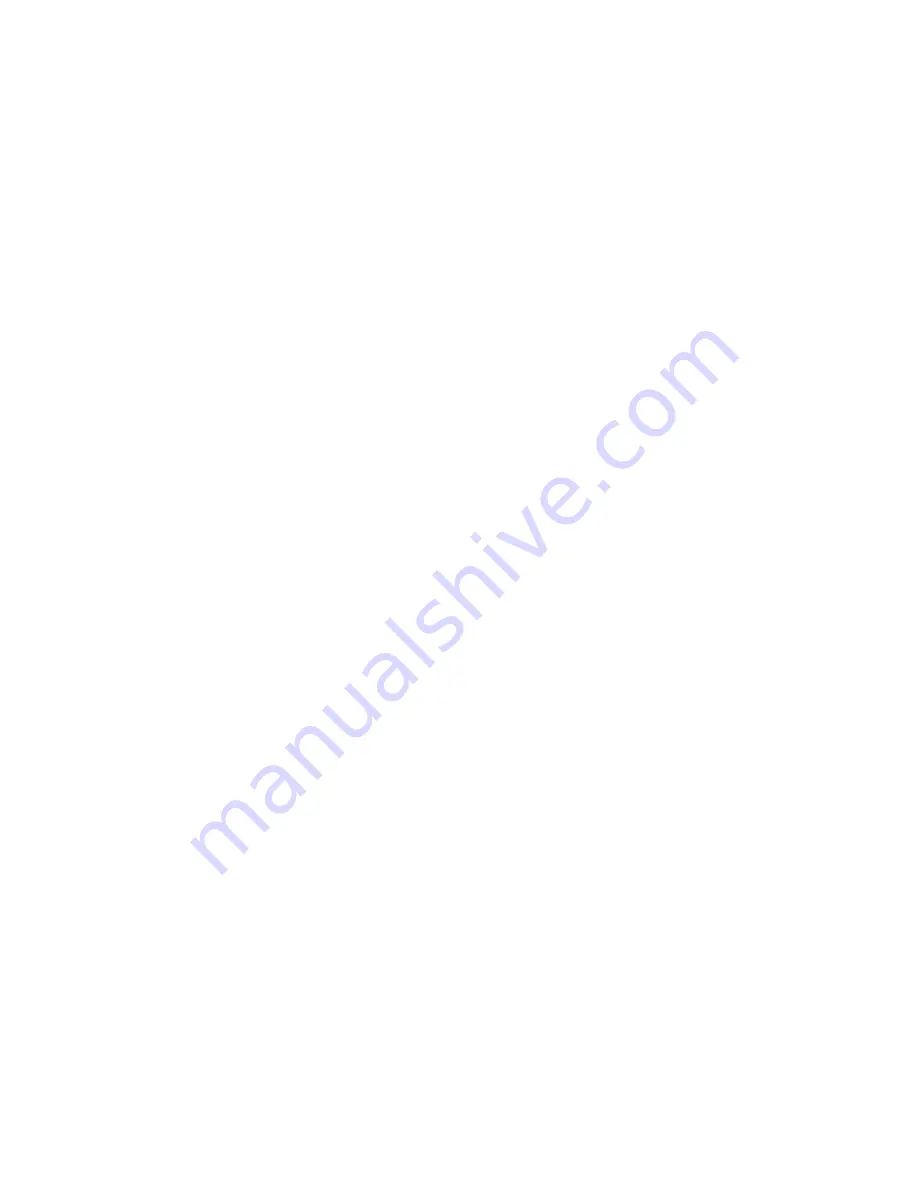
Table of Contents
1 INTRODUCTION.................................................................................................... 2
2
CHECK YOUR SOFTWARE VERSION ............................................................. 2
3 OPERATOR
SAFETY ............................................................................................ 3
4
GENERAL SYSTEM DESCRIPTION .................................................................. 4
4.1 I
NSTALLATION
.......................................................................................5
4.2 S
ENSORS
................................................................................................5
4.3 M
OUNTING THE
C
ENTER
S
ENSOR
..........................................................7
4.3.1
Turning the Center (Main lift Section) Off....................................7
4.3.2
Adjust the Sensor Offset................................................................8
4.3.3
Add an Additional Sensor .............................................................8
4.4 P
OWER
C
ABLE
.......................................................................................9
4.5 S
ENSOR
C
ABLES
..................................................................................10
4.6 C
ONTROL
P
ANEL
.................................................................................10
4.6.1 LCD
Screen.................................................................................11
4.6.2
SENSOR DISPLAY/SETUP Switch (NO)....................................11
4.6.3
The +/- switch .............................................................................11
4.6.4 AUTO/MANUAL
switch
(YES) ...................................................12
4.6.5 POWER
switch............................................................................12
4.7 R
EMOTE
C
ONTROLS
............................................................................12
5 SYSTEM
OPERATION ........................................................................................ 13
5.1 T
YPICAL
O
PERATION
...........................................................................13
5.1.1
Using the Toggle Switches..........................................................15
5.1.2
Change to Automatic or Manual Mode.......................................15
5.1.3
Adjust the Target Height (Setpoint) ............................................16
5.1.4
View the Actual Boom Height.....................................................16
5.1.5
Change the Sensitivity of the System (SENSI).............................16
5.1.6
Change Between SOIL and CROP mode ....................................16
5.2 U
NDERSTANDING
P
ERFORMANCE
I
SSUES
............................................17
5.3 U
NDERSTANDING
C
ROP
M
ODE
............................................................20
5.4 M
ENU
N
AVIGATION
.............................................................................22
5.4.1
Normal Operating Screen...........................................................22
5.4.2
Main Menu Overview..................................................................23
5.4.3
Menu Structure Map ...................................................................24
6 SYSTEM
SETUP ................................................................................................... 25
6.1 I
NITIAL
P
OWER
U
P
..............................................................................25
6.2 I
NSTALL
...............................................................................................25
6.3 R
E
T
UNE
...............................................................................................26
6.4 L
EVELING
C
HAINS
...............................................................................26
6.5 AUTOMATIC
SYSTEM
SETUP.......................................................27
6.6 MANUAL
SYSTEM
SETUP .............................................................40
6.6.1
Setting Up Sensors......................................................................40
6.6.2
Setting Up Hydraulic Valves.......................................................42
6.6.3
Turning Booms OFF or ON........................................................46
6.6.4
"Other ?" SETUP Options ..........................................................46
Summary of Contents for UC4 Total Control
Page 36: ...34 ...
Page 58: ...NOTES ...