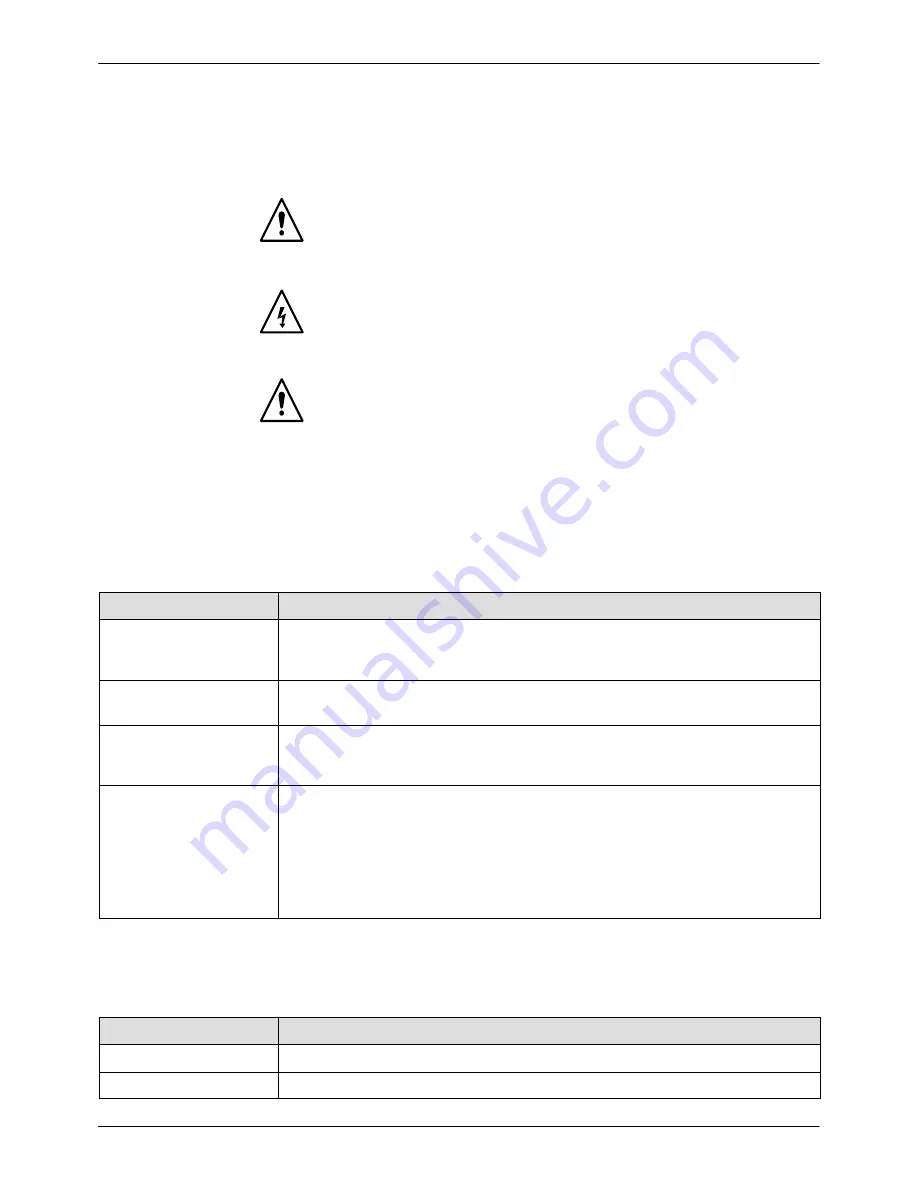
Nordson EcoDry
r
Series Induction Dryers with Touch Screen Controls
37
Part 1601306
−
02
E
2014 Nordson Corporation
Maintenance
The following parts of the dryer should be checked on the
indicated schedule.
WARNING:
Allow only qualified personnel to perform the following tasks.
Follow the safety instructions in this document and all other related
documentation.
WARNING:
Disconnect and lockout all power to the system before
perfoming any procedures that require working inside the coil tray or control
enclosure. Failure to observe may result in fatal injury to personnel.
WARNING:
Never disarm diagnostic devices including but not limited to:
S
Current sensor
S
Overtemperature switches
S
Air pressure switch
S
Coil tray lid safety switches
Disarming diagnostic devices will void the warranty and may cause
equipment failure.
Monthly
Item
Procedure
Thermocouple
Check the thermocouple for wear and good contact with the can ends. Clean
the thermocouple with a soft brush. Remove any debris lodged between the
element and the mounting pocket. Replace the thermocouple as needed.
Motion Sensor
Clean the sensor head lens with a clean, soft cloth. When the system is not
being used, cover the lens with the attached cover.
Cooling Blower Filter
Inspect the blower filter for dust or obstructions. Replace the filter as needed.
If the air flow is reduced, the system electronics can overheat. End drying
may also be affected by reduced air flow.
Coil Tray
Periodically inspect the glass coil tube for cleanliness and integrity. Clean the
tube with common solvents. Do not to get any solvent on the nylon hubs at
the dryer entrance or exit. Some solvents may also have an adverse effect on
the dryer’s exterior finish.
If the glass tube is cracked, only replace it with a new tube supplied by
Nordson. Different sizes and wall thicknesses are used depending on the can
end size and the application.
Quarterly
Item
Procedure
Electrical Connections
Check all wiring connections for vibration loosening.
Electrical Components
Check for excessive dust and dirt. Vacuum if needed.