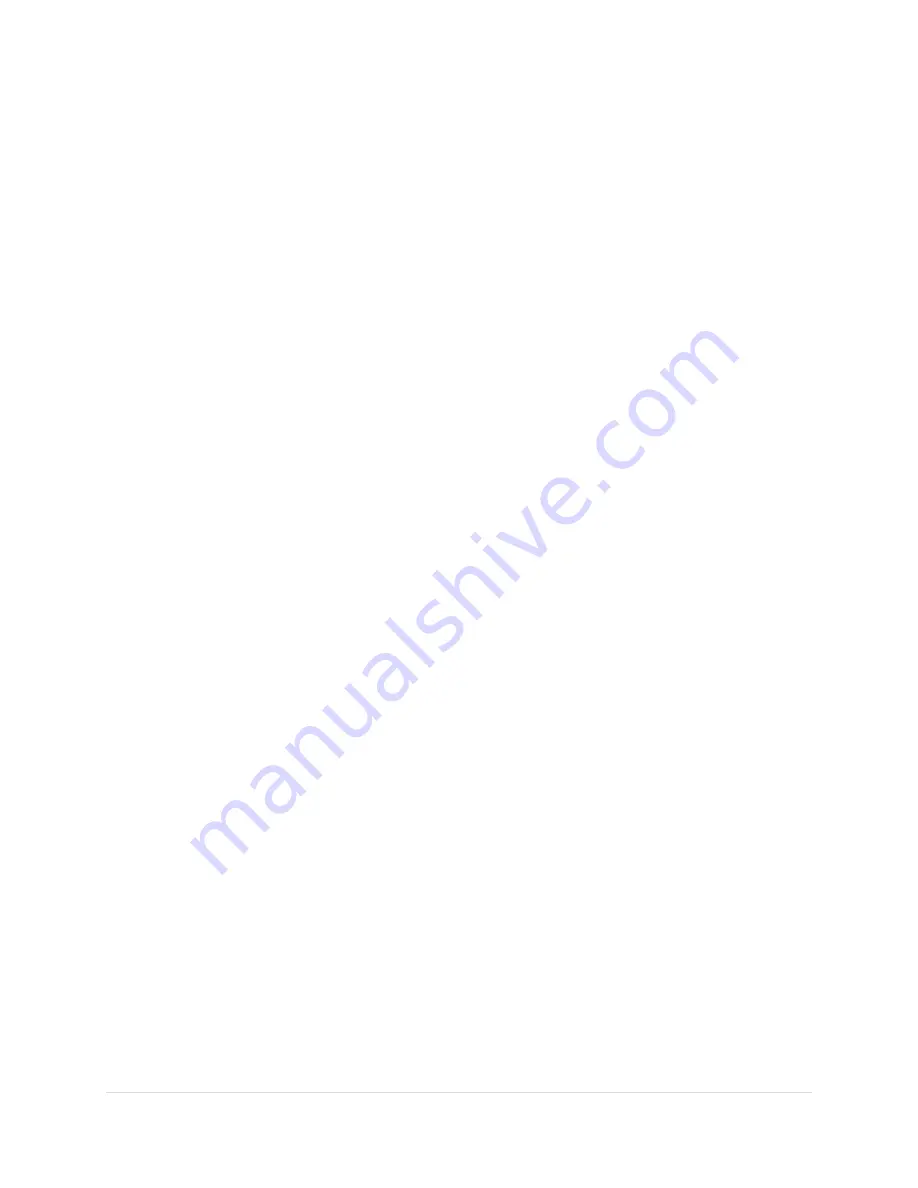
TG110DL User’s Manual
21 |
P a g e
NDT Systems, Inc.
5542
Buckingham Drive
,
Huntington Beach, CA 92649
,
PH: 714-893-2438
12. GAGING PRECAUTIONS
Very Thin Sections: As with any ultrasonic thickness gauge, when the sectional thickness falls below the minimum
operating thickness for the specific probe in use, erroneous readings will result. It is virtually impossible to
precisely specify the minimum thickness which can be gauged with a given probe/TG110DL combination because
the actual minimum thickness depends upon the particular application (material type, contour, surface conditions,
temperature, etc.). Therefore, the minimum thickness limit should be closely approximated by experimentation on
samples of the actual material/product.
One erroneous effect, called "doubling", sometimes occurs when gaging thicknesses fall below the minimum limit.
Another effect, known as "pulse-envelope cycle-jumping," produces a reading somewhat larger than the actual
thickness. It is advisable to double check critical thinner sections by using NDT Systems' NovaScope or an ultrasonic
flaw detector such the Avenger EZ or Raptor.
Pitting Corrosion: Pitted areas on the opposite metal surface can cause unexpected erratic changes in thickness
readout or, in extreme cases, a lack of thickness readout. Very small (especially sharply pointed) pits may even go
undetected (especially isolated single pits). When pitting is either detected or suspected, the area should be very
carefully scanned while changing the orientation of the probe's cross-talk barrier to enhance delectability of the
thinnest pitted spot (s). When positive results cannot be obtained, particularly on critical structures, use NDT
Systems' NovaScope or an ultrasonic flaw detector such the Avenger EZ or Raptor as a supplementary test method.
Material Misidentification: Always verify the type and anticipated thickness of material to be gauged. Erroneous
thickness readouts will result if an instrument is calibrated to a material and thickness other than the test material.
Worn or Malfunctioning Probes: Immediately replace any probe that is malfunctioning or showing excessive or
uneven wear.
Use of the ZERO Command: Zero the probe only on the metal Auto-Zero Reference Disc, located on the front of the
gauge. The instrument will lose calibration if ZERO is depressed while the probe is coupled to any other material.
Abnormal or Unusual Thickness Readings: The operator should always qualify abnormal/questionable thickness
indications. While such indications may be caused by corrosion/erosion, the use of wrong material thickness.
internal flaws, certain other materials, or gauge factors (as discussed).
Material Stacks: It is not possible to gauge the stack thickness of uncoupled material sheets piled upon one
another because ultrasound reflects totally from the bottom surface of the outer sheet.