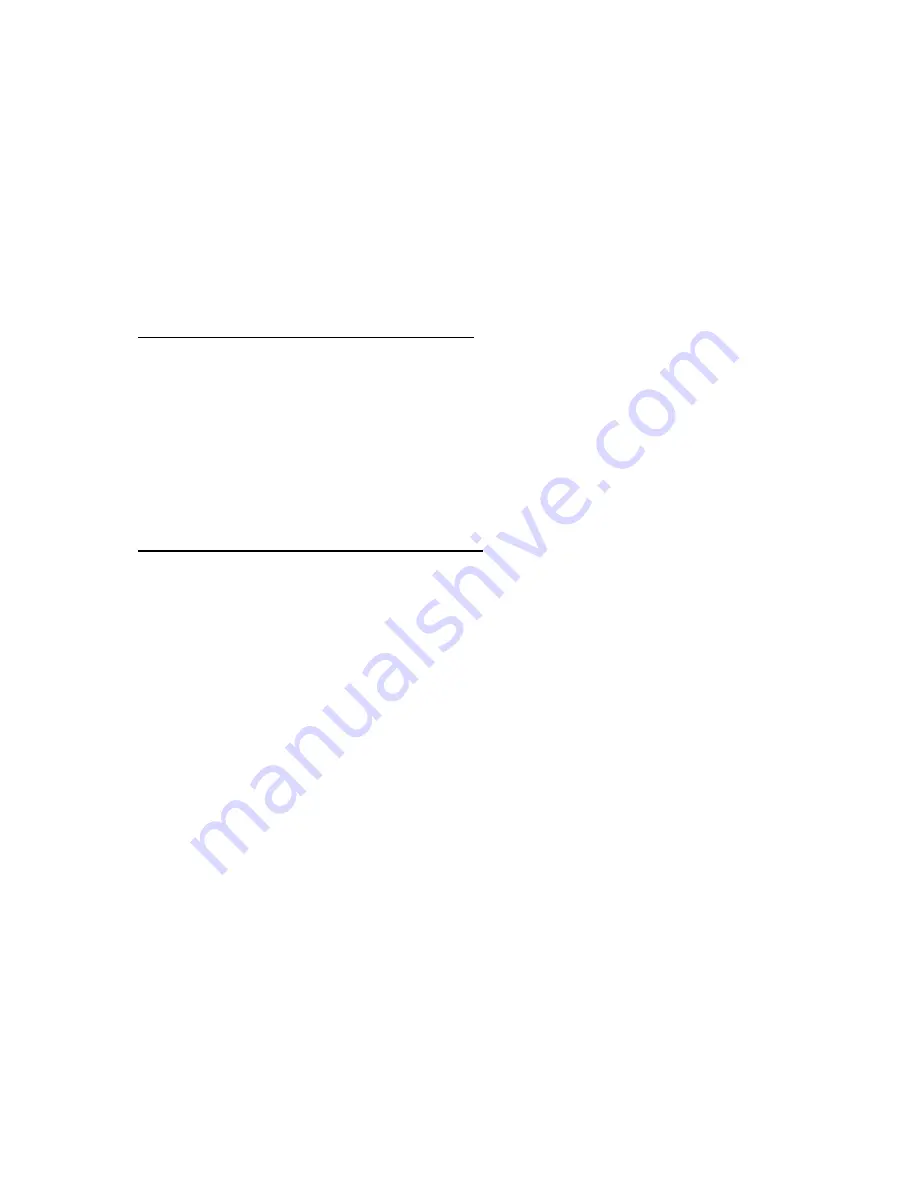
18
OIL FIRED BLOCKED VENT SWITCH - MODEL WMO-1
When installed on the oil chamber assembly according to these instructions, the manually reset WMO-1
blocked vent switch is designed to shut off power to the oil burner if the hot flue gases in the chimney vent
connector pipe back up sufficiently to activate it. The WMO-1 switch is required on new Newmac oil-fired
and combination furnaces or boilers installed in Canada. It must be installed by a qualified installer in
accordance with the manufacturer's installation instructions. Electrical wiring must be in accordance with
applicable codes and the Canadian Electrical Code.
Before leaving the appliance check that the WMO-1 switch and its cover are tightly secured.
Items supplied with this kit, Newmac Part 2040300:
Blocked Vent Switch Assembly-Model WMO-1
Installation on the Oil Chamber Assembly - Fig. 1A
-
Newmac combination wood/oil or coal/oil fired
boiler.
