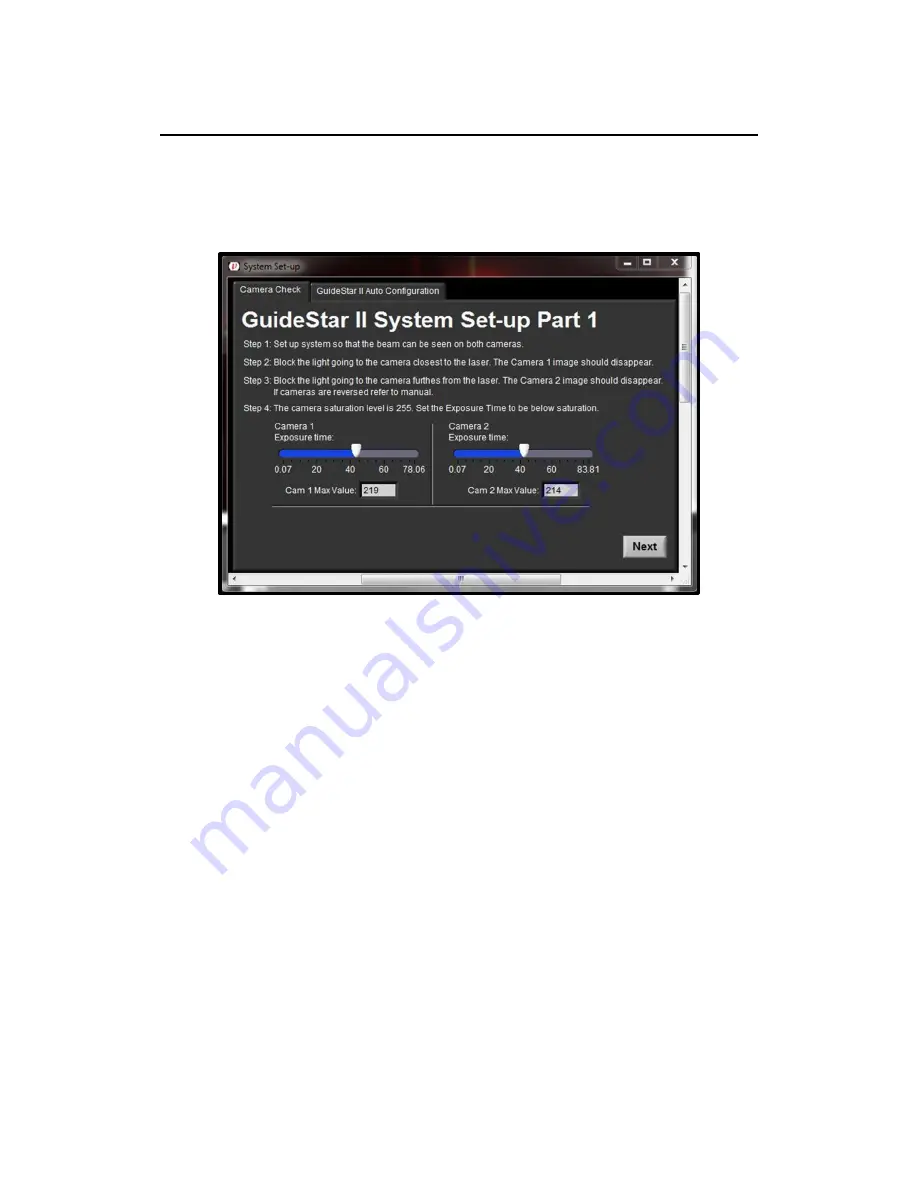
15
4.4
Software Operation
4.4.1
System Set-up
The first time the application is launched it will automatically open the System
Set-up window and display the Camera Check tab:
Figure 12. System Set-up window available through GuideStar II Tab.
This window cannot be closed until steps 1 - 4 are completed. If blocking the
beams to the Camera 1 causes the Camera 2 image to disappear in the GuideStar
II display (or vise-versa), then the camera IDs should be swapped. (For
instructions on how to do this, see Section 6: Frequently Asked Questions.)
Now, click “Next” or click on the “GuideStar II Auto Configuration” tab: