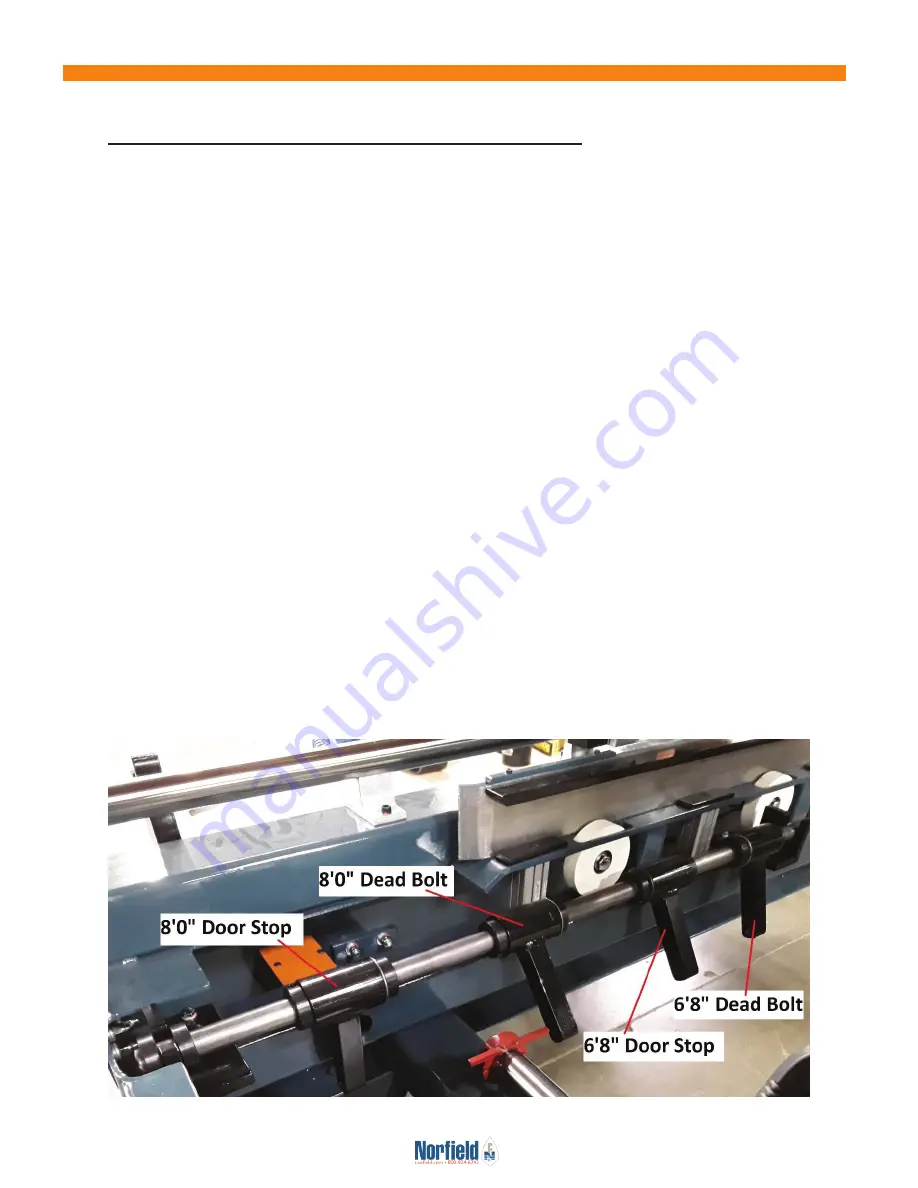
17
OPERATIONS
4800 XY OPERATING PROCEDURES
POSITION AND CLAMPING THE DOOR
1.
SELECT THE DOOR TO BE PROCESSED:
Before you begin you need to know the height and width of the door. Also the
size and shape of the lite to be cut.
2.
ADJUST THE WIDTH INDEX:
Move the width index to a size about 1 or 2 inches larger than the door. This will
make it possible to get the door into the machine. The width will move in and
“crowd” the door as part of the door clamping process. The width scale is located
to the operators left.
3.
INSERT THE DOOR.
The door is inserted, from the side of the machine, with the head toward the door
stop and the lock side away from the operator’s side of the machine. The door
stops may be installed at either end of the machine.
4.
PUSH THE DOOR AGAINST THE DOOR STOP AND CLAMP THE DOOR:
The head of the door should always be against a door stop. Knowing the door
size and the process being done to the door will determine the door stop to be
used.
Hold the door against the door stop and press the door clamp button. The width
index will crowd the door and clamp it up.
Summary of Contents for 4800XY
Page 2: ...2 First Release September 2019...
Page 5: ...5...