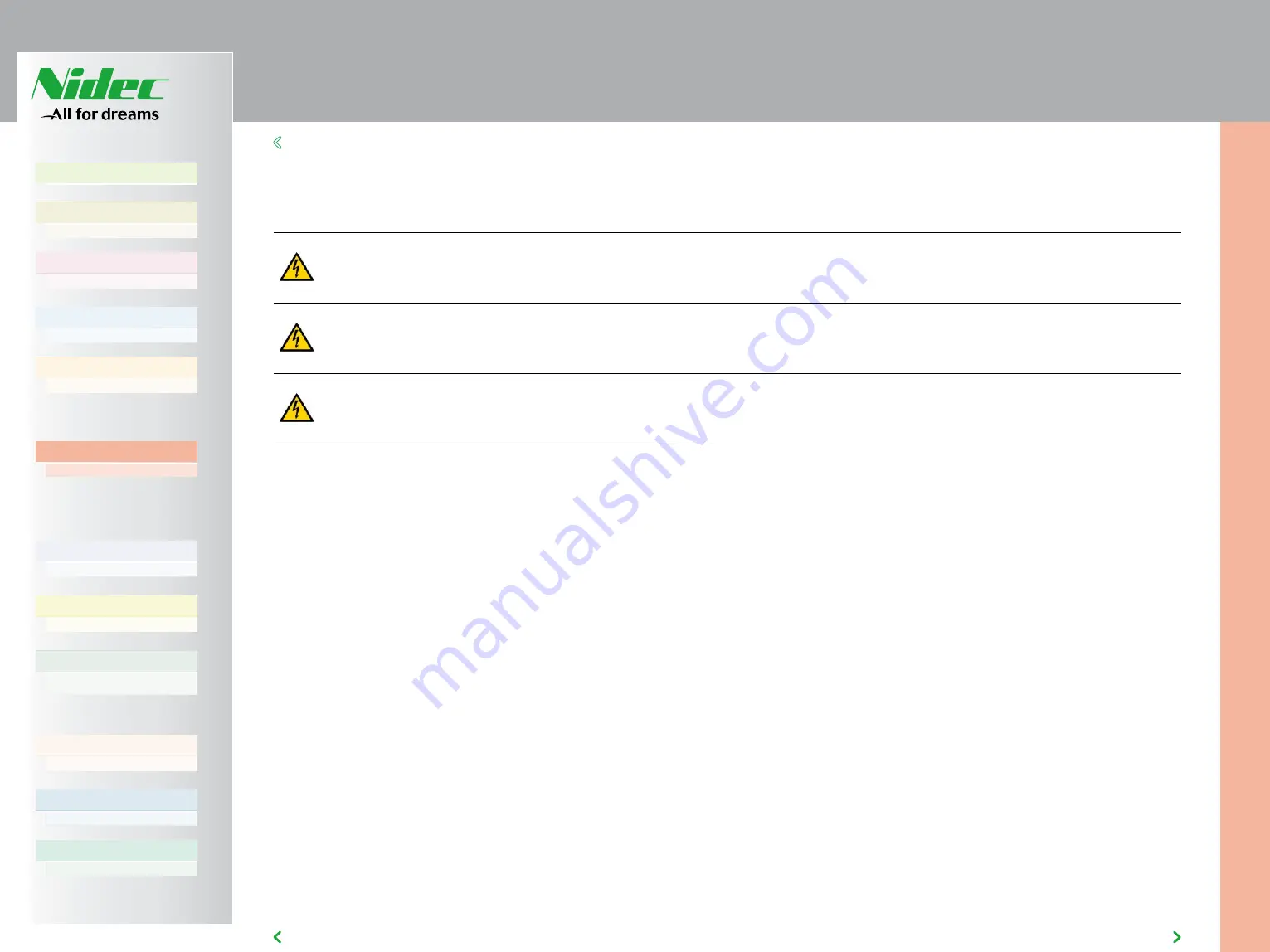
Summary
Chapter 1
P. 5
Chapter 2
P. 7
Chapter 3
P. 12
Chapter 4
P. 15
Chapter 5
P. 21
Chapter 6
P. 29
Chapter 7
P. 31
Chapter 8
P. 42
AD700E
21
General information
Important safety information
General Information and Ratings
Mechanical Installation
Operation
Parameters
Analog and Digital Input Macro
Configurations
Power Wiring
Chapter 9
P. 48
Chapter 10
P. 50
Modbus RTU Communications
Technical Data
Trouble Shooting
Chapter 11
P. 54
PREVIOUS VIEW
5 POWER WIRING
5
5 POWER WIRING
5.1 GROUNDING THE DRIVE
This manual is intended as a guide for proper installation. NIDEC INDUSTRIAL SOLUTIONS cannot assume responsibility for the compliance or the non-
compliance to any code, national, local or otherwise, for the proper installation of this drive or associated equipment. A hazard of personal injury and/
or equipment damage exists if codes are ignored during installation.
This AD700E contains high voltage capacitors that take time to discharge after removal of the main supply. Before working on the drive, ensure
isolation of the main supply from line inputs. Wait ten (10) minutes for the capacitors to discharge to safe voltage levels. Failure to observe this
precaution could result in severe bodily injury or loss of life.
Only qualified electrical personnel familiar with the construction and operation of this equipment and the hazards involved should install, adjust,
operate, or service this equipment. Read and understand this manual and other applicable manuals in their entirety before proceeding. Failure to
observe this precaution could result in severe bodily injury or loss of life.
Grounding Guidelines
The ground terminal of each AD700E should be individually connected
DIRECTLY to the site ground bus bar (through the filter if installed).
AD700E ground connections should not loop from one drive to another,
or to, or from any other equipment. Ground loop impedance must confirm
to local industrial safety regulations. To meet UL regulations, UL approved
ring crimp terminals should be used for all ground wiring connections.
The drive Safety Ground must be connected to system ground. Ground
impedance must conform to the requirements of national and local
industrial safety regulations and/or electrical codes. The integrity of all
ground connections should be checked periodically.
Protective Earth Conductor.
The Cross sectional area of the PE Conductor must be at least equal to
that of the incoming supply conductor.
Safety Ground
This is the safety ground for the drive that is required by code. One of
these points must be connected to adjacent building steel (girder, joist), a
floor ground rod, or bus bar. Grounding points must comply with national
and local industrial safety regulations and/or electrical codes.
Motor Ground
The motor ground must be connected to one of the ground terminals
on the drive.
Ground Fault Monitoring
As with all drive's, a leakage current to earth can exist. The AD700E
is designed to produce the minimum possible leakage current whilst
complying with worldwide standards. The level of current is affected by
motor cable length and type, the effective switching frequency, the earth
connections used and the type of RFI filter installed. If an ELCB (Earth
Leakage Circuit Breaker) is to be used, the following conditions apply:
• A Type B Device must be used
• The device must be suitable for protecting equipment with
a DC component in the leakage current
• Individual ELCBs should be used for each AD700E