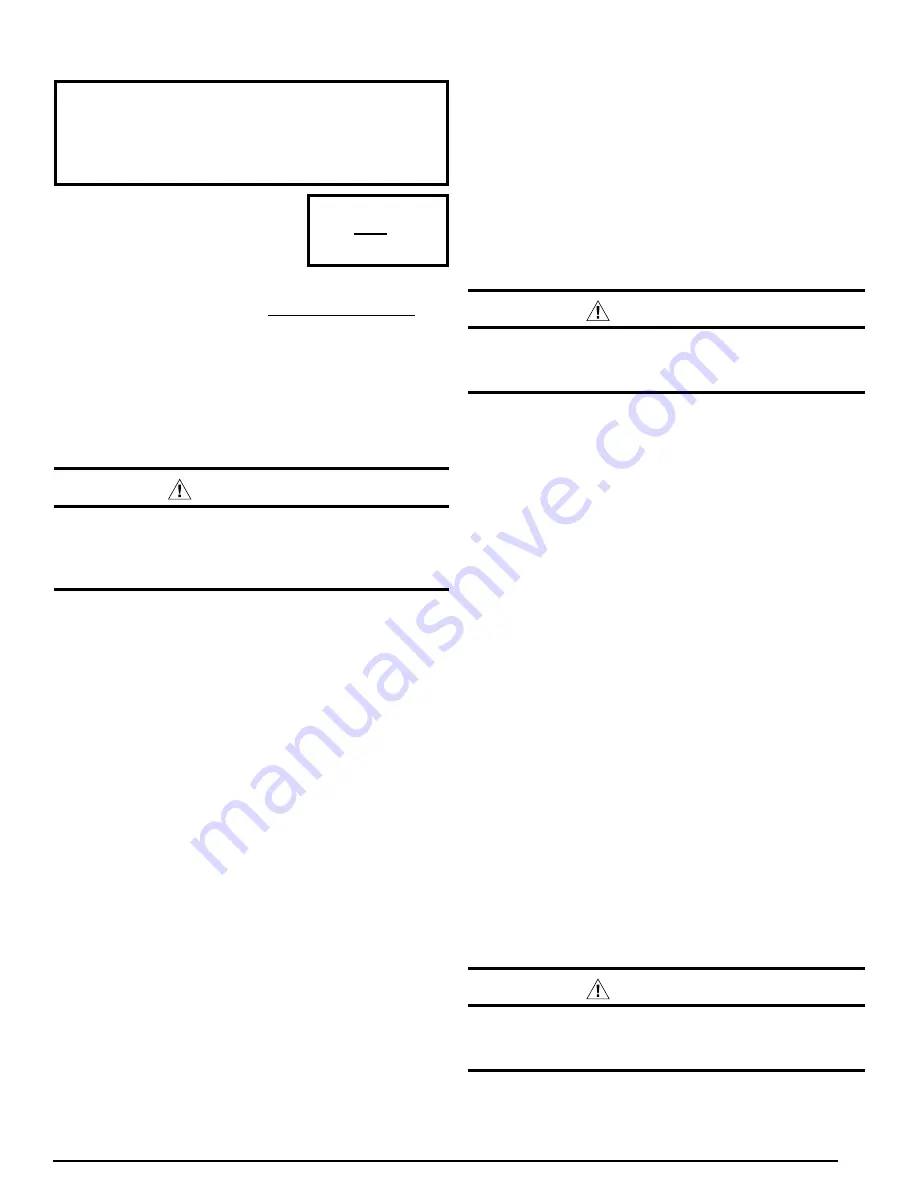
13
3. Determine the maximum deviation:
EXAMPLE
From the values given in step 1, the BC voltage (460V) is
the greatest difference in value from the average:
460 - 454 = 6
454 - 451 = 3
454 - 453 = 1
4. Determine percent of voltage
imbalance by using the results from
steps 2 & 3 in the following equation.
