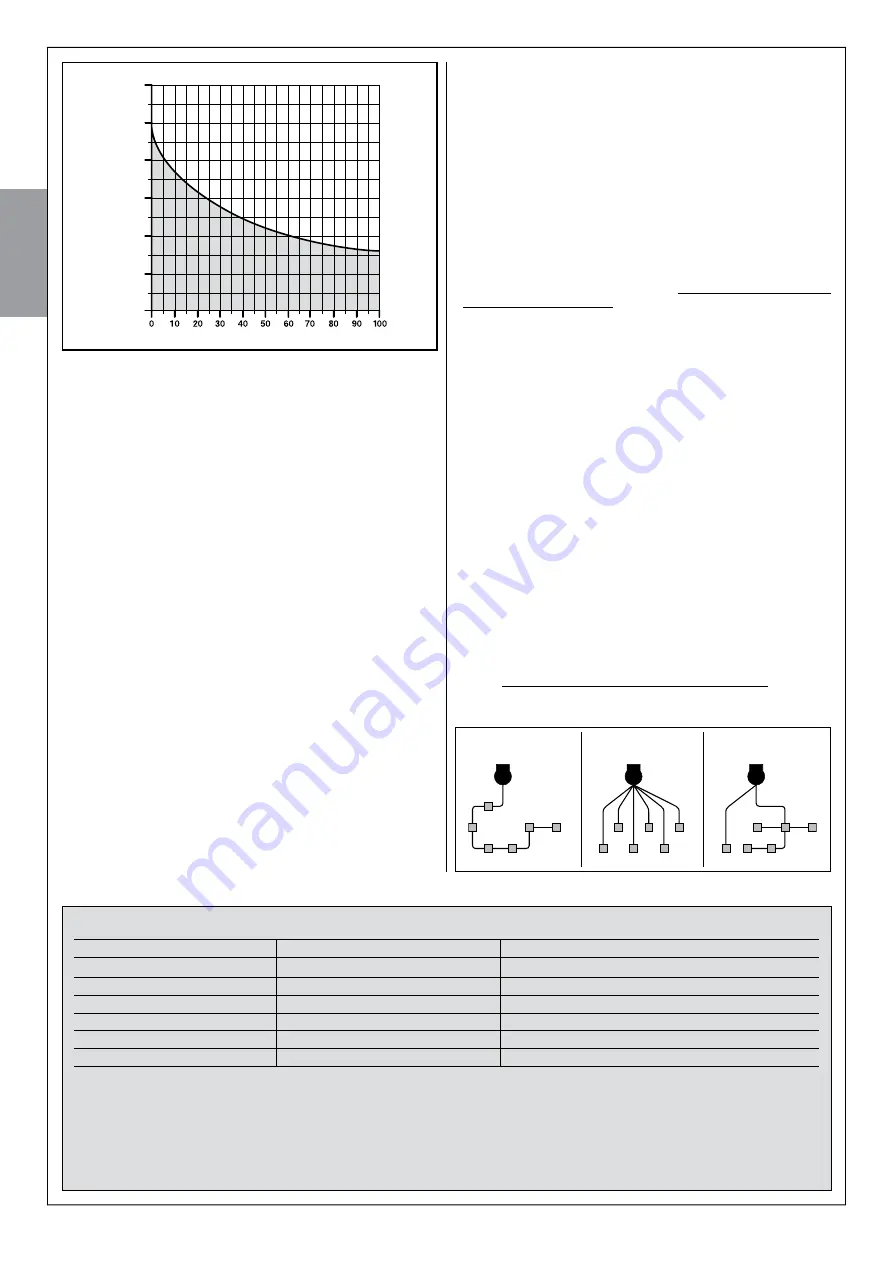
English
4
4.1.2 - Establish the position of all connection cables
Refer to the instructions in paragraph 4.2 to establish the layout of the
raceways for electric cable ducting.
4.1.3 - Ensure all equipment and materials for work are available
Before starting work, ensure that you have all equipment and materials
required to complete the work. Ensure that all items are in good condition
and comply with local safety standards.
