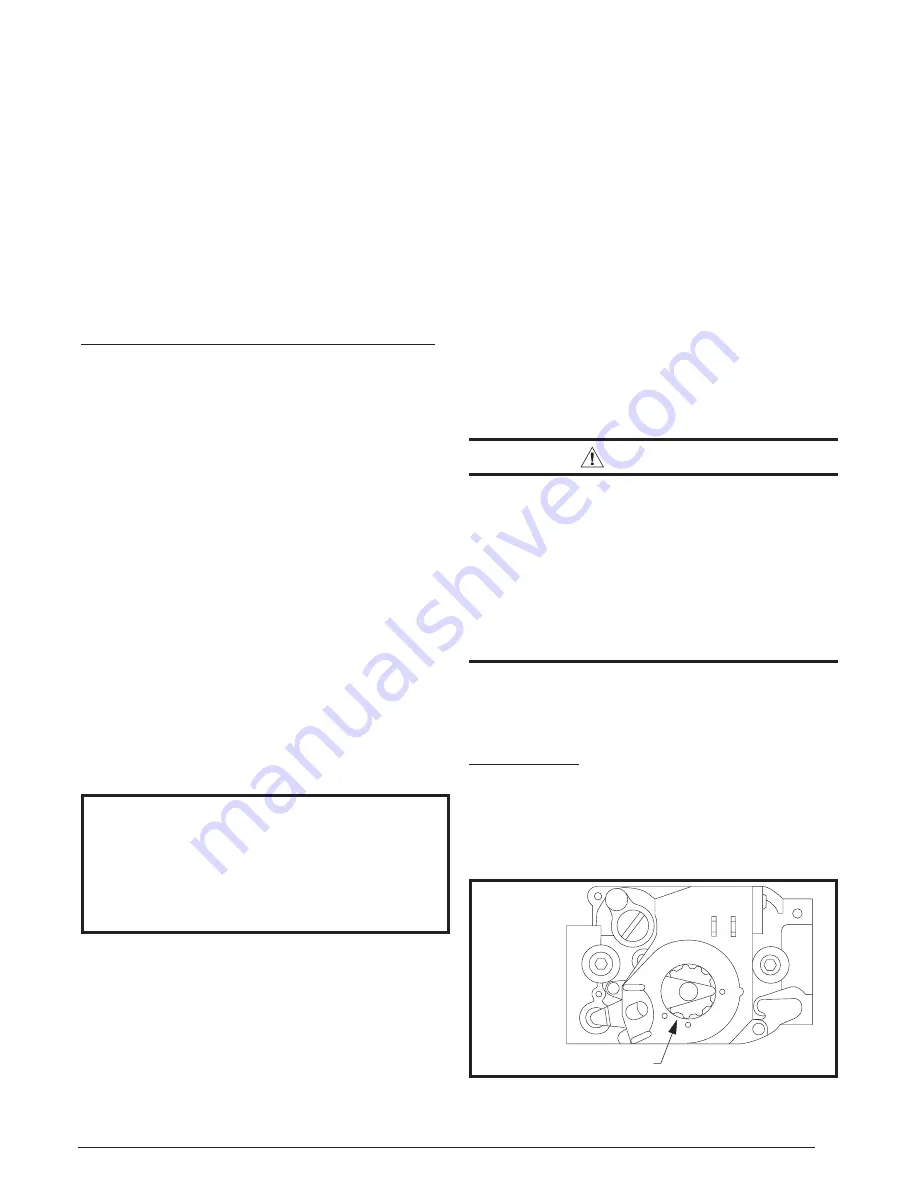
21
5. Set the thermostat MODE the
ON
position.
6. Turn the gas valve ON. Push in and turn gas control
knob counter-clockwise to
ON
7. Replace the furnace door.
8. Turn on all electric power to the appliance.
9. Change the thermostat mode to
HEAT
and the
temperature selector to a desired temperature level.
The igniter should light in approximately 75 seconds.
If the appliance will not operate, see “How to Shut Off
Gas - Direct Ignition” on
and call your service
technician or gas supplier.
NOTE:
In the event of any flashback or explosion,
immediately shut off the furnace and call your service
technician.
How to Shut Off Gas - Direct Ignition Models
1. Set the thermostat to the lowest setting.
2. Turn off all electric power to the appliance before
servicing unit.
3. Set the furnace On-Off Switch to
OFF
.
4. Turn gas control knob clockwise to
OFF
5. Replace the furnace door.
Verifying Input Rate
IMPORTANT NOTE:
The input rate must not exceed the rate shown on the
furnace rating plate. At altitudes above 2,000 feet, it
must not exceed that on the rating plate less 4% for
each 1,000 feet.
The input rate must be verified for each installation to
prevent over-firing of the furnace. To determine the exact
input rate, perform the following procedures:
1. Shut off all other gas fired appliances.
2. Start the furnace and run it for at least 3 minutes.
3. Measure the time (in seconds) required for the gas
meter to complete one revolution.
4. Convert the time per revolution to cubic feet of gas per
hour using
5. Multiply the gas flow rate in cubic ft per hr by the heating
value of the gas in Btu per cubic ft to obtain the input
rate in Btuh. See example.
Example:
• Time for 1 revolution of a gas meter with a 1 cubic ft
dial = 40 seconds.
• From
• Local heating value of the gas (obtained from gas
supplier) = 1,040 Btu per cubic ft.
• Input rate = 1,040 x 90 = 93,600 Btuh.
6. The manifold pressure must be verified for each
installation by a qualified installer, service agency or
the gas supplier. See
Verifying & Adjusting Temperature Rise
Confirm the temperature rise through the furnace is
within the limits specified on the furnace rating plate. Any
temperature rise outside the specified limits could result
in premature failure of the heat exchanger.
1. Place thermometers in the return and supply air stream
Figure 29. Direct Ignition Gas Valve - Honeywell
GAS CONTROL KNOB
as close to the furnace as possible. To avoid false
readings, the thermometer on the supply air side must be
shielded from direct radiation from the heat exchanger.
2. Adjust all registers and duct dampers to the desired
position and run the furnace for 10 to 15 minutes in
high fire before taking any temperature readings. The
temperature rise is the difference between the supply
and return air temperatures.
For typical duct systems, the temperature rise will fall
within the limits specified on the rating plate with the
blower speed at the factory recommended setting. If
the measured temperature rise is outside the specified
limits, it may be necessary to change the speed of the
blower.
NOTE:
Lowering the blower speed increases the
temperature rise and a higher blower speed will decrease
the temperature rise.
The furnace is equipped with a multi-tap ECM motor. For
alternate motor tap selections see
&
Burner Adjustments
CAUTION:
• Adjustment must be made only by a qualified
technician. Improper air adjustment may
cause unsafe operation, explosion and/or fire
asphyxiation.
• If the input to the furnace is too great because
of excessive gas pressure, wrong size nozzle or
orifice, high altitude, etc., the burner flame will
be sooty and can produce carbon monoxide,
which could result in unsafe operation,
explosion and/or fire or asphyxiation.
Burner settings are made at the factory. However, these
settings may change during shipping, handling, and
installation. The following items should be checked and
readjusted if necessary.
Gas Pressure
The gas pressure can be checked with a manometer at
the pressure tap located on the top of the gas valve.
Natural gas manifold pressure should be 3.5” W.C. and
L.P. gas manifold pressure should be 10” W.C. Replace
Summary of Contents for MG1 Series
Page 31: ...31...