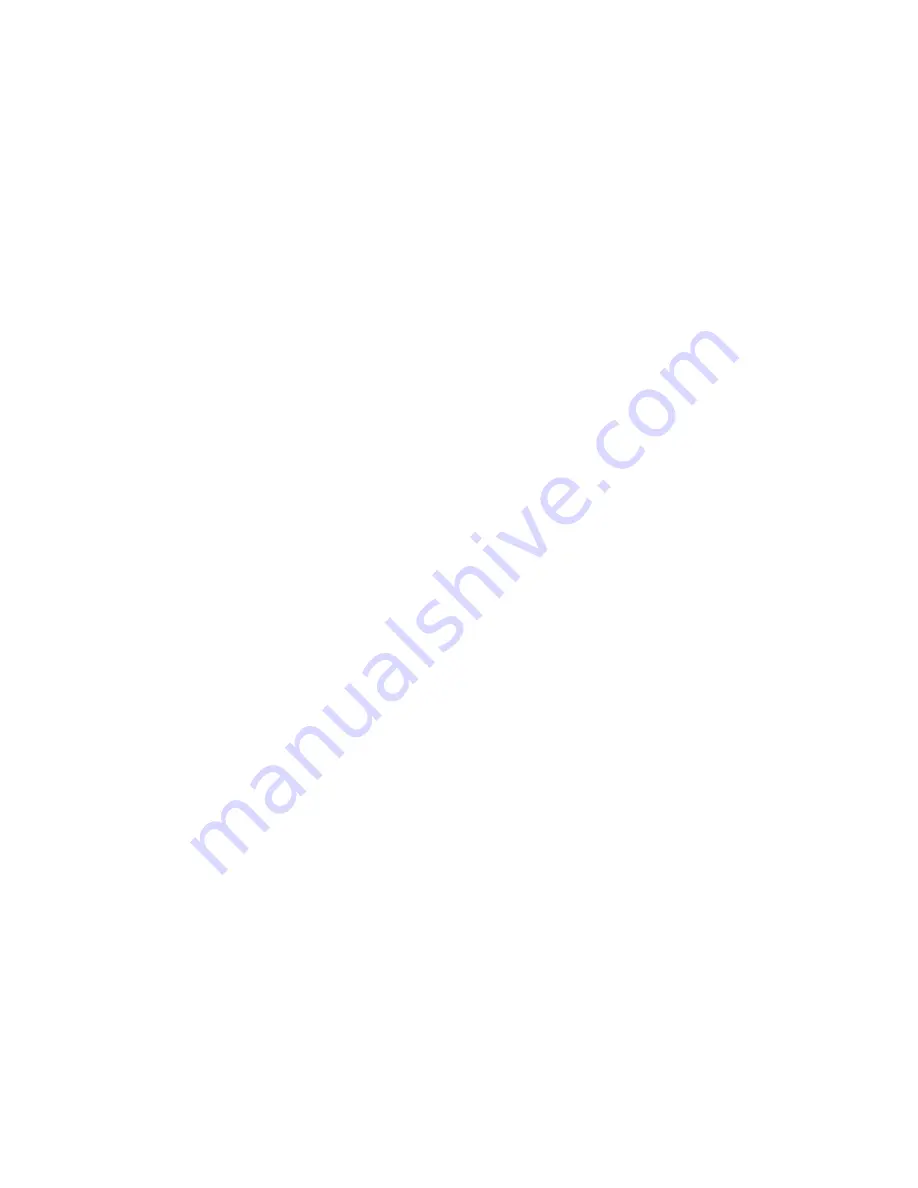
6
For safe operating procedures for solid fuel operation, refer to the notice label on the furnace.
The furnace room must have adequate air for combustion. If the unit is in a confined space, one
square inch of free air access for every 1,000 BTU must be provided.
Use a chimney suitable for solid fuel which must be kept free of accumulation of soot and ash
Accumulations of soot and ash not only create a fire hazard but cause poor efficiency
In case of a soot fire, move all thermostats to their lowest setting, close the barometric draft regulator
and call the fire department.
