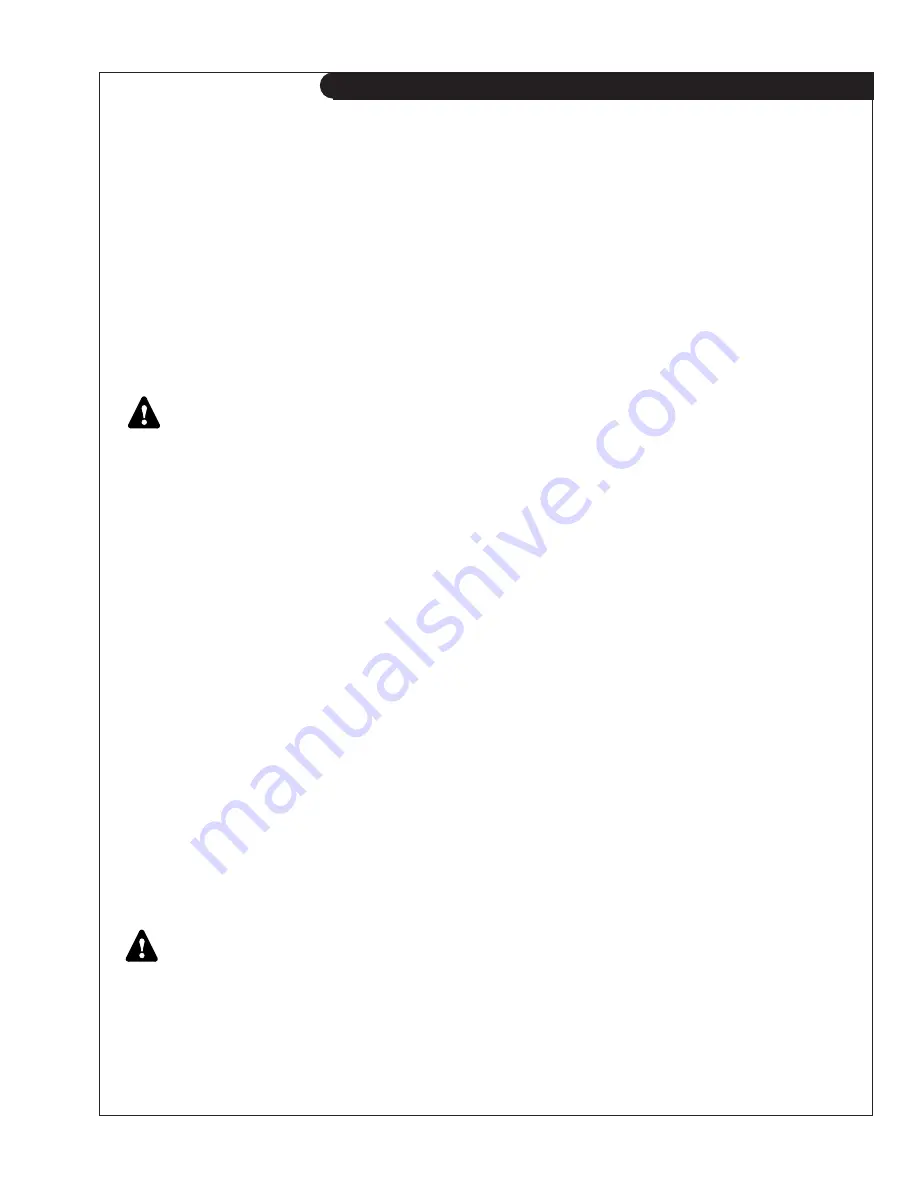
OL1276 03/10
17
COOLANT TESTING
1. Coolant test kits are available to allow on-site
evaluation of the coolant condition.
2. The kits use small strips of paper which are dipped
into the coolant. The paper changes color and indi-
cates the SCA concentration. It also indicates the
amount of EGC (antifreeze).
3. Test kits are available through your Northern Lights
or Lugger Dealer.
4 Pack - Part Number.......................20-00005
50 Pack - Part Number.....................20-00010
SP14. CHECKING COOLANT LEVEL
.
CAUTION:
The cooling water in the engine
reaches extremely high temperatures. You must
use extreme caution when working on hot engines
to avoid burns. Allow the engine to cool before
working on the cooling system. Open the
fi
ller
cap carefully, using protective clothing when the
engine is warm.
1. Check the coolant level each day before starting the
engine.
2. Remove the pressure cap from the expansion tank
and check water level. In order to give the coolant
an opportunity to expand, the level should be about
1 3/4 in. (4-5 cm) below the
fi
ller cap sealing surface
when the engine is cold. When
fi
lling with cool-
ant, the venting cock on top of the turbocharger (for
engines
fi
tted with turbocharger) should be opened
to ensure that no air pockets form in the cooling
system.
2. The pressure valve in the
fi
ller cap releases when the
pressure is approximately 7 PSI (0.5 bar). Use a cap
pressure tester to check cap if you suspect it is faulty.
4. The makeup coolant, added to compensate for loss
or leaks, must meet engine coolant requirements
outlined in previous section.
SP15. FLUSHING THE COOLING SYSTEM
CAUTION:
The cooling water in the engine
reaches extremely high temperatures. You must
use extreme caution when working on hot engines
to avoid burns. Allow the engine to cool before
working on the cooling system. Open the
fi
ller cap
carefully, using protective clothing when the engine
is warm.
1. Flush the cooling system and check for leaks and
blockage every 600 hours, or yearly.
The engine
must be stopped and cold.
2. Close the seacock.
3. Remove the pressure cap from the expansion tank
with caution. If applicable, open the cooling system
air vent on top of turbocharger.
4. Open the drains on the exhaust manifold and engine
block. Drain the fresh water system (see Component
Locations, page 4).
5. For vessels with keel cooling, the vessel must be out
of the water to allow draining of the keel cooler.
6. With drains open, pour clean water into the expansion
tank. When the water from drain is clear and free from
discoloration and sediment, close that drain. When all
drains are closed,
fl
ushing is complete.
7. Fill the fresh water system by pouring the
recommended coolant mixture as described in previ-
ous sections.
8. Close cooling system air vent on turbocharger.
9. Open the seacock.
10. Start the engine. Check hoses and connections and
repair any leakage.
SP16. HEAT EXCHANGER CLEANING
1.
Drain the cooling system.
2. Remove the cooling water pipes between the heat
exchanger and the water pump inlet.
3. Disconnect hose to seawater pump.
4. Unscrew the attaching bolts holding the heat
exchanger to the expansion tank.
5. Remove bolts holding heat exchanger cover.
6. Wash the core inside and out. If necessary, chemical
agents can be used. Also clean the accessible parts of
the heat exchanger housing.
7. Reassemble, using new gaskets and sealing rings.
SP18. ZINC ANODES
1. Zincs are installed in the cooling system to protect
your engine from electrolysis. Check them faithfully
every 250 hours. If you are in warm salt water or
where electrolysis is a known problem, check them
more often.
Servicing