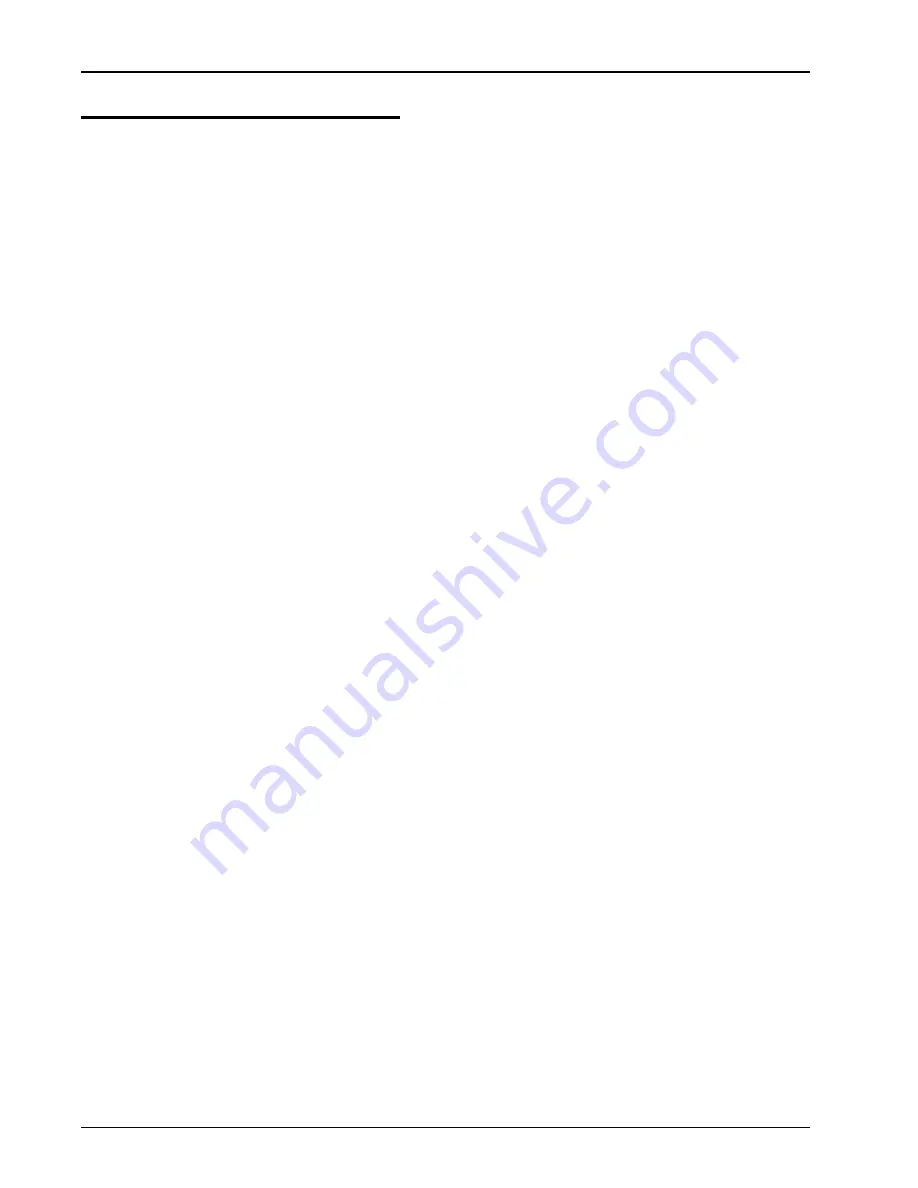
Introduction
2
TRU/FLO Compound Meter Installation and Maintenance Guide
TRU/FLO General Information
The following sections provide general information about the TRU/FLO
meter.
Operation
The hydraulic valve transfers flow smoothly between the disc section
and turbine section of the meter, minimizing the loss of accuracy in the
crossover range. The turbine measuring assembly registers medium and
high flows while the T-10
®
chamber registers low flows, ensuring
accurate measurement at all flow rates.
Construction
The TRU/FLO meter consists of a durable lead free, high-copper alloy
maincase, Neptune turbine measuring assembly, Neptune T-10 chamber,
and two magnetic-driven, roll-sealed registers.
The lead free, high-copper maincase is corrosion-resistant and easy to
handle.
A calibration vane allows field calibration of the
meter to lengthen
service life and to ensure accurate registration.
The two magnetic-driven, roll-sealed registers simplify the meter’s
design and reduce long-term maintenance.
Warranty
Neptune T-10 meters and Neptune T-10 nutating disc chambers in
TRU/FLO compound meters are warranted to meet or exceed new meter
accuracy standards of the
AWWA standard C700-95
for a period of:
•
Five years from date of shipment for 5/8-inch, ¾-inch, and 1-inch
meters.
•
Two years from the date of shipment for 1½-inch, and 2-inch
meters.
•
Or the applicable registration shown, in Table 1 on page 3,
whichever occurs first.
Neptune further guarantees that the Neptune T-10 and Neptune T-10
nutating disc chambers in the TRU/FLO compound meter performs to at
least repaired meter accuracy standards according to AWWA manual M-
6 chapter 5 for an additional 10 years or the registration shown in
Table 1 on page 3, whichever occurs first.
Summary of Contents for TRU/FLO
Page 2: ......
Page 3: ...TRU FLO Compound Meter Installation and Maintenance Guide...
Page 8: ...Notes Contents vi TRU FLO Compound Meter Installation and Maintenance Guide...
Page 12: ...x TRU FLO Compound Meter Installation and Maintenance Guide Notes Tables...
Page 44: ...Appendix A 32 TRU FLO Compound Meter Installation and Maintenance Guide Notes...
Page 57: ......