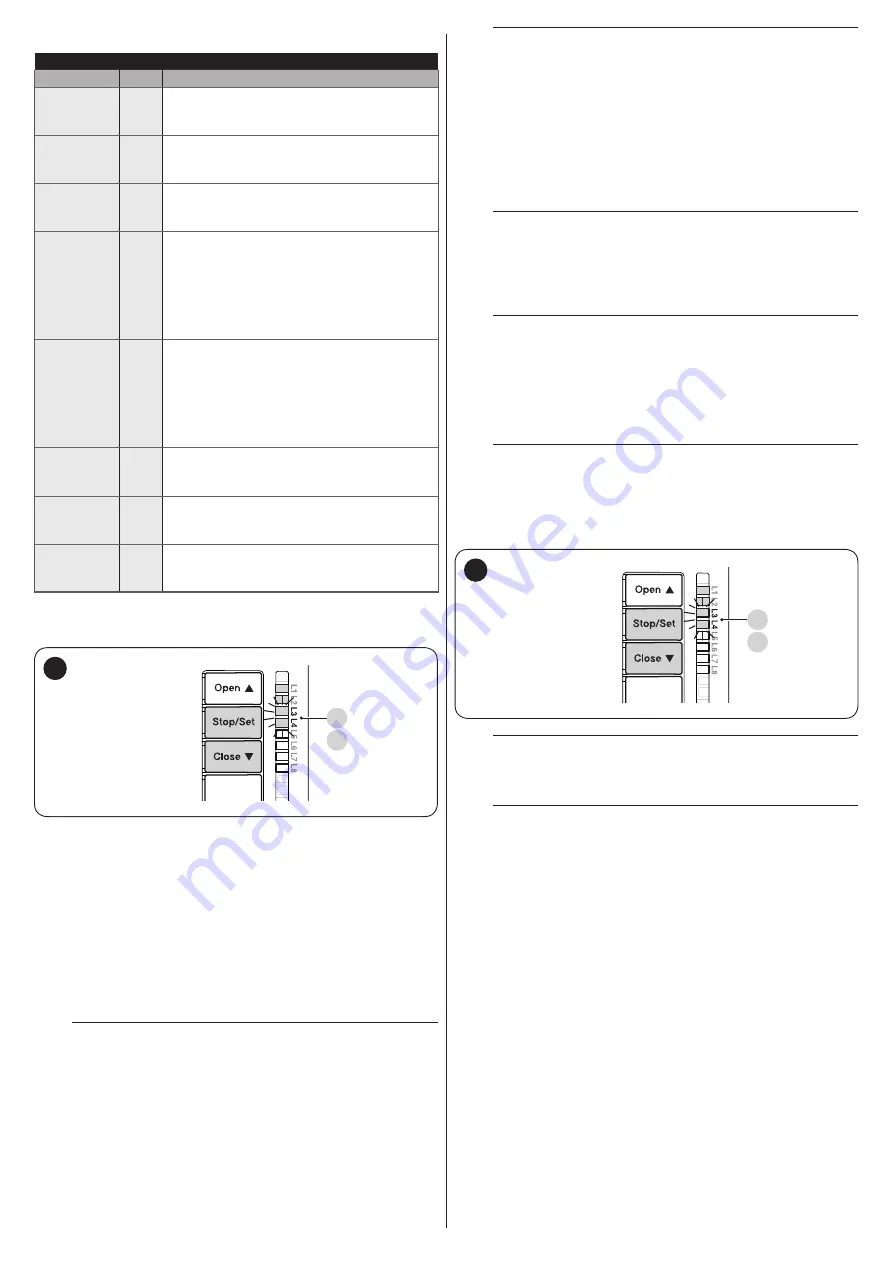
10
– ENGLISH
Table 5
PROGRAMMING POSITIONS
Position
LED
Description
Position 0
(motor 1)
L1
maximum closing position: when the leaf
relative to motor 1 strikes the closing
mechanical stop
Position 0
(motor 2)
L2
maximum closing position: when the leaf
relative to motor 2 strikes the closing
mechanical stop
Position SA
(motor 2)
L3
Offset on opening: when the leaf associated
with motor 2 moves beyond this position, leaf
1 will start to open
Position A
(motor 1)
L4
Desired opening position: position in which
the leaf associated with motor 1 must stop
at the end of an opening manoeuvre. This
position must not necessarily correspond
to the opening mechanical stop; it can be
chosen as desired between positions “0” and
“1”
Position A
(motor 2)
L5
Desired opening position: position in which
the leaf associated with motor 2 must stop
at the end of an opening manoeuvre. This
position must not necessarily correspond
to the opening mechanical stop; it can be
chosen as desired between positions “0” and
“1”
Position SC
(motor 1)
L6
Offset on closing: when leaf 1 is below this
position, leaf 2 will start to close
Position 1
(motor 1)
L7
Maximum opening position: when the leaf
relative to motor 1 strikes the opening
mechanical stop
Position 1
(motor 2)
L8
Maximum opening position: when the leaf
relative to motor 2 strikes the opening
mechanical stop
4.8.1 Learning in automatic mode
L3
L4
15
To effect the automatic learning procedure:
1.
simultaneously press and hold the and
g
buttons
h
2.
release the buttons when LEDs
“L3”
and
“L4”
start flashing
quickly (after roughly 5 seconds)
3.
check that the automation carries out the following
manoeuvre sequences:
a.
slow closing of motor M1 up to the mechanical stop
b.
slow closing of motor M2 up to the mechanical stop
c.
slow opening of motor M2 and of motor M1 up to the
stop
d.
fast closing of motors M1 and M2.
m
If the first manoeuvre (a) fails to close the leaf
controlled by motor M1 but closes the one
controlled by M2, press
f
or
h
to
stop the learning phase. At this point, reverse the
connections of motors M1 and M2 on the terminals
on the control unit and those of the respective
encoders. Then repeat the self-learning procedure.
m
If the first two manoeuvres (a and b) are not “closing”
but “opening” manoeuvres, press the
f
or
h
button to stop the learning phase. At this
point, invert the control wires (external positions
with respect to the terminal) on the motor that
executed the opening manoeuvre and repeat the
self-learning procedure.
4.
at the end of the closing manoeuvre (
d
) of the two motors,
LEDs
“L3”
and
“L4”
switch off to signal that the procedure
was performed correctly.
m
If, during the automatic learning procedure, the
photocells or one of the devices connected to the
“stop” input intervene, the procedure interrupts and
LED L1 starts flashing. In this case, the self-learning
procedure must be repeated from the beginning.
l
The automatic learning procedure can be run
again at any time, even after the installation phase;
for example, after modifying the position of the
mechanical stops.
4.8.2 Learning in manual mode
m
The user has maximum 10 seconds to press
the buttons consecutively during the learning
procedure. After this time, the procedure terminates
automatically and memorises the changes made up
to that time.
L3
L4
16
l
When LEDs "L1..L8" flash, to shift between LEDs
simply press the
f
or
h
button briefly
(the LED will flash to signal the current position).
l
While LEDs "L1..L8" flash, to move the motor in any
one direction, it is necessary to press and hold the
f
or
h
button.
To effect the manual learning procedure:
1.
simultaneously press and hold the and
g
buttons
h
2.
release the buttons when LED
“L1”
starts flashing (after
roughly 3 sec)
3.
LED “
L1
” flashes:
position 0 of M1
–
to command and move motor 1 to
position “0”
(“
Figure
”): press and hold the
f
or
h
button.
Once the position is reached, release the button to stop
the manoeuvre
–
to memorise the position, press and hold the
g
button for at least 3 seconds then release it (after 2
seconds LED “
L1
” will remain lit and after the
g
button is released, LED “
L2
” will start flashing)
Summary of Contents for MC824HHS
Page 1: ...Nice MC824HHS Control unit EN Instructions and warnings for installation and use...
Page 24: ...24 ENGLISH NOTES...
Page 26: ...26 ENGLISH NOTES...
Page 27: ...ENGLISH 27 NOTES...