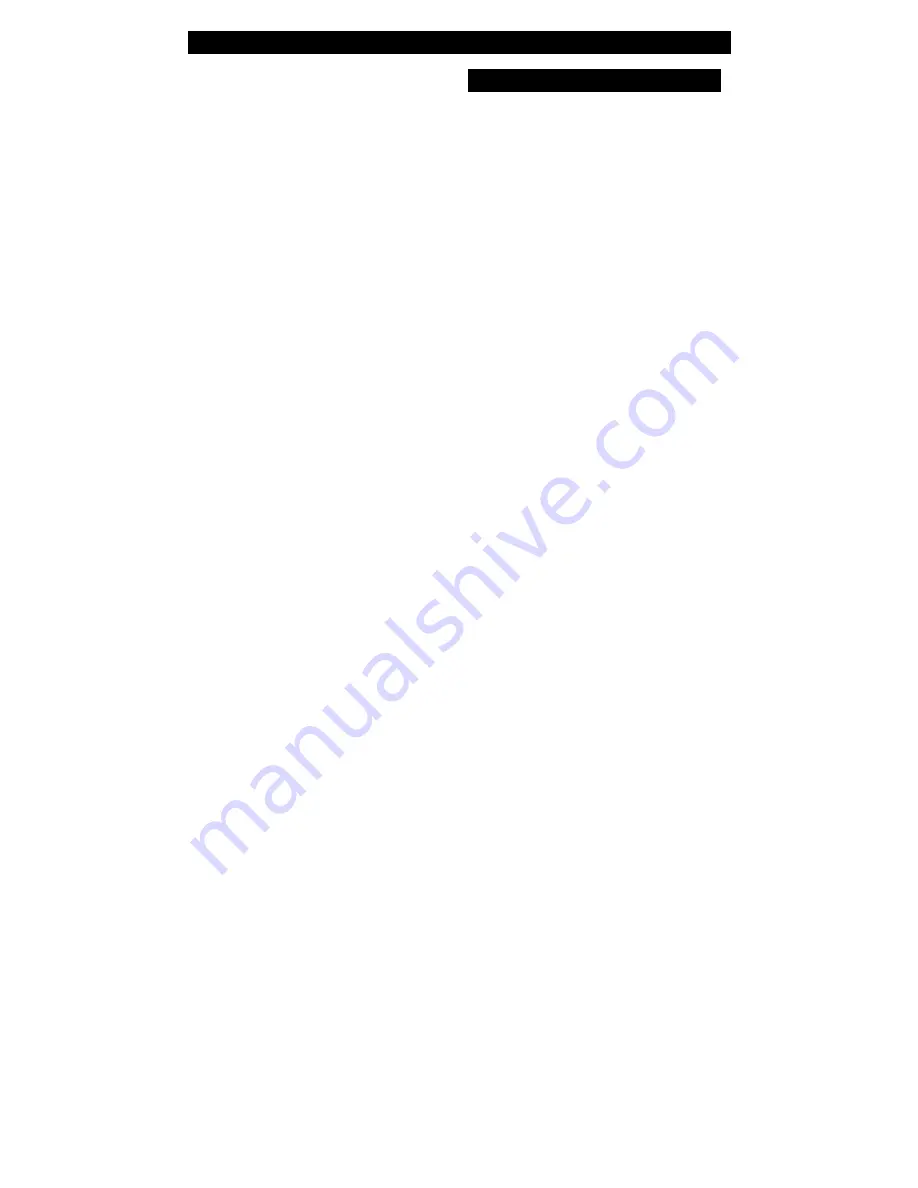
How to dismount the core bit
(1) By holding the drill (with the core bit
inserted) in an upward position, drive the drill
to repeat impact operation two or three times,
whereby the screw is loosened and the drill
becomes ready for disassembly. (2)
Remove the core bit shank from the drill, hold
the core bit with one hand and strongly strike
the head of the hexagonal portion of the core
bit shank with a hand hammer two or three
times, whereby the round head screw is
loosened and the drill is ready for
disassembly.
Oil feeding
Caution.
Prior to oil feeding, always disconnect the
plug from the power supply receptacle.
Since an oil chamber is built in this electric
hammer drill, it can be used for
approximately 20 days without supplying
lubrication oil, assuming that the drill is used
continuously 3 –4 hours daily.
Feed oil into the oil tank as described below
before using the hammer drill. (see Fig 15
and 16)
(1) When the drill is held upright look through
the oil gauge window to see if oil is visible, if
no oil shows oil must be installed before
operating. If drill is used without oil this could
seriously damaged the drill and forfeit any
warranty given
(2) Before feeding oil, use the provided
wrench to remove the oil gauge. Be careful
not to lose the rubber packing attached below
the oil gauge.
(3) Check the oil level once daily, confirming
that oil is filled.
(4) After feeding oil, securely clamp the oil
gauge.
Note
: Oil for the electric hammer drill is sold
separately, use Shell oil (ROTELLA 40)
engine oil or equivalent, this is sold at most
shop or filling stations anywhere.
Maintenance and inspection
1.
Inspecting the tool
When using dull tool bits this can cause
motor malfunction and degraded efficiency.
Always replace dull bits with new ones
without delay when abrasion is noted.
2.
Inspecting the mounting screws
Regularly inspect all mounting screws and
ensure that they are properly tightened.
Should any of the screws be loose, retighten
them immediately. Failure to do so could
result in serious injury.
3.
Maintenance of the motor.
The motor unit winding is the very “heart” of
the power tool. Exercise due care to ensure
the winding does not become damaged
and/or wet with oil or water.
4.
Inspecting the carbon brushes (Fig 17)
The motor employs carbon brushes which
are consumable parts. Since an excessively
worn carbon brush could result in motor
trouble, replace the carbon brush with a new
one which has the same carbon brush no.
shown in the figure when it becomes worn to
or near the “wear limit” in addition always
keep carbon brushes clean and ensure that
they slide freely within the brush holders.
Replacement steps.
The carbon brush can be removed by
removing the tail cover and brush cap in that
order at the interior.
5.
Inspection of the dust cover.
The function of the dust cover is to protect
the inside mechanism.
When the interior of the dust cover is worn,
replace with new dust cover. To remove the
dust cover pull it out.
INSTALLING BITS
Never hold the chuck body with one hand
and use the drill power to rotate the drill
body to loosen or tighten bits. You may
severely injure your hand.
ASSEMBLY & OPERATION
MAINTENANCE
16