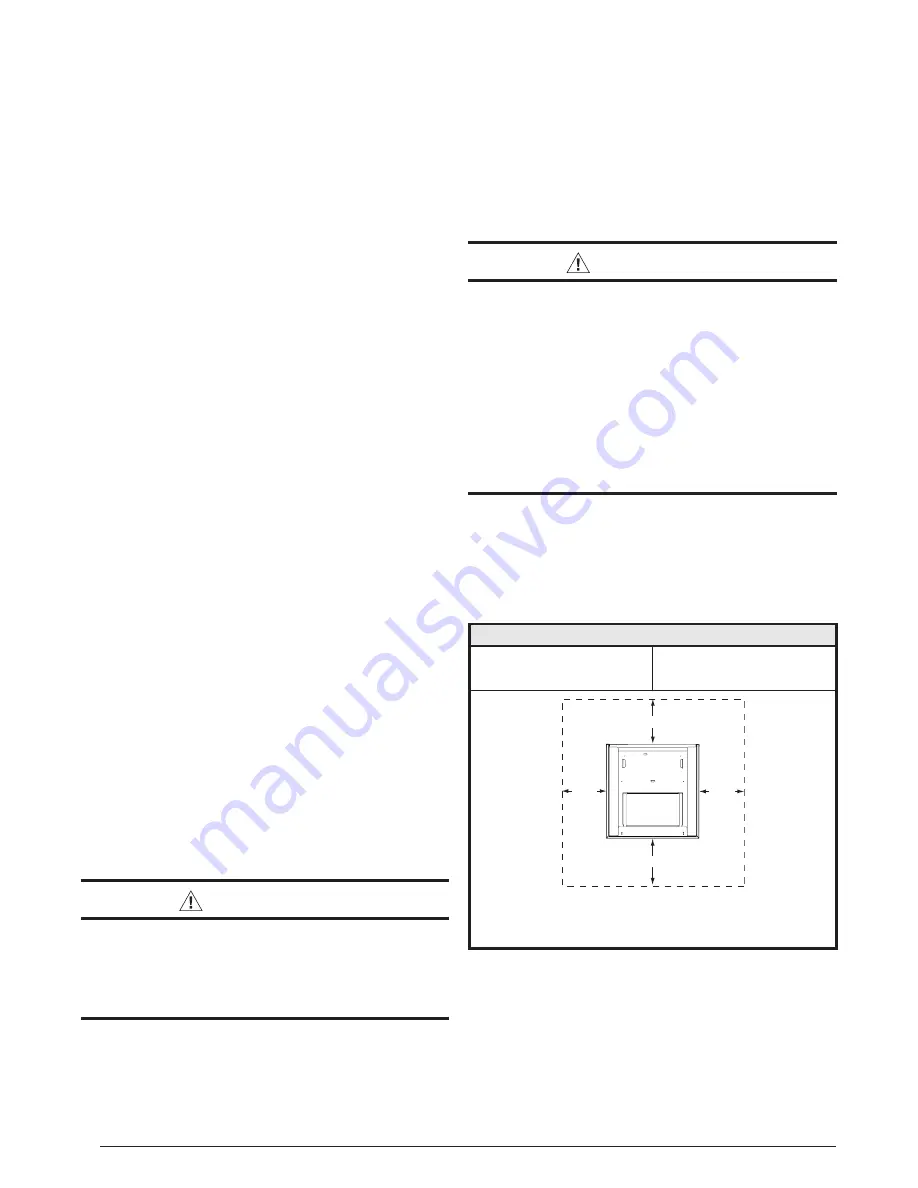
4
GENERAL INFORMATION
This appliance has been tested for capacity and efficiency
in accordance with AHRI Standards and will provide many
years of safe and dependable comfort, providing it is properly
installed and maintained. Abuse, improper use, and/or
improper maintenance can shorten the life of the appliance
and create unsafe hazards. Please read all instructions
before installing the unit.
Before You Install this Unit
√
This equipment is securely packaged at the time of
shipment and upon arrival should be carefully inspected
for damage prior to installing the equipment at the job
site. Claims for damage (apparent or concealed) should
be filed immediately with the carrier.
√
it is recommended that the cooling load of the area to
be conditioned should be calculated and a system of the
proper capacity selected.
√
Check the electrical supply and verify the power supply
is adequate for unit operation. The system must be wired
and provided with circuit protection in accordance with
local building codes. If there is any question concerning
the power supply, contact the local power company.
√
Verify the duct system is appropriate for the air handler
being installed. Please note that when replacing an existing
system with lower air-flow, the duct system may require
modification.
Locating the Air Handler
• Survey the job site to determine the best location for
mounting the unit. Consideration should be given to
availability of electric power, service access, and noise.
• The dimensions of the room or alcove must be able to
accommodate the overall size of the unit and the installation
. Physical dimensions for this
air handler are also shown in
• The air handler should be set into position before routing
the refrigerant tubing.
Minimum Clearances
• This appliance must be installed in accordance with
. The air handler must be
installed with ample clearance for easy access to the air
filter, blower assembly, heater assembly, controls, and
vent connections. Applicable building codes may require
additional clearance to equipment. Refer to applicable
building codes for details.
• Static pressure drop through louvered openings and
through return air plenums should be considered in the
overall duct design in the determination of the total external
static pressure.
Installation in a Garage
WARNING:
Do not place combustible materials on or against
the cabinet. Do not place flammable materials,
(gasoline, paint thinners, etc.) or any other
flammable vapors and liquids, in the vicinity of
the air handler.
The B64 Series air handler may be installed in a residential
garage with the provision that the unit must be located or
protected to prevent physical damage by vehicles.
Plenums & Air Ducts
• Plenums and air ducts should be installed in accordance
with the standards of the National Fire Protection
Association Standard for Installation of Air Conditioning
Systems (NFPA 90A), Standard for Installation of Residence
Type Warm Air Heating and Air Conditioning Systems (NFPA
90B), and all applicable local codes. NFPA publications
are available by writing to: National Fire Protection
Association, Batterymarch Park, Quincy, ME 02269 or visit
www.NFPA.org online.
WARNING:
All return ducts must be secured to the air
handler using appropriate methods. All return
ducts must be adequately sealed. When return
air is provided through the bottom of the unit,
the joint between the air handler and the return
air plenum must be air tight.
Return air and circulating air ducts must not be
connected to any other heat producing device
such as a fireplace insert, stove, etc. This may
result in fire, explosion, carbon monoxide
poisoning, personal injury, or property damage.
• Design the duct work according to methods described
by the Air Conditioning Contractors of America (ACCA).
• This unit is designed only for use with a return and supply
duct. The return air duct must have the same free area as
the opening provided on the air handler. The ducts should
be appropriately sized to the capacity of the air handler
to ensure its proper airflow rating.
INSTALLATION CLEARANCES
Left Side ............. 0 Inches
Right Side ......... 0 Inches
Back ................. 0 Inches
Front ...............†See Notes
†
NOTE:
Alcove Installations
- Allow 24 in. minimum clearance from front
of unit to nearest wall or partition for servicing. Recommended
clearance is 36 in.
REAR
RIGHT
SIDE
LEFT
SIDE
FRONT
Table 1. Minimum Unit Clearances
Summary of Contents for B64EM Series
Page 27: ...27...