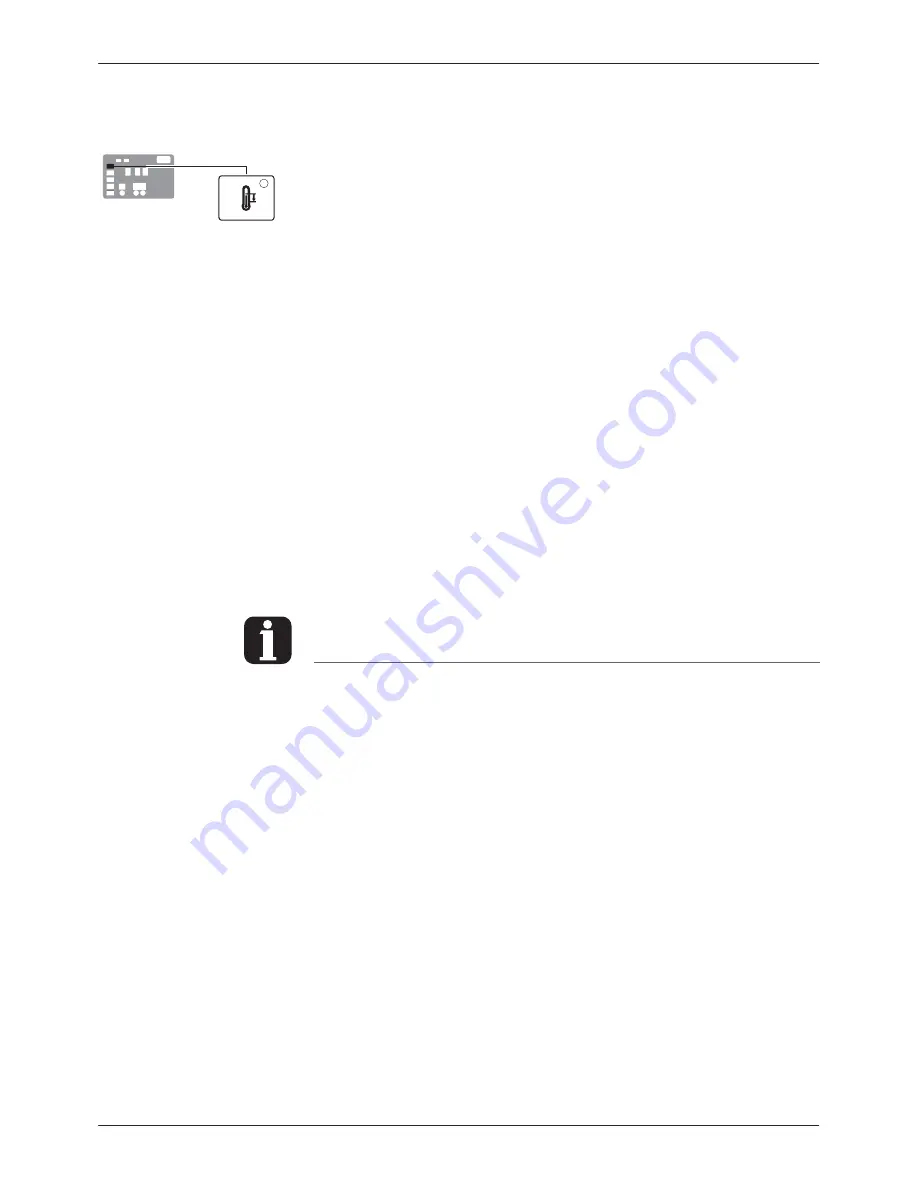
Standby key
Operation
4-22
Part 1032059B
E
2003 Nordson Corporation
Manual 41-DURABLUE-MA-02
Standby Key
Use the standby key to manually place the melter into, and take it out of, the
standby mode. Using the standby mode during periods of time when
the melter is inactive helps conserve energy and allows heated components
to quickly return to their set-point temperatures when the melter is once
again needed.
When the melter is placed into the standby mode, the temperatures of
all components are reduced down from their set-point temperature by a
pre-set standby delta. The melter will remain in the standby mode until the
standby key is pressed or the function of one of the operating parameters
takes the melter out of the standby mode.
If the melter was set up to use the manual standby timer
(parameter 26), pressing the standby key will place the melter in the
standby mode for the period of time specified by the timer. After the manual
standby time has elapsed, the melter will once again begin heating all of the
components to their assigned set-point temperature.
Using the standby key overrides the control of the melter (on or off) by
the seven-day clock or a remote input.
Refer to Section 3, Installation, Setting Up the Melter, and to Appendix B,
Operating Parameters, for information about setting the standby delta and
the standby timer.
The melter may also be set up to automatically
enter the standby mode using a variety of
operating parameters.
Appendix B, Parameters 25, 26, 57, 62,
and 67
Whenever manual standby is enabled, the
standby LED blinks.
Appendix B, Parameter 26
Summary of Contents for DuraBlue D10L
Page 91: ...Troubleshooting 6 11 Part 1032059B E 2003 Nordson Corporation Manual 41 DURABLUE MA 02...
Page 93: ...Troubleshooting 6 13 Part 1032059B E 2003 Nordson Corporation Manual 41 DURABLUE MA 02...
Page 95: ...Troubleshooting 6 15 Part 1032059B E 2003 Nordson Corporation Manual 41 DURABLUE MA 02...
Page 97: ...Troubleshooting 6 17 Part 1032059B E 2003 Nordson Corporation Manual 41 DURABLUE MA 02...
Page 99: ...Troubleshooting 6 19 Part 1032059B E 2003 Nordson Corporation Manual 41 DURABLUE MA 02...
Page 101: ...Troubleshooting 6 21 Part 1032059B E 2003 Nordson Corporation Manual 41 DURABLUE MA 02...
Page 103: ...Troubleshooting 6 23 Part 1032059B E 2003 Nordson Corporation Manual 41 DURABLUE MA 02...
Page 105: ...Troubleshooting 6 25 Part 1032059B E 2003 Nordson Corporation Manual 41 DURABLUE MA 02...
Page 107: ...Troubleshooting 6 27 Part 1032059B E 2003 Nordson Corporation Manual 41 DURABLUE MA 02...
Page 109: ...Troubleshooting 6 29 Part 1032059B E 2003 Nordson Corporation Manual 41 DURABLUE MA 02...
Page 111: ...Troubleshooting 6 31 Part 1032059B E 2003 Nordson Corporation Manual 41 DURABLUE MA 02...
Page 113: ...Troubleshooting 6 33 Part 1032059B E 2003 Nordson Corporation Manual 41 DURABLUE MA 02...
Page 115: ...Troubleshooting 6 35 Part 1032059B E 2003 Nordson Corporation Manual 41 DURABLUE MA 02...