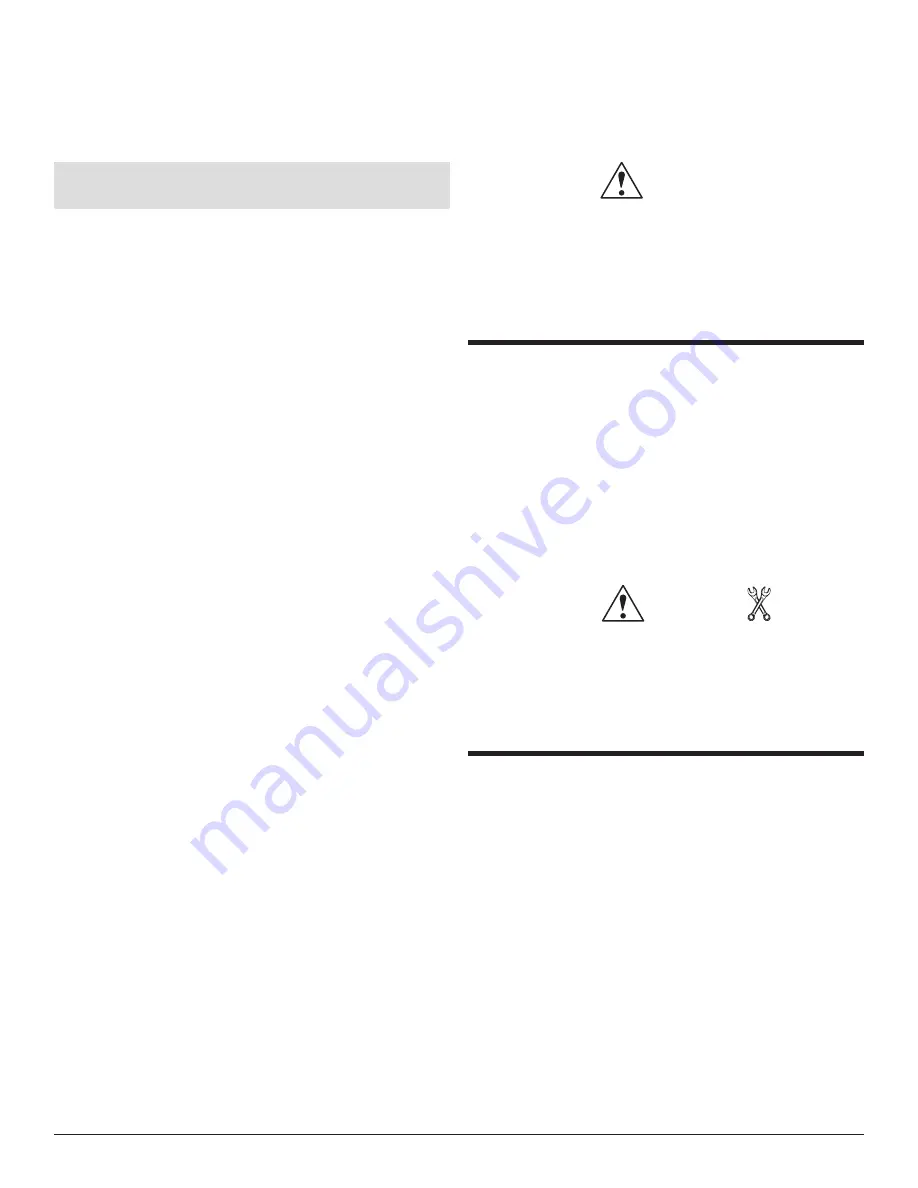
68
S
ection
8
1. Remove left and the right freezer evaporator
plate bolts along with the washers.
2. Remove seven bolts from fin assembly.
3. Unclip the thermistor from the fin assembly.
—Water dispenser units
a. Remove the paddle assembly.
b. Remove the water dispenser cover.
c. Disconnect the spigot.
d. Disconnect the wiring and remove the
bracket containing the LED board, spigot,
and switch as an assembly.
It is not possible to anticipate all of the RV
manufacturers enclosure design or refrigerator
installations practices.
Always, double check for additional screws
and brackets before attempting to remove the
refrigerator from the enclosure as certain RV
manufacturers may install additional brackets
or screws to secure the top and the sides of
the refrigerator to the enclosure.
Tools:
1/4" nut driver
5/16" nut driver
7/16" open end wrench
9/16" open end wrench
5/8" open-end wrench
#2 Phillips screwdriver
IMPORTANT
Cooling System Removal
Cooling system replacement requires removing
the refrigerator from the enclosure.
Protect the front of the refrigerator! Cover
the floor with a moving blanket/pad or
similar soft material to protect the floor as
well as the refrigerator doors panels and
optical display when the refrigerator is laid
down on the floor.
CAUTION
4. With the assistance of an able person, lay
the refrigerator on the floor doors side down.
5. Disconnect and remove the water valve
assembly. See Section 10 for information on
the ice maker water valve and the ice maker/
water dispenser water valve.
WARNING
Always use two wrenches to loosen
or tighten fittings to prevent damaging
components, piping, or fittings. Damaged
components, piping, or fittings create the
potential for gas leaks.
6. Disconnect and remove the gas valve
assembly (with bracket). See Section 5 for
information on gas valve connections and
fittings.
7. Disconnect and remove the spark/sense
electrode assembly.
8. Remove the power board cover then
disconnect the AC heaters leads and the
high temperature limit switch leads.
9. Disconnect and remove fans.
10. Disconnect fan wiring from thermostatic
switch and remove switch.
Summary of Contents for 121X series
Page 2: ...This page intentionally left blank...
Page 10: ...8 Section 2 This page intentionally left blank...
Page 96: ...94 Section 12 Section 12 Wiring Diagrams and Pictorials Figure 12 1 Wiring diagram...
Page 97: ...Section 12 95 Figure 12 2 Wiring pictorial...
Page 99: ...Section 12 97 This page intentionally left blank...