1.
Remove the 5/8" or 7/8 diameter plug or knockout in the oil chamber assembly. Drill at least four
9/64" diameter holes in the oil chamber assembly at the locations shown.
2.
Insert the heat transfer tube assembly (5) into the 5/8" or 7/8" diameter hole. Check that the heat
transfer tube assembly (5) is sealed against the oil chamber assembly by installing 4 metal screws
(7).
CAUTION
: Disconnect the electrical power supply before wiring the WMO-1 assembly.
3.
See Diagram #8: Using suitable AC90 flexible (BX) conduit or equivalent, wire the WMO-1 switch in
series with the appliance limit circuit. Connect at the appliance junction box.
4.
Check the operation of the WMO-1 switch before leaving the appliance. The WMO-1 switch is reset
by pushing the square red button.
Installation on the Oil Chamber Assembly - Fig. 1B -
Newmac combination wood/oil or coal/oil fired
boiler.
1.
Remove the 5/8" or 7/8 diameter plug or knockout in the oil chamber assembly. Remove one of the
securing nuts (7) from the tube of the WMO-1 assembly. Tighten the remaining nut (5) onto the tube
as far as possible.
2.
Insert the threaded tube end into the 5/8" diameter hole in the oil chamber assembly. Install the first
securing nut onto the tube on the inside of the oil chamber assembly. Tighten securely.
CAUTION
: Disconnect the electrical power supply before wiring the WMO-1 assembly.
3.
See Diagram #8 in the Installation, Operating and Service Manual. Using suitable AC90 flexible (BX)
conduit or equivalent, wire the WMO-1 switch in series with the appliance limit circuit. Connect at the
burner junction box.
4.
Check the operation of the WMO-1 switch before leaving the appliance. The WMO-1 switch is reset
by pushing the square red button.
WMO-1 Blocked Vent Switch Check
Note: take appropriate precautions - this test can produce soot,
smoke and fumes. The appliance should not be left unattended during the test.
1.
With the appliance shut down, block the vent pipe at the downstream (chimney) side of the
barometric damper.
2.
Start the appliance.
3.
The WMO-1 switch should stop the oil burner in less than 10 minutes.
4.
After the test, turn off the appliance and let it cool.
5.
Remove the blockage from the vent pipe.
6.
Reset the WMO-1 switch by pushing in the square red button until it clicks.
7.
Ensure that the appliance is in a safe condition.
Maintenance and Cleaning
The WMO-1 switch assembly should be checked and cleaned at least once a year and after any time the
switch has shut off the burner.
Cleaning procedure - See Figure 1A
1.
Switch off the electrical power to the appliance.
2.
Remove the WMO-1 cover (2).
Summary of Contents for BC 160
Page 21: ...20 DIAGRAM 4 SECONDARY AIR OPENINGS LOW WATER CUT OFF FITTING...
Page 23: ...22 DIAGRAM 6 GENERAL ASSEMBLY...
Page 24: ...23 Diagram 7 FLUE PIPE CONNECTION Diagram 8 MINIMUM INSTALLATION CLEARANCES...
Page 25: ...24 Diagram 9 CONTROL PANEL...
Page 26: ...25 Diagram 10A FIELD WIRING...
Page 27: ...26 Diagram 10B FIELD WIRING WITH LOW WATER CUT OFF...
Page 28: ...27 Diagram 11...
Page 29: ...28 Diagram 13A...
Page 30: ...29 Diagram 13B...
Page 31: ...30 Diagram 14 WOOD ADD ON WIRING...
Page 32: ...31 Diagram 15A...
Page 33: ...32 Diagram 15B...
Page 34: ...33 Diagram 16A TYPICAL PIPING ZONING WITH CIRCULATORS...
Page 35: ...34 Diagram 16B TYPICAL PIPING ZONING WITH ZONE VALVES...
Page 36: ...35 Diagram 17 Diagram 18...
Page 37: ...36 Diagram 19 Diagram 20...
Page 38: ...37 Diagram 21 SHAKER GRATE INSTALLATION PROCEDURE...
Page 39: ...38 Diagram 22 GRATE INSTALLATION PROCEDURE Diagram 23 CASTING INSTALLATION...
Page 41: ...40 Diagram 24 SECONDARY AIR SYSTEM GENERAL ASSEMBLY...
Page 42: ...41 Diagram 25 SECONDARY AIR SYSTEM INSTALLATION...