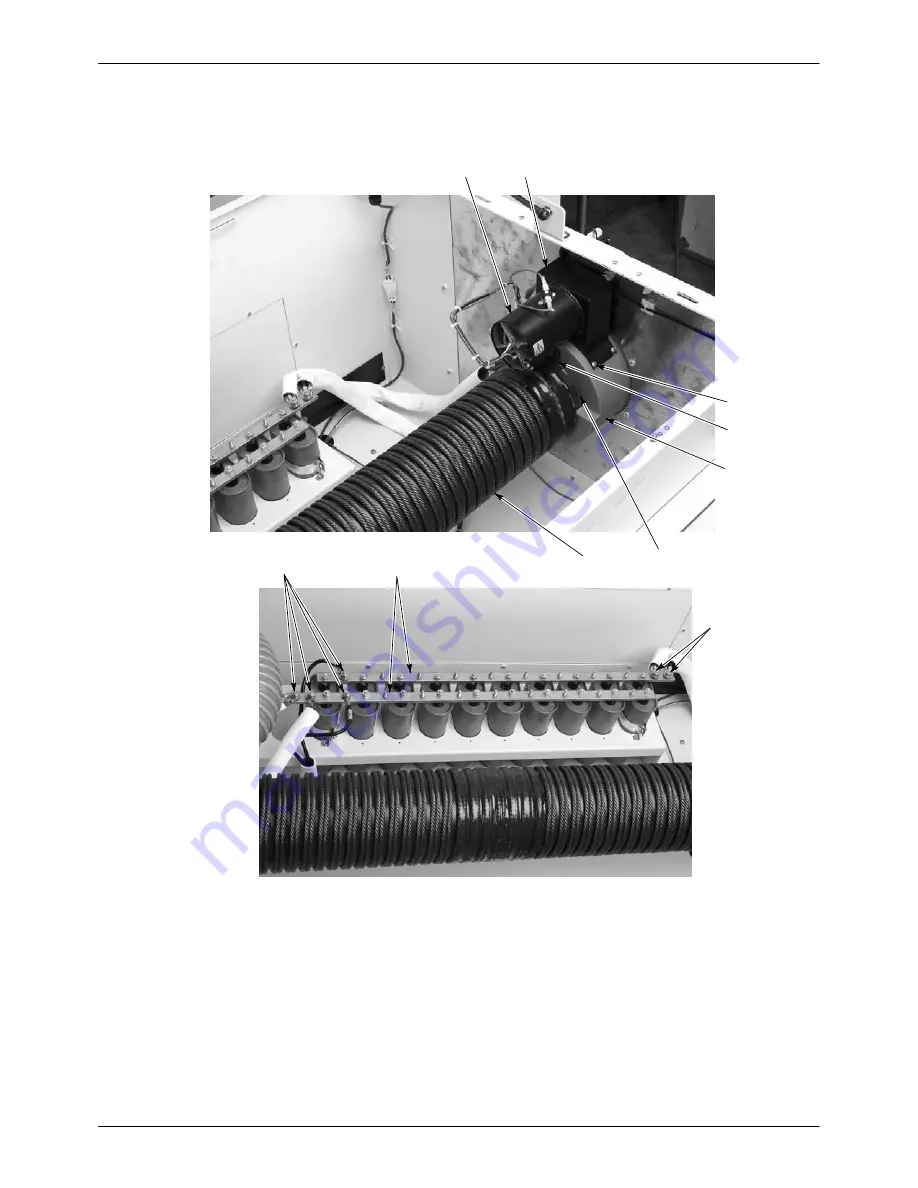
Nordson iDry
r
Series Induction Dryers
46
Part 1075452
−
04
E
2016 Nordson Corporation
Coil and Coil Tube Replacement
(contd)
1
7
2
4
3
5
6
8
8
9
Figure 43 Coil and Tube Replacement (Air Heater at Entrance End Shown)
1. Vent housings
2. Air Heater
3. Screws (4 on each hub)
4. Hubs
5. Nylon slotted screws
6. Glass tube (inside coil)
7. Coil
8. Coil connections (typical)
9. Bus bars