4.1.4 - Completing the set-up work
Prepare the area for subsequent installation of the devices, completing all
preliminary work, such as:
- digging of raceways for protection ducting of electric cables (external
ducting may be used as an alternative);
- laying of protection ducting and embedding in concrete;
- sizing of all electric cables to required length (see paragraph 4.2) and
routing in protection ducting.
Caution! - In this phase, do not make
any electrical connections.
Warnings
:
• The hoses and ducting serve to protect electrical cables and prevent
accidental damage in the event of impact.
• When laying pipelines, take into account the risk of possible deposits of
water in the branch wells, where condensate may form in the pipelines
and the control unit with possible damage to the electronic circuits.
• Position the ends of the ducting at the points envisaged for fixture of the
various components.
4.2 - PREPARARING ELECTRIC CABLES
To prepare all connection cables, proceed as follows.
a)
- Refer to
fig. 4
to check the connections of the various devices to the
control unit and terminals to be used for each connection.
Important
-
Only devices using “ECSbus” technology can be connected to the
terminal “ECSbus”.
b)
- Refer to
fig. 3
to check positions of the electrical cables in the area.
Then draw a similar diagram on paper, adapting it to specific require
-
ments of your system.
Note -
This diagram will be useful to establish
the route of the raceways for cable ducting, and to draw up a com-
plete list of the cables required.
c)
- Read
Table 1
to determine the type of cables to be used; then refer
to the diagram drawn above and on-site measurements to determine
the length of each cable.
Caution! - No cable must exceed the
specific maximum length stated in Table 1.
WARNING -
“ECSbus” technology enables the interconnection of devic
-
es using a single “bus” cable, with 2 internal electrical wires. Connection
of several devices can be in the configuration “
cascade
”, “
star
” or the
latter two “
combined
”:
––– STEP 4 –––
4.1 - PRELIMINARY CHECKS FOR INSTALLATION
4.1.1 - Establish the position of devices in the system
With reference to
fig. 3
and
4
, locate the approximate position for installa
-
tion of each device envisaged in the system.
Fig. 3
shows a system made
using this product and other optional accessories in the Mhouse range.
These elements are positioned according to a typical standard layout. The
components are:
a
- SL1SC/SL10SC gearmotor with control unit
b
- Pair of PH100 photocells
c
- FL100 flashing light with integrated aerial
d
- Pair of posts for PT50 photocells (not supplied)
e
- Closure mechanical stops
f
- Floor-mounted track
g
- “Opening” limiter bracket
h
- CR100 rack (not supplied)
i
- KS100 key-operated selector switch
l
- “Closing” limiter bracket
WARNING! - Some of these devices are optional and may not be
present in the kit (see the Mhouse product catalogue).
WARNINGS:
• The gearmotor must be anchored to the ground, laterally to the gate
using the relative fixing plate.
• The fixed control devices must be positioned:
- in sight of the automation;
- far from moving parts;
- at a height of at least 1.5 m from the ground,
- not accessible by the public.
TABLE 1 – Technical specifications of electric cables
Connection
Type of cable
(minimum section values)
Max. admissible length
A
- Power line
Cable 3 x 1,5 mm
2
30 m
(note 1)
B
- FLASH flashing light output
Cable 2 x 0,5 mm
2
20 m
C
- Radio aerial
RG58 shielded cable type
20 m (less than 5 m recommended)
D
- Input/Output ECSbus
Cable 2 x 0,5 mm
2
20 m
(note 2)
E
- STOP input
Cable 2 x 0,5 mm
2
20 m
(note 2)
F
- OPEN input
Cable 2 x 0,5 mm
2
20 m
(note 2)
Note 1
- If the power cable is longer than 30 m, a cable with a larger section is required (e.g. 3 x 2.5 mm
2
) and safety earthing is necessary in
the vicinity of the automation.
Note 2
- For cables of ECSbus and those of the STOP and OPEN inputs, a single cable with multiple internal wires may be used, to combine
several connections: for example, the STOP and OPEN inputs can be connected to the KS100 selector switch with a cable of 4 x 0.5 mm2
2
.
ATTENZIONE! – The cables used must be suited to the installation environment: for example a cable type H03VV-F is recommen
-
ded for indoor environments, and a cable type H07RN-F for outdoor environments is recommended.
cascade
star
combined
50.000
100.000
150.000
200.000
250.000
300.000
GRAPH 1
Severity index (%)
manoeuvre
cycles
Summary of Contents for MhouseKit SL10S
Page 2: ......