OIL BURNER OPERATING INSTRUCTIONS
GENERAL CARE
This burner is fully automatic. All adjustments have been carefully set and should not be changed. Keep
burner free from excess dirt and moisture.
Any oil leaks, however small, should receive immediate
attention. The oil filter should be cleaned once a year by the service man. The motor should be given a
few drops of light oil two or three times a year. No other parts require lubrication.
FUEL
The supply tank should be kept at least one-quarter full.
Outside underground storage tanks if not
equipped with a special gauge, are gauged by a stick. Recommended grade of fuel: No. 2 Furnace Oil.
CAUTION
1.
Do not use gasoline, crankcase or any oil containing gasoline
2.
Do not tamper with the unit or controls, call the service man
3.
Do not attempt to start burner when excess oil has accumulated, when the heating unit is full of
vapour, or when the combustion chamber is very hot
4.
Do not burn garbage or paper in heating system, and never leave paper or rags around the unit
HEATING PLANT
Give you heating unit the proper care and attention.
The use of a boiler as an incinerator is not
recommended. Heating unit flues should be kept clean for economical operation. Dampers are set by
installation men and should not be changed. Free ventilation must be permanently provided in the room
where the burner installation is made.
CONTROLS
The operation of the burner is normally controlled by room thermostat, which may be set for any
temperature desired, usually 20ºC (68ºF). If a higher or lower temperature is desired, the indicator should
be moved to the proper point on the scale. To shut down burner at any time, turn main switch to off
position.
SUMMER SHUT DOWN
When burner is not to be used during the summer months turn off burner main switch. If the heating unit
room is damp protect burner against dirt and moisture with light cover.
SAFETY SHUT-OFF
An emergency oil shut-off valve should be installed by local ordinance. Always keep the valve shut off if
the burner is shut down for an extended period of time.
SERVICE
If burner fails to run when the thermostat or other operating control is calling for heat, see that the main switch
is turned on and that fuses are not blown. Be sure there is oil in the supply tank and that the electric service to
the building has not been temporarily interrupted. Press button on burner control box one time only and if
burner still fails to start call the service man. A periodic inspection of the burner is recommended.
Summary of Contents for BC 160
Page 21: ...20 DIAGRAM 4 SECONDARY AIR OPENINGS LOW WATER CUT OFF FITTING...
Page 23: ...22 DIAGRAM 6 GENERAL ASSEMBLY...
Page 24: ...23 Diagram 7 FLUE PIPE CONNECTION Diagram 8 MINIMUM INSTALLATION CLEARANCES...
Page 25: ...24 Diagram 9 CONTROL PANEL...
Page 26: ...25 Diagram 10A FIELD WIRING...
Page 27: ...26 Diagram 10B FIELD WIRING WITH LOW WATER CUT OFF...
Page 28: ...27 Diagram 11...
Page 29: ...28 Diagram 13A...
Page 30: ...29 Diagram 13B...
Page 31: ...30 Diagram 14 WOOD ADD ON WIRING...
Page 32: ...31 Diagram 15A...
Page 33: ...32 Diagram 15B...
Page 34: ...33 Diagram 16A TYPICAL PIPING ZONING WITH CIRCULATORS...
Page 35: ...34 Diagram 16B TYPICAL PIPING ZONING WITH ZONE VALVES...
Page 36: ...35 Diagram 17 Diagram 18...
Page 37: ...36 Diagram 19 Diagram 20...
Page 38: ...37 Diagram 21 SHAKER GRATE INSTALLATION PROCEDURE...
Page 39: ...38 Diagram 22 GRATE INSTALLATION PROCEDURE Diagram 23 CASTING INSTALLATION...
Page 41: ...40 Diagram 24 SECONDARY AIR SYSTEM GENERAL ASSEMBLY...
Page 42: ...41 Diagram 25 SECONDARY AIR SYSTEM INSTALLATION...