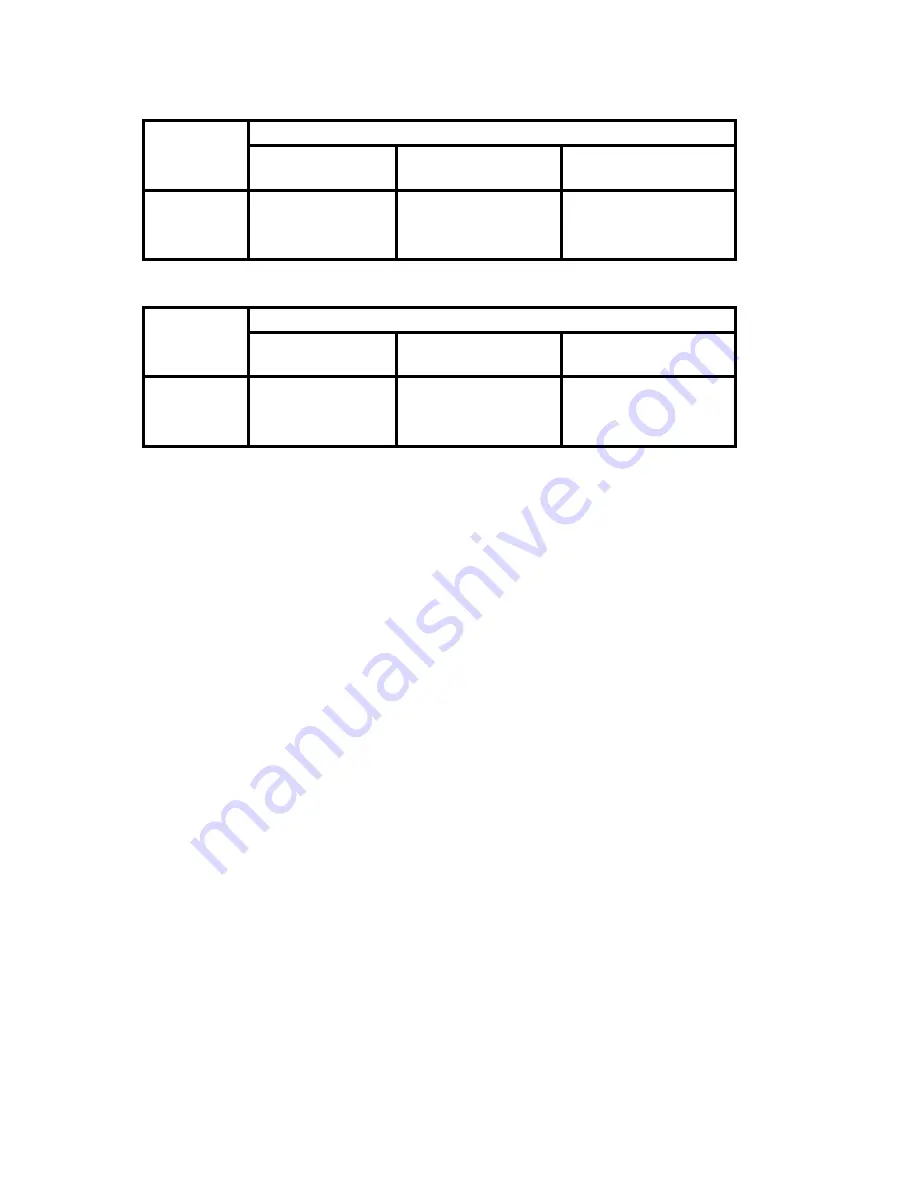
11
M2000
Parameter
Number
Net Capacity x Divisions
8000 x 2 kg
12,000 x 2 kg
15,000 x 5 kg
3 2
2
5
4** 8400
12600
15750
6 1
1
1
Table 2 - Parameter Settings (Metric units)
M2000
Parameter
Number
Net Capacity
10,000 x 2 lb
20,000 x 5 lb
60,000 x 10 lb
3 2
5
10
4** 10500
21000
63000
6
1 kg
0
0
Table 3 - Parameter Settings (US units)
Notes:
* Set parameter 30 to 3 for ticket printers. Set parameter 30 to 6 for roll
printers.
** Values listed are maximum settings. Parameter 4 may be set anywhere
from net capacity plus one division up to the maximum setting.