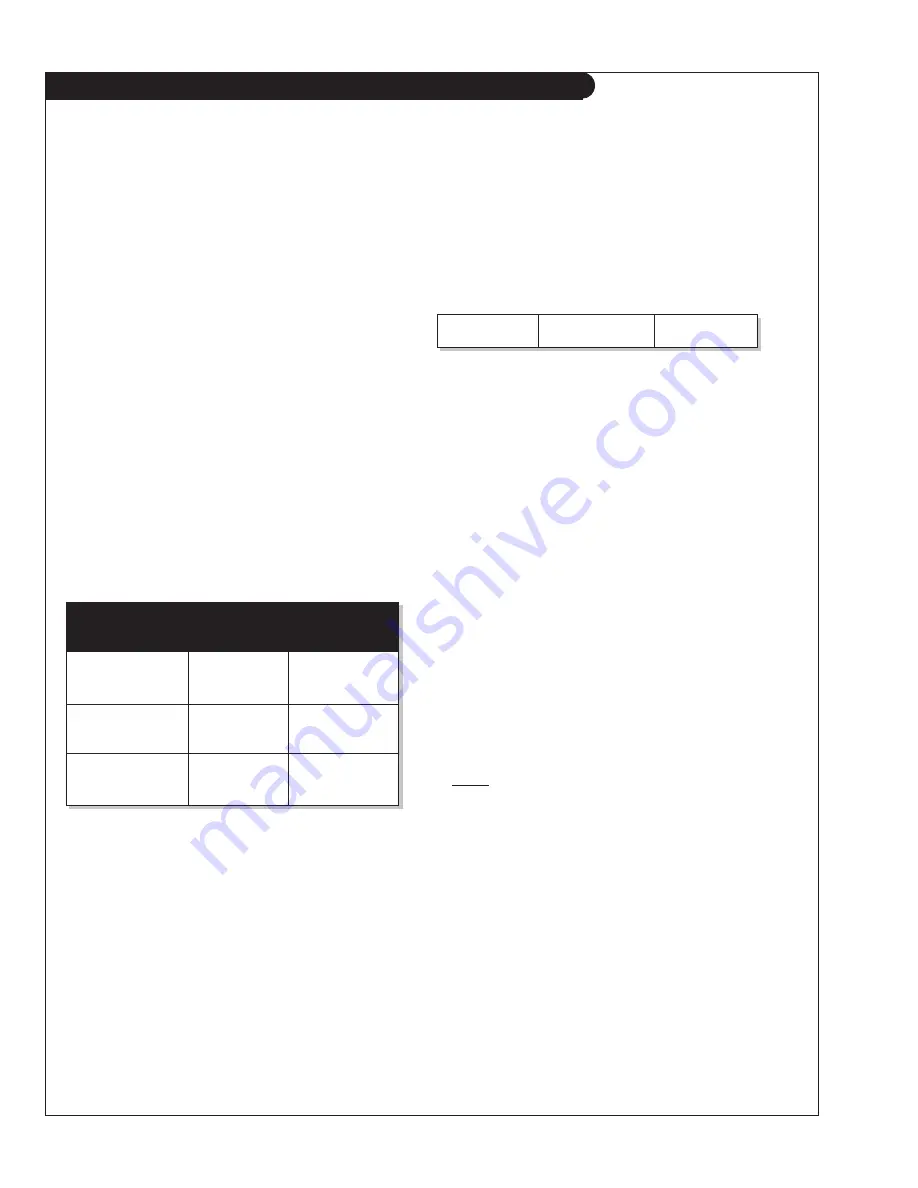
OL1276 03/10
12
LUBRICATION
Break-in oil
1. Use one of the following during the
fi
rst 100 hours
of operation:
a. John Deere Engine Break-In Oil
b. API Service CC, CD oil
c.
ACEA
Speci
fi
cation E1
2.
Do not use
John Deere PLUS-50 oil or engine oils
meeting API CF-4, API CG-4, API CH-4, API
CI-4, ACEA E2, ACEA E3, ACEA E4, or ACEA
E5 performance levels during the
fi
rst 100 hours of
operation of a new or rebuilt engine. These oils will
not allow the engine to break-in properly.
Lubrication - General
1. Use only clean, high quality lubricants stored in
clean containers in a protected area.
2. These oils are acceptable after the
fi
rst 100 hours:
a. API Service CH-4, CJ-4 multi-viscosity oils.
b. API Service CD/CG-4/CF-4 multi-viscosity oils.
c.
ACEA
Speci
fi
cation E3
d.
ACEA
Speci
fi
cation E4/ E5
3. Use the proper weight oil for your average operation
temperature.
4. Some increase in oil consumption may be expected
when SAE 5W and SAE 5-20W oils are used. Check
oil level frequently.
5. Never put additives or
fl
ushing oil in crankcase.
SP1. CHECK ENGINE OIL LEVEL
1. Check the oil level in the crankcase, with the oil
dipstick, daily.
2. The oil level must be between the “Waf
fl
ed area”
and the “Add”. Never allow the level to go below the
“Add”.
3. Always add the same viscosity of oil as is already in
the crankcase.
SP2. OIL CHANGES
1. Using the oil recommended above, change the engine oil
and
fi
lter after the
fi
rst 100 hours of operation, and every
250 hours thereafter.
2. During intermittent cold weather operation, change oil
every 100 hours or six weeks, whichever comes
fi
rst.
3. Change oil at any seasonal change in temperature when a
new viscosity of oil is required.
4. Engine Lube Oil Capacity:
SP3. CHANGING OIL FILTER
1. Change the lube oil
fi
lter every 250 hours.
2. Use a
fi
lter wrench to remove old
fi
lter. Dispose of
fi
lter
in approved manner.
3. Make sure the gasket from the old
fi
lter is removed and
discarded.
4. Lubricate the rubber gasket on the new
fi
lter and screw it on
nipple until gasket meet the sealing surface.
5. Using hands only, no wrench, tighten
fi
lter one-half turn
farther. Overtightening can do damage to
fi
lter housing.
6. Fill engine with recommended oil. Start engine and
check for leakage. Stop engine and check oil level. Add
additional oil if necessary.
SP4. AIR CLEANER
1. Inspect air cleaner every 100 hours, clean and re-oil
every 600 hours, or yearly, or when red service light is
visible in air
fi
lter restriction indicator; whichever comes
fi
rst. Replace
fi
lter element after 5 to 7 cleaning cycles,
depending on condition.
Note: Use part # 24-20019 Cleaning and Re-Oiling Kit,
do not use motor oil or other oils to re-oil
fi
lter.
2. Replace oil separator
fi
lter every 600 hours, or yearly, or
if oil leakage is seen at crankcase pressure regulator vent;
whichever comes
fi
rst.
Note: Air
fi
lter element must be
removed to access retaining clamp and cover that retains
oil separator
fi
lter inside.
3. Check hoses and clamps on crankcase pressure regulator
plumbing for tightness, cha
fi
ng or deterioration.
4. Start the engine and check for leaks.
NOTE:
Make absolutely sure no impurities enter the
engine while changing the element. Do not run the
engine with the air cleaner removed.
Air
Single
Multi
Temperature
Viscosity
Viscosity
Above
32°F
(0°C)
SAE-30W SAE15-40W
-10°F to 32°F
(-23°C to 0°C)
SAE-10W SAE10-30W
Below
-10°F
(-23°C)
SAE-5W SAE5-20W
1276
44.4 qts.
42 liters
Servicing
Corrected page 2-6-08