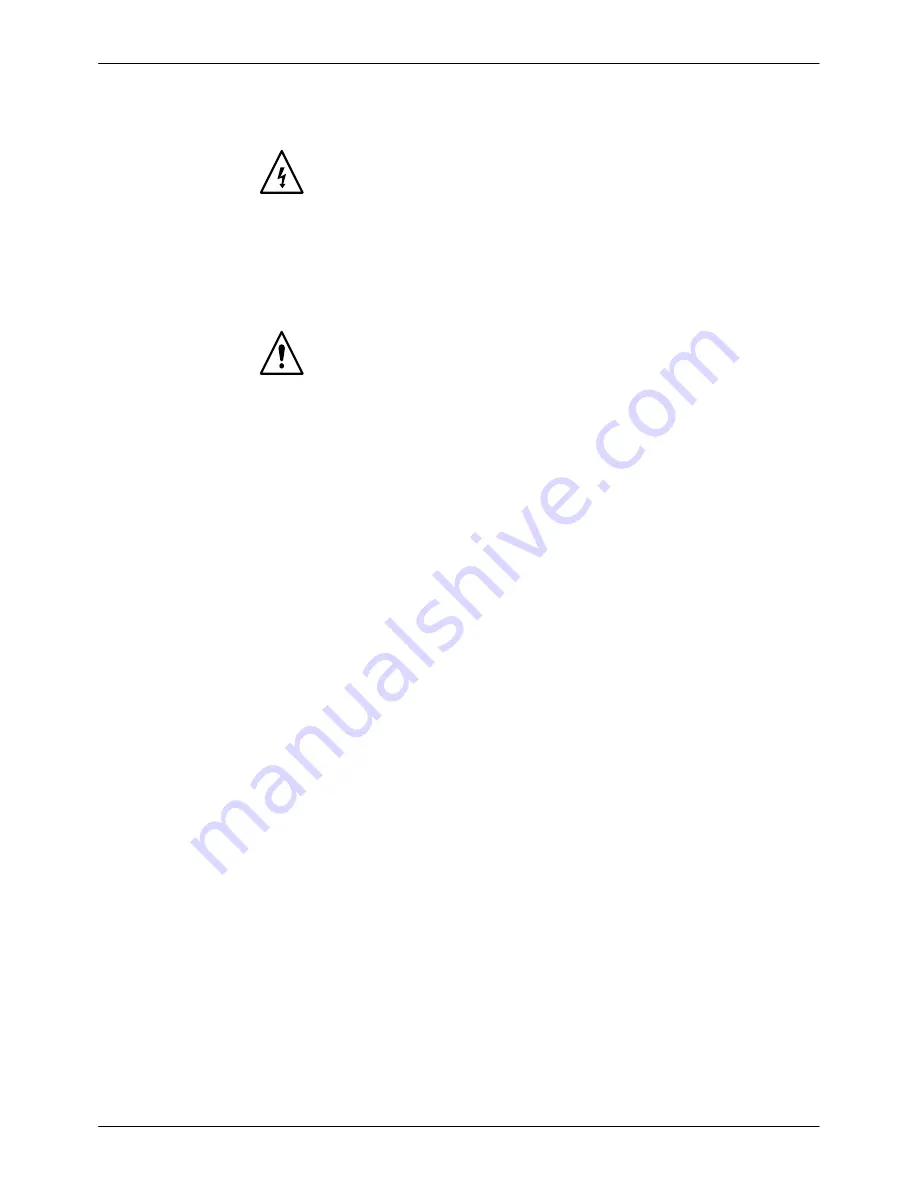
Nordson EcoDry
r
Series Induction Dryers with Touch Screen Controls
40
Part 1601306
−
02
E
2014 Nordson Corporation
Repair
WARNING:
Disconnect and lockout all power to the system before
perfoming any of the procedures in this section. Failure to observe may
result in fatal injury to personnel.
Repair of the dryer consists of replacing damaged or failed components.
Most repairs only require basic tools. Electrical repairs should always be
done by a qualified electrician with knowledge of high voltage systems.
For help with repairs not covered in this manual, contact your Nordson
representative.
WARNING:
Never disarm diagnostic devices including but not limited to:
S
Current sensor
S
Overtemperature switches
S
Air pressure switch
S
Coil tray lid safety switches
Disarming diagnostic devices will void the warranty and may cause
equipment failure.
Coil and Coil Tube Replacement
The coil and coil tube can be replaced separately. They both must be
removed to replace one or the other.
1. Shut down the dryer, turn the main disconnect to the OFF position, then
disconnect and lockout power at an external disconnect.
2. Unlock and open the coil tray lid.
3. Remove the screws securing the rear access panel with a hex wrench.
4. See Figure 29. Remove the screws (3) securing the exhaust vent
housing (1) and air heater (2) from the entrance and exit hubs (4). Move
the exhaust vent housing and air heater out of the way.
5. Remove the nylon slotted screws (5) from the face of the hubs.
6. See Figure 30. Disconnect the coil wiring from the bus bar terminals.
Push the wiring up through the hole in the bottom of the coil tray.
7. Lift the coil and tube assembly out of the dryer. Get help if needed.
8. Slide the coil tube out of the coil.
9. Unpack the new component(s) and re-assemble the coil and tube.
10. Carefully install the coil and tube assembly in the coil tray, positioning
the ends of the tube into the hubs. It does not matter which end of the
coil is at the entrance or exit.
11. Check the clearance between the end of the glass tube and the output
hub. There must be 0.8
−
1.6 mm (0.03
−
0.06 in.) of clearance to allow for
thermal expansion. If this clearance does not exist, shim the hub as
follows:
a. Loosen the six output hub mounting screws and install shim stock
between the hub flange and the sheet metal end plate.
b. Tighten the hub mounting screws and check the tube clearance.
c. Trim away any protruding shim stock.