Page 7: ...Fran ais 7 2 300 163 295 84 4 E D A F D B D C D 3 i d e g h a d b b c f l 1 A C D E F B G...
Page 9: ...Fran ais 9 5 7 8 9 10 0 50 moteur fix gauche moteur fix droite 6 36 50 0 50 50...
Page 10: ...Fran ais 10 11 12 14 13 170 170 1 200 200...
Page 11: ...Fran ais 60 11 16 18 19 17 10 0 50 0 50 10 moteur fix gauche moteur fix droite 15 A...
Page 13: ...Fran ais 21 A B 6 mm x4 A B A B A B B B B 1 2 3 4 1 2 3 4 20 B C A 13 5 D E F 6...
Page 14: ...Fran ais 14 22 23 21 A B A B A B A B A B A B 5 6 7 8 9 11 12 10 A B A B 6 mm x4 A A A A 4...
Page 15: ...Fran ais 15 24 25 TX RX 26 FL100 PH100 KS100 A 28 27 A B...
Page 17: ...Fran ais 17 31 B A C 34 32 A A B 35 A B 30 A B 33 T1 T2 T3 T4...
Page 34: ......
Page 39: ...English 5 2 300 163 295 84 4 E D A F D B D C D 3 i d e g h a d b b c f l 1 A C D E F B G...
Page 41: ...English 7 5 7 8 9 10 0 50 motor fixed on left motor fixed on right 6 36 50 0 50 50...
Page 42: ...English 8 11 12 14 13 170 170 1 200 200...
Page 43: ...English 9 18 19 60 17 10 0 50 0 50 10 motor fixed on left motor fixed on right 15 A 16...
Page 45: ...English 11 21 A B 6 mm x4 A B A B A B B B B 1 2 3 4 1 2 3 4 5 20 6 B C A D E F...
Page 46: ...English 12 22 23 21 A B A B A B A B A B A B 5 6 7 8 9 11 12 10 A B A B 6 mm x4 A A A A 4...
Page 47: ...English 13 24 25 TX RX 26 FL100 PH100 KS100 A 28 27 A B...
Page 49: ...English 15 31 B A C 34 32 A A B 35 A B 30 A B 33 T1 T2 T3 T4...
Page 66: ......
Page 71: ...Italiano 5 2 300 163 295 84 4 E D A F D B D C D 3 i d e g h a d b b c f l 1 A C D E F B G...
Page 73: ...Italiano 7 5 7 8 9 10 0 50 motore fissato a sinistra motore fissato a destra 6 36 50 0 50 50...
Page 74: ...Italiano 8 11 12 14 13 170 170 1 200 200...
Page 77: ...Italiano 11 21 A B 6 mm x4 A B A B A B B B B 1 2 3 4 1 2 3 4 20 B C A 5 D E F 6...
Page 78: ...Italiano 12 22 23 21 A B A B A B A B A B A B 5 6 7 8 9 11 12 10 A B A B 6 mm x4 A A A A 4...
Page 79: ...Italiano 13 24 25 TX RX 26 FL100 PH100 KS100 A 28 27 A B...
Page 81: ...Italiano 15 31 B A C 34 32 A A B 35 A B 30 A B 33 T1 T2 T3 T4...
Page 98: ......
Page 103: ...5 2 300 163 295 84 4 E D A F D B D C D 3 i d e g h a d b b c f l 1 A C D E F B G...
Page 106: ...8 11 12 14 13 170 170 1 200 200 Polski...
Page 109: ...11 21 A B 6 mm x4 A B A B A B B B B 1 2 3 4 1 2 3 4 20 B C A 5 D E F 6 Polski...
Page 110: ...12 22 23 21 A B A B A B A B A B A B 5 6 7 8 9 11 12 10 A B A B 6 mm x4 A A A A 4 Polski...
Page 111: ...13 24 25 TX RX 26 FL100 PH100 KS100 A 28 27 A B Polski...
Page 113: ...15 31 B A C 34 32 A A B 35 A B 30 A B 33 T1 T2 T3 T4 Polski...
Page 130: ......
Page 131: ......