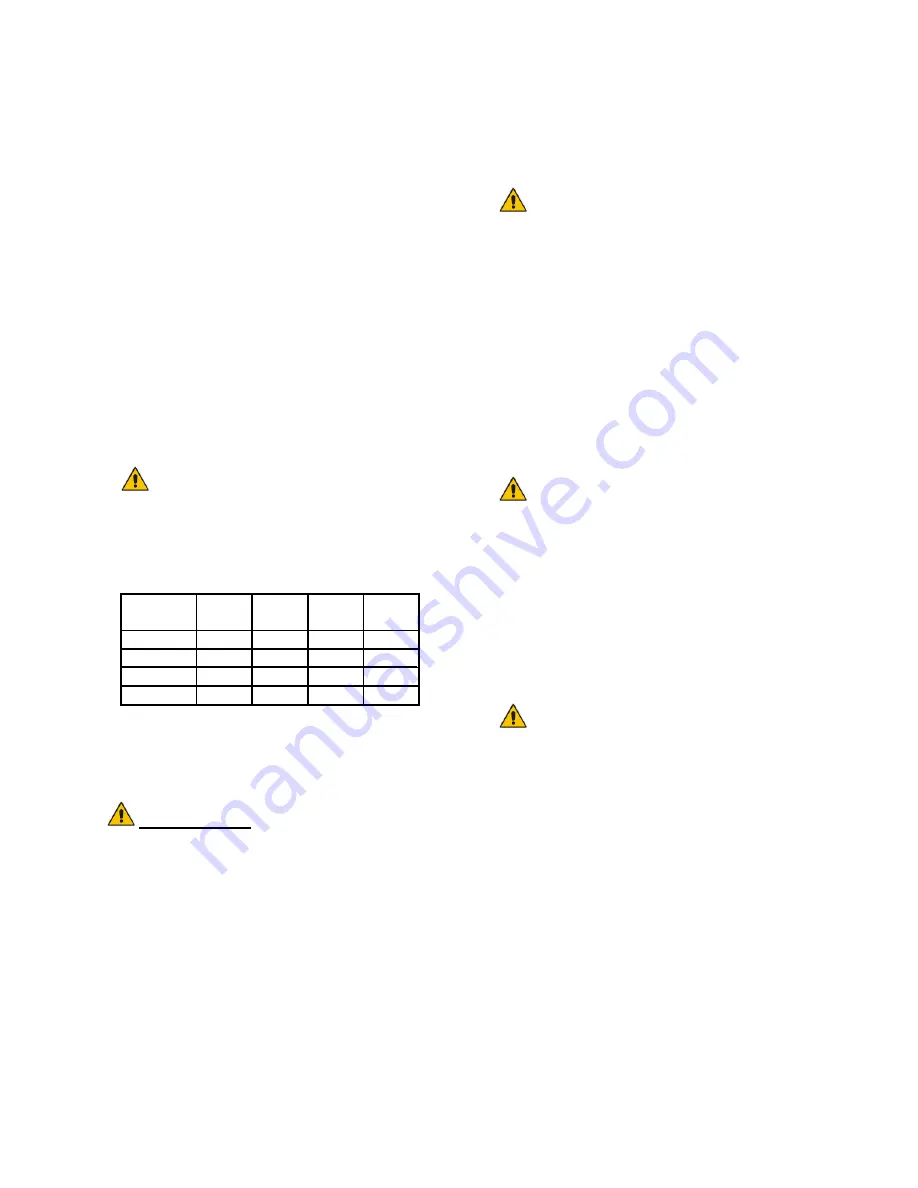
8
4
INSTALLATION PROCEDURE
4.1 E
XISTING SYSTEM CHECK
It is necessary to check the existing system’s
functionality before installing the UC4+
Spray Height Control system.
1.
Drive your sprayer onto a flat piece of
land, with unobstructed boom movement
(e.g. no power lines).
2.
Test that all boom functions operate
correctly. As you test each function
check it off in
Table 3
.
It is necessary to test the boom
functions in all directions
Table 3 – Hydraulic System Function
Check Sheet
BOOM
FOLD
IN
FOLD
OUT
UP
DOWN
LEFT
MAIN
RIGHT
ROLL*
N/A
N/A
*
Some sprayers may not have this function.
4.2 B
OOM
S
PEED
T
EST
IMPORTANT:
Raise/lower all boom sections several
times to warm up the hydraulic system.
Grease all moving parts for consistent
results.
1.
Lower each boom and main section as
close to the ground as possible.
2.
Set your sprayer at field working RPM
on the throttle and mark this value in
Table 4
You will need a stopwatch or a
watch that displays “seconds” for
the next step.
3.
Raise the LEFT boom from its extreme
LOW position to the very TOP of its
travel. Record the time this takes in
Table 4
“Trial #1” for “Left UP”.
4.
Lower the LEFT boom from its extreme
HIGH position to the BOTTOM of its
travel. Record this time in
Table 4
,
Trial #1, for “Left DOWN”.
Be careful when lowering the
booms so they don’t hit the
ground.
5.
Similarly, record two more time trials
(Trial #2 & #3) for the LEFT boom and
record in
Table 4
.
6.
Repeat Steps
1
through
5
for the RIGHT,
MAIN and ROLL functions.
Your sprayer may not have a roll
feature.
7.
Average the three trials recorded for
each boom movement and record this
calculation in the “Average Time” slot in
Table 4
.
8.
These “Average Times” now represent
how quickly your system can react to
manual control. In
Section 4.10
, this
procedure is repeated with the UC4+
Spray Height Control system installed
for comparison and troubleshooting
purposes.
Summary of Contents for Gregson Maverick 120 Series
Page 9: ...7 Figure 3 Hydraulic Components ...
Page 14: ...12 Figure 9 Sensor Serial Number Installation Location 3 SENSOR SYSTEM 5 SENSOR SYSTEM ...
Page 32: ...30 5 3 ITEM C02B 44664 CABLE UC4 CAN NODE DUAL 5 4 ITEM C03 44656 VALVE CABLE VARIABLE RATE ...
Page 33: ...31 5 5 ITEM C04 44651 VALVE EXTENSION CABLE ...
Page 34: ...32 5 6 ITEM C10 44650 11 POWER CABLE GREGSON MAVERICK ...