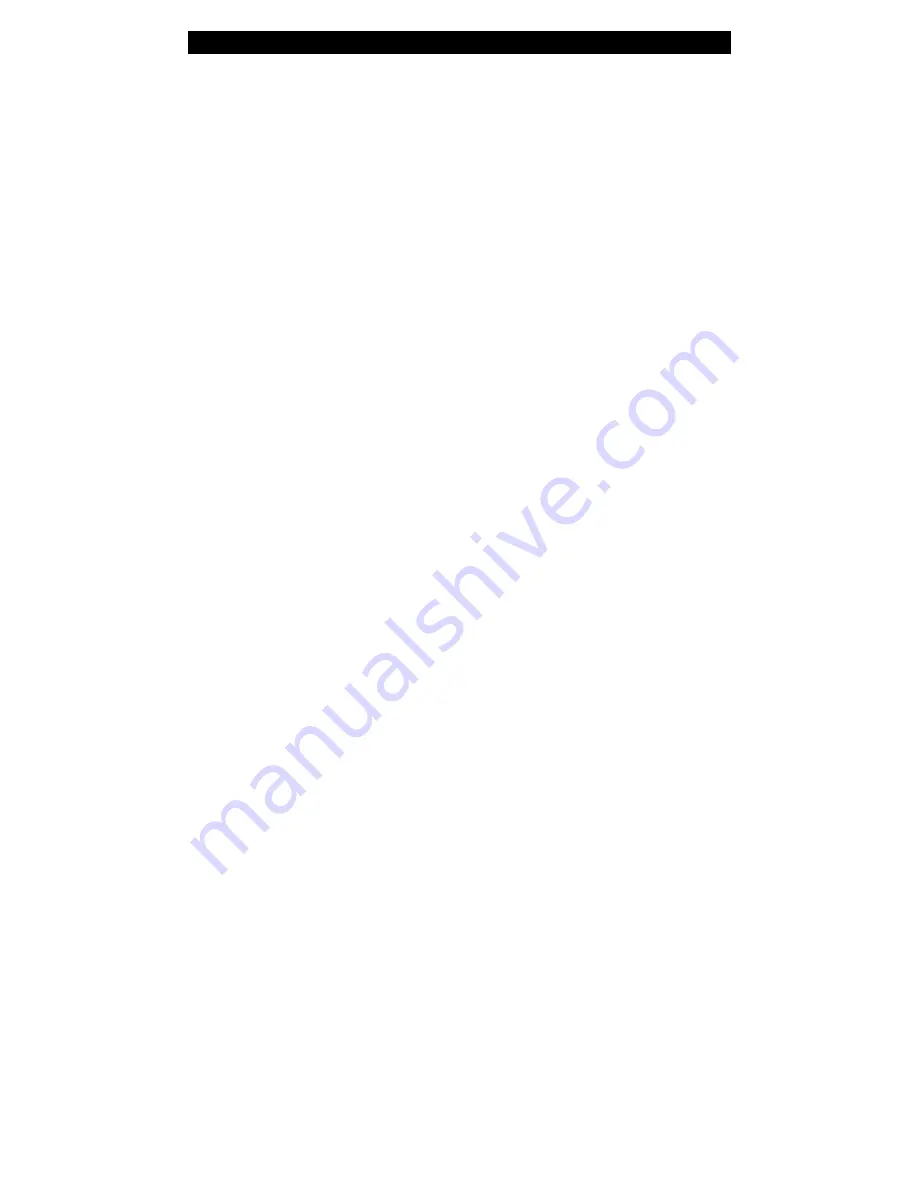
Drilling and driving-in operations for self-
drilling anchors.
When self-drilling anchors (Fig 4) are used,
the anchors can be driven in. In this case,
use the optional accessories for self-drilling
anchors such as the anchor adaptor.
1/ When an impact anchor adaptor is
used
,(1) attach the turning handle to the
anchor adaptor and create a base hole by
applying drill impact to the hole position while
manually turning the handle. (Fig 5). In this
case the plug is not attached to the anchor.
(2) When a predetermined depth has been
attained, pull out the anchor tentatively. (Fig
6). (3) By employing a syringe, blow out the
chips and dust.
(4) Attach the plug to the anchor tip and drive
in the anchor again with the electric hammer
drill.
(5)After driving in the anchor, use the drift
key to separate the anchor. (see Fig 7)
(6)By employing a manual hammer or pliers,
snap off the tapered portion of the anchor.
(see Fig 8)
Caution.
Since the snapped off tapered portion will fly
about, pay attention to the snapping direction
As this may cause injury.
2/ When a rotation and impact anchor
adapter is used,
(1) attach a self-drilling anchor to the anchor
adaptor.
(2) Turn on the switch and drill a base hole
with the self-drilling anchor.
At the start of the hole-drilling slightly tilt the
drill to determine the hole position.
(3) After drilling clear out dust from the hole
with the
syringe, attach the plug to the
anchor tip and drive in the anchor with a
hand hammer.
(4) For further operations, follow procedures
(5) and (6) described above. When an impact
anchor adaptor is used.
When a taper shank adaptor is used
(1)Attach a drill bit with tapered shank to the
taper shank adaptor.
(2) Turn on the switch, and drill a hole until it
reaches the hole depth indicating groove.
(see Fig 9)
(3) After clearing out the dust and particles
with the syringe, attach a plug to the anchor
tip and drive in the anchor with a manual
hammer or pliers.
How to handle a core bit
When a core bit is used, large caliber holes
and blind holes can be drilled. In this case,
use optional accessories for core bits (such
as a center pin and core bit shank) for more
rational operation.
1. Mounting.
Caution
Prior to mounting a core bit, always
disconnect the plug from the power supply
receptacle.
(1) Mount the core bit on the core bit shank
(Fig 10) make sure you oil the screw portion
of the core bit shank for easy dismount.
(2) Mount the core bit shank on the drill main
body in the same manner as in mounting the
drill bit and the bull point. (Fig 11)
(3) Insert the center pin into the guide plate
until it reaches the extremity.
(4) Fit in the guide plate by aligning its
concaved position with the core bit tip when
the position of the concave is shifted by
turning the guide plate right or left, the guide
plate never slips off even when the drill is
used in a downward direction. (Fig 12)
2. Drilling holes.
(1)
Insert the plug into a power supply
receptacle.
(2) A spring is built in the center pin. By
straight and gentle pressing to the wall or
floor surface, the entire surface of the core bit
tip attains contact to start the hole drilling job.
(3) When the hole depth reaches
approximately 5mm, the hole position can be
determined. Then remove the center pin and
guide plate from the core bit and continue the
drilling job.
Caution
When removing the center pin and guide
plate, always disconnect the plug from the
power supply receptacle.
15
ASSEMBLY & OPERATION