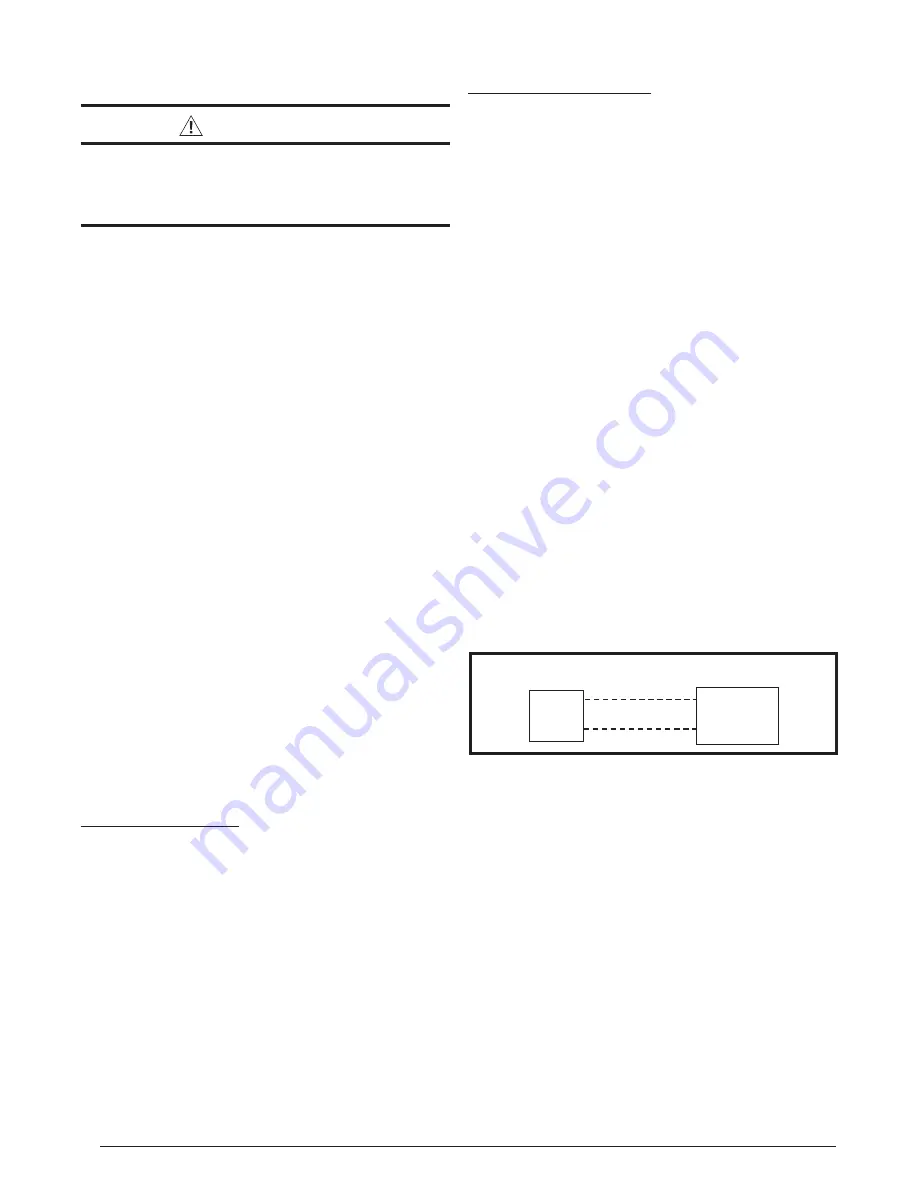
10
Grounding
WARNING:
The unit cabinet must have an uninterrupted or
unbroken electrical ground to minimize personal
injury if an electrical fault should occur. Do not
use gas piping as an electrical ground!
This unit must be electrically grounded in accordance with
local codes or, in the absence of local codes, with the National
Electrical Code (ANSI/NFPA 70) or the CSA C22.1 Electrical
Code. Use the grounding lug provided in the control box
for grounding the unit.
Control Board
The control board in the air handler controls the timing
sequence of the elements. The board is equipped with a 3
second blower on delay and a 15 second blower off delay
in heating and a 40 second blower off delay in cooling.