6
454
100 x
= 1.32%
EXAMPLE
max voltage deviation
from average voltage
= 100 x
average voltage
% Voltage Imbalance
The amount of phase imbalance (1.32%) is satisfactory since
the amount is lower than the maximum allowable 2%. Please
contact your local electric utility company if your voltage
imbalance is more than 2%.
Grounding
WARNING:
The unit cabinet must have an uninterrupted or
unbroken electrical ground to minimize personal
injury if an electrical fault should occur. Do not use
gas piping as an electrical ground!
This unit must be electrically grounded in accordance with
local codes or, in the absence of local codes, with the National
Electrical Code (ANSI/NFPA 70) or the CSA C22.1 Electrical
Code. Use the grounding lug provided in the control box for
grounding the unit.
Thermostat / Low Voltage Connections
• The R8GE unit is designed to operate from a 24 VAC Class
II control circuit. The control circuit wiring must comply with
the current provisions of the NEC (ANSI/NFPA 70) and
with applicable local codes having jurisdiction. Thermostat
connections should be made in accordance with the
instructions supplied with the thermostat and the indoor
equipment.
• The low voltage wires must be properly connected. Route 24V
control wires through the sealing grommet near the power
entrance. Recommended wire gauge and wire lengths for
typical thermostat connections are listed in
.
• Several thermostat options are available depending on the
accessories installed with the unit. Select a thermostat that
operates in conjunction with the installed accessories.
• The thermostat should be mounted about 5 feet above the
floor on an inside wall. DO NOT install the thermostat on
an outside wall or any other location where its operation
may be adversely affected by radiant heat from fireplaces,
sunlight, or lighting fixtures, and convective heat from warm
air registers or electrical appliances. Refer to the thermostat
manufacturer’s instruction sheet for detailed mounting
information.
Checking Heat Anticipator Settings
• Add the current draw of the system components.
OR
• Measure the current flow on the thermostat
R
-
W
circuit
after the circulating blower motor has started. Set the heat
anticipator according to the thermostat manufacturer’s
instructions for heat anticipator settings.
Blower Speed
The blower speed is preset at the factory for operation at the
same speed for heating and cooling. These factory settings
are listed in
. For optimum system
performance and comfort, it may be necessary to change the
factory set speed.
CAUTION:
To avoid personal injury or property damage, make
sure the motor leads do not come into contact with
any uninsulated metal components of the unit.
1. Shut off all electrical power to the unit and remove the blower
panel. Locate the orange, red and blue wires terminated to
the blower motor.
NOTE:
The orange wire controls cooling
operation while the red wire controls heating operation. The
blue wire controls fan-only operation.
2. Verify the required speed from the airflow data found in Table
10. Place appropriate wire on the correct motor speed tap
for the required airflow point.
3. The integrated furnace control can be set to a 2 or 3 speed
mode. When a
G
only call is received from the thermostat
(indicating a continuous fan mode), the blower will run the
heating speed when the
2-SPD
mode is selected using the
jumper on the control board (factory setting). When
3-SPD
mode is selected, the fan only speed may be different than
the heating or cooling speed. If no jumper is present, the
control defaults to the
2-SPD
mode of operation. A call for
heating or cooling takes priority over fan only mode
Optional Humidistat
An optional humidistat may be installed in the return air duct
for humidity control (when needed), maximum system capacity
and energy efficiency. The humidistat senses when humidity
in the return air stream is above a preset level and sends a
signal to the motor to reduce airflow. This allows more moisture
to be removed until the humidity level drops.
NOTE:
The packaged heat pump unit is pre-programmed for
humidistat operation. Remove the jumper connector between
the two terminals marked
HUM
on the variable speed board.
Install the humidistat in the return air duct as directed in the
installation instructions included with the kit. Wire the humidistat
through the low-voltage wire entrance in the packaged heat
pump unit to the quick-connect terminals (marked
HUM)
Wire
the humidistat to open on rise in humidity.
CAUTION:
To avoid personal injury or property damage, make
certain that the motor leads cannot come into contact
with any uninsulated metal components of the unit.
Check all factory wiring to the units wiring diagram. Inspect the
factory wiring connections to be sure none loosened during
shipping or installation.