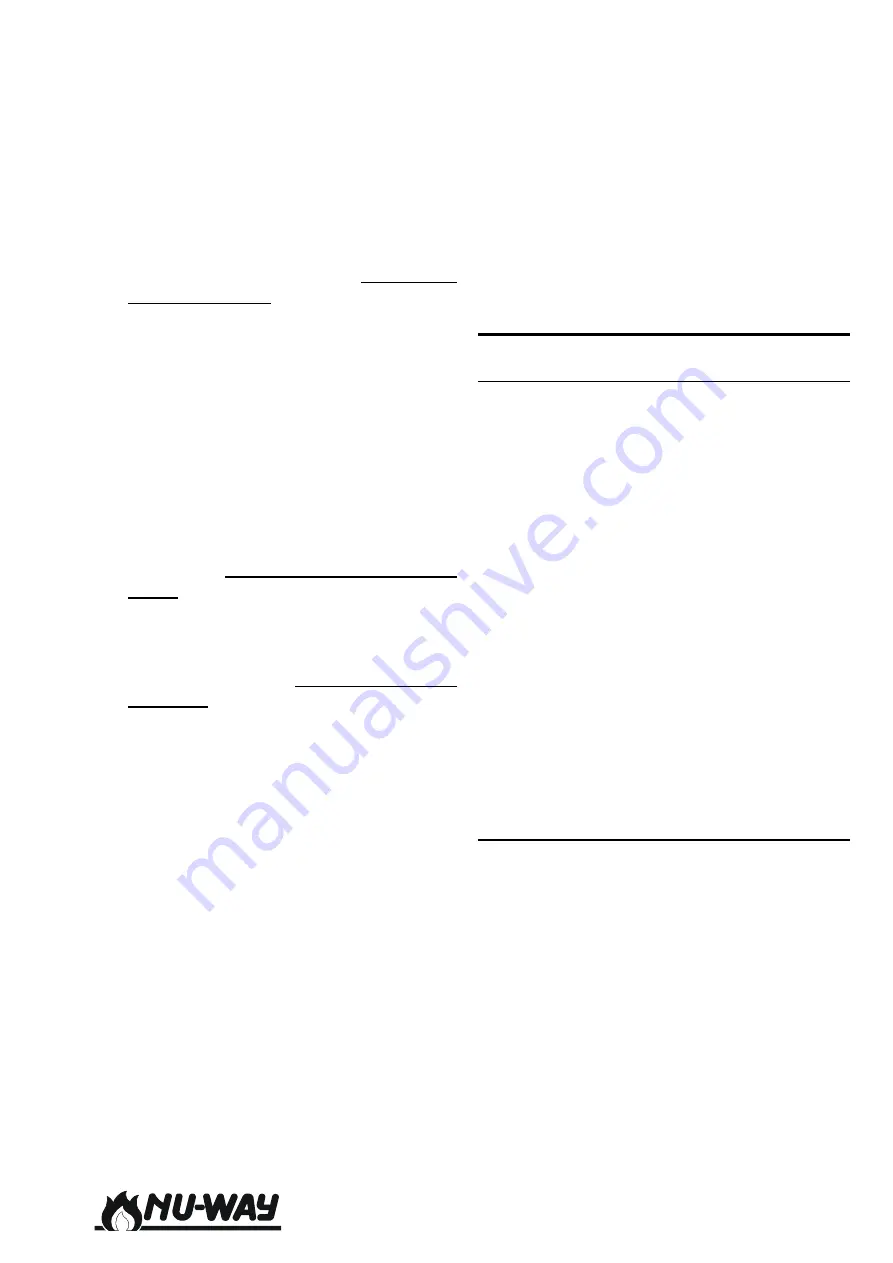
Page 15
XGN Handbook
•
Press (+) to move the control point to P2,
again making any adjustments to keep the
flame safe and stable.
•
Follow the above procedure through P3, P4
etc. until position P9, the high fire position,
is obtained.
•
With the gas butterfly set at 90°, adjust the
governor on the SKP2x valve to give the
required high flame gas flow.
•
Adjust the air damper position to give the
required combustion analysis.
Note the air
damper position.
•
Switch off the burner and restart the
procedure from entering the pass code.
•
Adjust the value of the air damper at P9 to
that noted above.
•
Scroll through to the GAS EL display and start
the burner.
•
At the ignition point P0, adjust the air and
start gas values to give a good light up.
Ensure that the start rate gas flow
does not exceed 30% of the high
flame gas rate as measured at the
Gas Meter Note the gas and air posi-
tions.
•
Move to point P1 and adjust the gas butterfly
to give the required low flame gas flow. Adjust
the air damper to give the required
combustion analysis.
Note the gas and air
positions.
•
Switch off the burner and restart the
procedure from entering the pass-code.
•
Adjust the value of the gas and air settings to
those noted at points P0, P1 and P9.
•
Scroll through to the GAS EL display and start
the burner.
•
Move to point P2, the firing rate will increase.
•
Adjust the air damper to give the correct
combustion analysis.
•
Repeat the above procedure for points P3
through P8, fine tuning the combustion
analysis as required.
•
When the burner is firing satisfactorily, return
the burner to set point P9.
Two further points
Bu
and
Bo
, which correspond
to the minimum and maximum firing rates can now
be set using the air damper angles that were set at
P1 and P9 respectively.
•
Press keys (1) and (2) together to access the
display point Bu. Wait until the display is
steady. Adjust the value to reflect the air
damper angle at P1.
•
Press keys (1) and (2) again to access the
display point bo. Wait until the display is
steady. Adjust the value to reflect the air
damper angle at P9.
•
Finally, press keys (1) and (2) again to enter
the information into memory.
The procedure is now complete.
F
INAL
A
DJUSTMENTS
Setting the Air Pressure Switch
Switch off the electrical supply to the burner.
Remove the air pressure switch cover. Fit a
manometer to the pressure switch to check the
accuracy of the dial.
Re-establish the electrical supply.
Enter the pass-code as described on page 13 for a
part commissioning. The default settings will not
be displayed. Switch on and the burner will purge
then fire at point PO. Slowly turn the adjusting
dial clockwise until the flame is extinguished; the
burner may go to lockout. Turn the dial one
division anticlockwise and let the burner restart, if
the burner fails to start, turn the dial another
division anticlockwise. Repeat the above
procedure at one division per cycle until the
burner operates. Adjust the dial a further two
divisions anticlockwise.
Switch off the burner, isolate the electrical supply,
fit the cover and remove the manometer.
Setting the Flame Signal
When the burner is operating normally, carefully
turn back the sensitivity control until LED 1 begins
to flicker. Increase the setting again by one or two
increments until both LED’s are lit. If LED 1 does
not flicker even at position 1: Leave potentiometer
at position 1-2. This adjustment should be carried
out when the flame signal current is weakest (at a
cold-start, shortly after flame establishment or af-
ter stabilisation).
The flame signal can be checked by using a
microammeter.
The minimum signal required is 15 µA
The MBC display is designed to give an indication
of the signal, the screen gives a 0 to 4 readout.
See service display screen 18.
Summary of Contents for XGN Series
Page 4: ...XGN Handbook Page 4...
Page 23: ...Page 23 XGN Handbook XGN450 23 XGN650 23...
Page 24: ...XGN Handbook Page 24 XGN1000 25 XGN1150 38...
Page 30: ...XGN Handbook Page 30 NOTES...
Page 31: ...Page 31 XGN Handbook NOTES...