See
and
for control board modes and actions.
Twinning
These instructions are to be used when connecting two B64
air handlers (2-4 ton models) to a common single stage A/C
condensing unit or heat pump. Twinning is possible for B64
units with PSC or fixed speed (FSHE) motors. Twinning is
not possible for units with variable (VSHE) speed motors.
All low voltage wiring instructions, cautions, and warnings
accompanying the air handler remain applicable, except for:
Line & Low Voltage Connections
a. The line voltage connections for both air handlers must
be the same phase and on the same leg of power.
b. Low voltage wiring should be connected as shown in
c. Wire all other low voltage thermostat terminals to
both air handlers as shown in
NOTE:
If there is any other air moving device in the
duct work, consult the factory for a resolution.
Heater Kits
When electric heat packages with circuit breakers are field-
installed, the circuit breaker may be used as a disconnecting
means in most applications. Reference the NEC and local
codes for disconnect requirements.
If a heater kit is installed:
B64EM and B64VM air handlers are shipped from the factory
without an electric heater kit installed. If electric heat is
desired, a heater kit may be purchased separately and field
installed. Determine the correct size heater kit for your unit
by referring to the heater kit installation instructions.
1. Connect the 2 wire plug of the air handler to the mating
2 wire plug of the heater kit.
2. Connect the line voltage leads to the circuit breaker or
terminal block provided.
3. Connect the heater kit plug with the mating receptacle
on the air handler control board.
4. Refer to Heater Kit Installation Instructions to determine
if you need to replace a limit or add an air baffle.
5. Connect blue blower limit wires according to Heater Kit
Installation Instructions and the corresponding Wiring
Diagram.
If a heater kit is not installed:
1. Remove the 2 wire plug of the air handler by cutting the
wires and discarding the plug.
2. Strip the ends of the 2 air handler wires and connect to
the line-voltage leads with the 2 wire nuts provided.
3. Certain air handler models are equipped with blower
. These are left
unconnected if a heater kit is not installed.
Humidifier
The unit has an output to power a humidifier when the blower
is running. This output is rated to 1.0 amp at 208/240V.
Dehumidification Options
The motor control board has a
DHUM
or
D
connection that
allows the system to increase the amount of humidity that
is removed from the circulating air. See
This is accomplished by reducing the CFM
and allowing the cooling coil to become colder. This will
only occur when there is a call for cooling. There are many
ways that this can be electrically wired.
1. If the room thermostat incorporates a humidity sensor and
DHUM
output, connect the
DHUM
on the thermostat to
the
D
terminal on the motor control board. See
2. If using a separate humidistat, connect the
DHUM
&
R
terminals on the humidistat to the
D
&
R
terminals on
the motor control board of the air handler. In this option,
the
DHUM
output of the humidistat must be set so it is
only closed when there is a call for dehumidification.
3. If a humidistat is not available, it is an acceptable
option to connect the
R
&
D
terminals on the motor
control board together with a field supplied wire. This
option causes the blower to run at a reduced CFM for
10 minutes after a call for cooling.
NOTE:
If outdoor
unit is a heat pump, connect the
O
terminal to the
D
terminal.
Electronic Air Cleaner (EAC)
The unit has an output to power an electronic air cleaner
when the blower is running. This output is rated to 1.0 amp at
208/240V. See
STARTUP & ADJUSTMENTS
Before You Start the Unit
Prior to start-up, complete the following inspections:
√
Verify the unit is level and properly located with adequate
clearances for servicing the unit as shown in
√
Check condensate drain line(s) for proper drainage.
√
Verify the surrounding area and top of the unit is free from
obstructions and debris.
√
Check all duct connections. Make sure the duct work is
adequately sealed to prevent air leakage.
√
Check all coil connections for leaks.
√
Verify that the line voltage power leads are securely
connected and the unit is properly grounded. Make sure
all doors are installed before restoring power to the unit
DHUM
R
R
DHUM
HUMIDISTAT
MOTOR
CONTROL BOARD
Figure 7. DHUM Wiring Configuration
Summary of Contents for B64EM Series
Page 27: ...27...