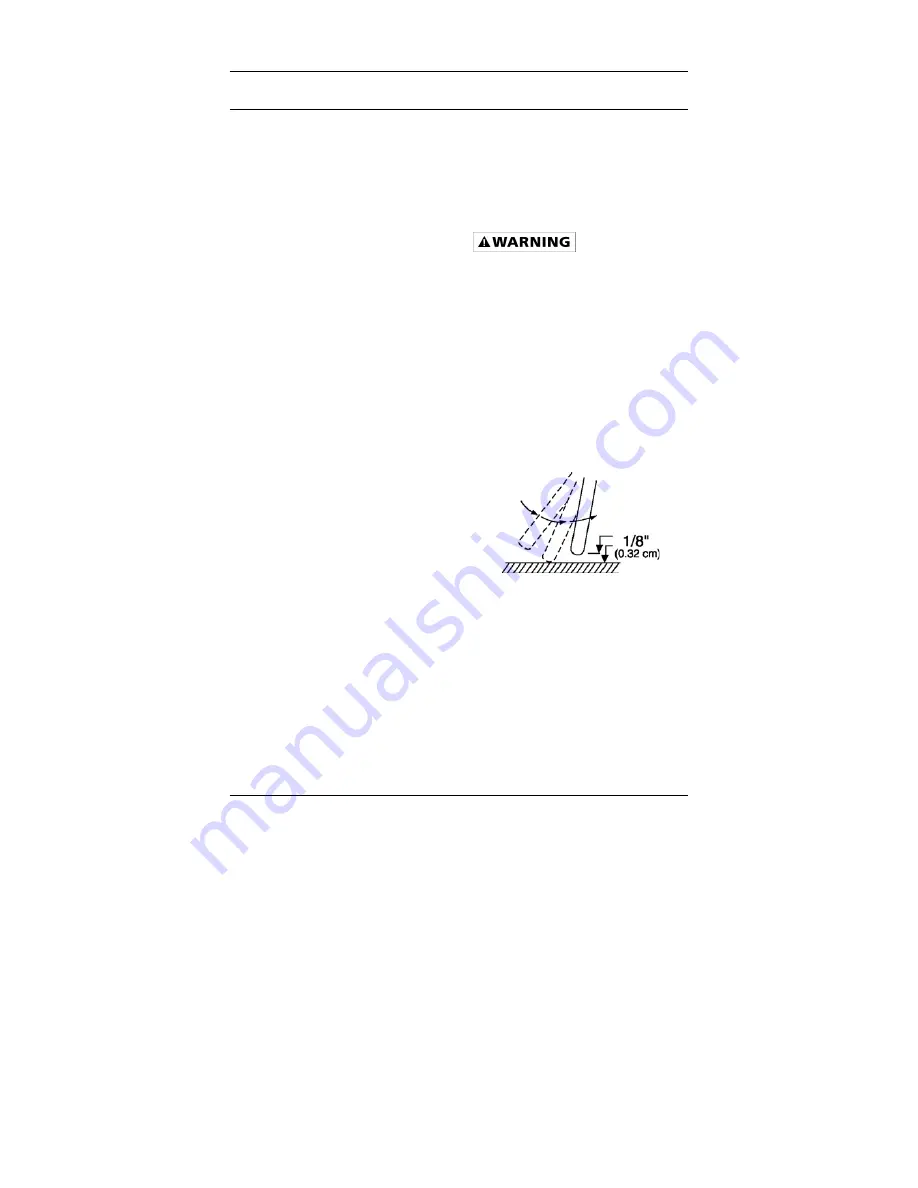
Northern Industrial Welding
9
Operating Instructions and Parts Manual
ST80i
c.
The bead will be flat and porous
d. Rod may be freeze or stick to
work piece
Note:
Rate of travel over the work
also affects the weld. To ensure
proper penetration and enough
deposit of rod, the arc must be moved
slowly and evenly along the weld
seam.
Operation
1. Setting the amperage control
The welder has an infinite output
current control. It is capable of
welding with 1/16" and 5/64" and
3/32" electrodes.
There is no golden rule that
determines the exact amperage
required for every situation. It is best
to practice your welds on scrap metal
which matches the metals you intend
to work with to determine correct
setting for your job. The electrode
type and the thickness of the work
piece metal determine the amount of
heat needed in the welding process.
Heavier and thicker metals require
more voltage (amperage), whereas
lighter and thinner metals require less
voltage (amperage).
2. Welding techniques
The best way to teach yourself how to
weld is with short periods of practice
at regular intervals. All practice welds
should be done on scrap metal that
can be discarded. Do not attempt to
make any repairs on valuable
equipment until you have satisfied
yourself that your practice welds are
of good appearance and free of slag
or gas inclusions.
2.1 Holding the electrode
The best way to grip the electrode
holder is the way that feels most
comfortable to you. To Position the
Electrode to the work piece when
striking the initial arc it may be
necessary to hold the electrode
perpendicular to the work piece.
Once the arc is started the angle of
the electrode in relation to the work
piece should be between 10 and 30
degrees. This will allow for good
penetration, with minimal spatter.
2.2 Striking the arc
EXPOSURE TO A WELDING ARC
IS EXTREMELY HARMFUL TO THE
EYES AND SKIN.
• Never strike an arc or begin
welding until you have adequate
protection.
• Wear flameproof welding gloves,
heavy long-sleeved shirt, cuffless
trousers, high-topped shoes and a
welding helmet or shield.
Scratch the work piece with the end
of electrode to start arc and then
raise it quickly about 1/8 inch gap
between the rod and the work piece.
See following picture
:
It is important that the gap be
maintained during the welding
process and it should be neither too
wide or too narrow. If too narrow, the
rod will stick to the work piece. If too
wide, the arc will be extinguished.
It needs much practice to maintain
the gap. Beginners may usually get
sticking or arc extinguishing. When
the rod sticks to the work piece,
gently rock it back and forth to make
them separate. If not, the circuit is
short connection, and it will overload
the welder.
Summary of Contents for ST 80 i
Page 1: ...67 L 23 5 7 1 0 18...