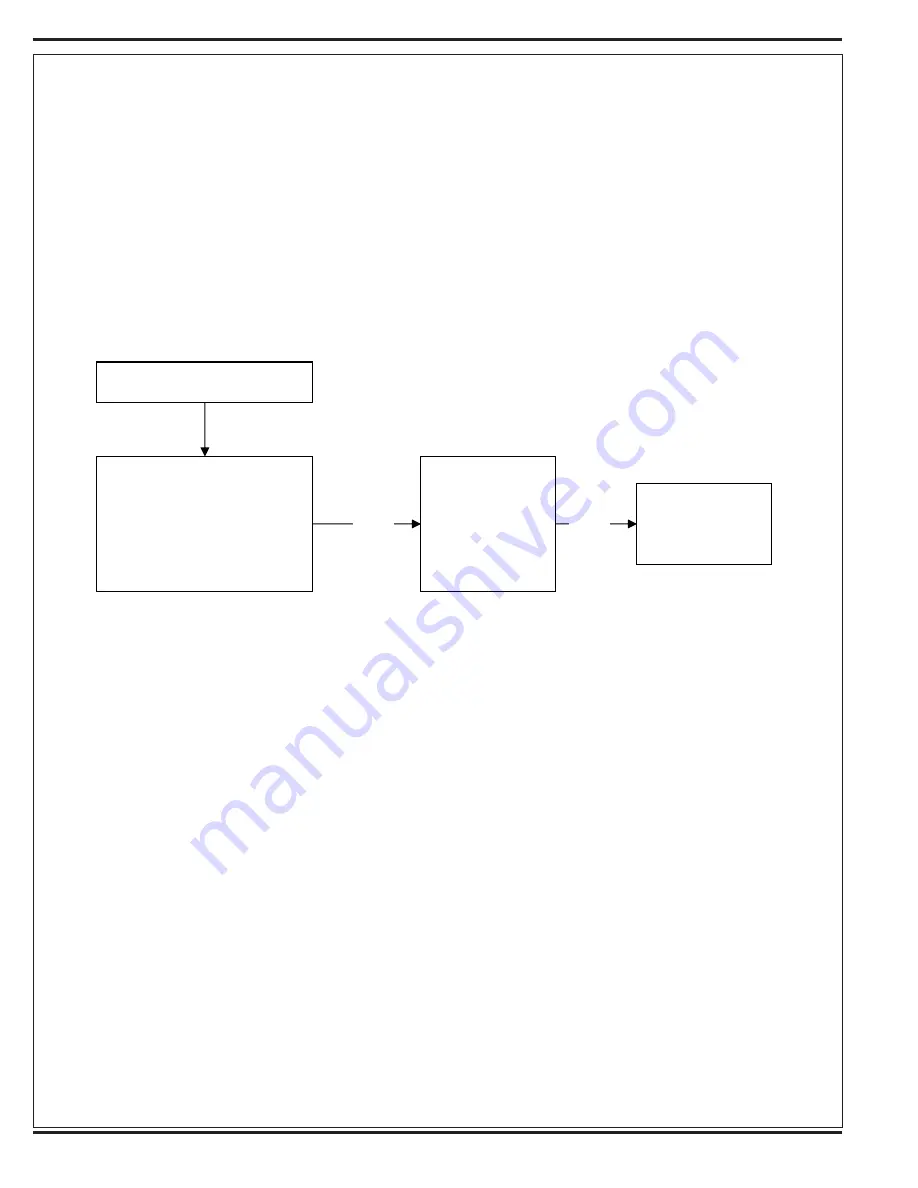
36
- FORM NO. 56043129 - SR 1900
SWEEPING SYSTEM
TROUBLESHOOTING GUIDE
Troubleshooting Guide
Symptom
Side broom motor(s) will not run
Part B: Hydraulic Load Circuit
Note 1: Do all testing with the engine running at high speed, the main broom lowered (sweep
position) and the drive pedal activated (machine moving). When the above steps are
completed the side broom(s) will lower automatically and turn ON (rotate).
Note 2: By pressing the control panel side broom ON/OFF switch during sweeping the side
broom will be raised and turned OFF.
Side broom motor will not run
Remove the side broom L3
valve cartridge
•Inspect, clean and reinstall
Does the motor run ?
Substitute* or
replace the
defective L3 side
broom valve
cartridge.
Does the motor
run ?
Replace the
failed side
broom motor.
No
No
*Substitute valve cartridge numbers 3 & 7 they are the same and can be swapped to
help troubleshoot the system.
Summary of Contents for 56507009
Page 5: ...FORM NO 56043129 SR 1900 5...
Page 64: ...64 FORM NO 56043129 SR 1900 THIS PAGE IS INTENTIONALLY BLANK...
Page 76: ...76 FORM NO 56043129 SR 1900 ENGINE HARNESS FOR GM 1 6L GAS Petrol Tier 3 ELECTRICAL SYSTEM...
Page 77: ...FORM NO 56043129 SR 1900 77 ELECTRICAL SYSTEM ENGINE HARNESS FOR GM 1 6L LPG Tier 3...