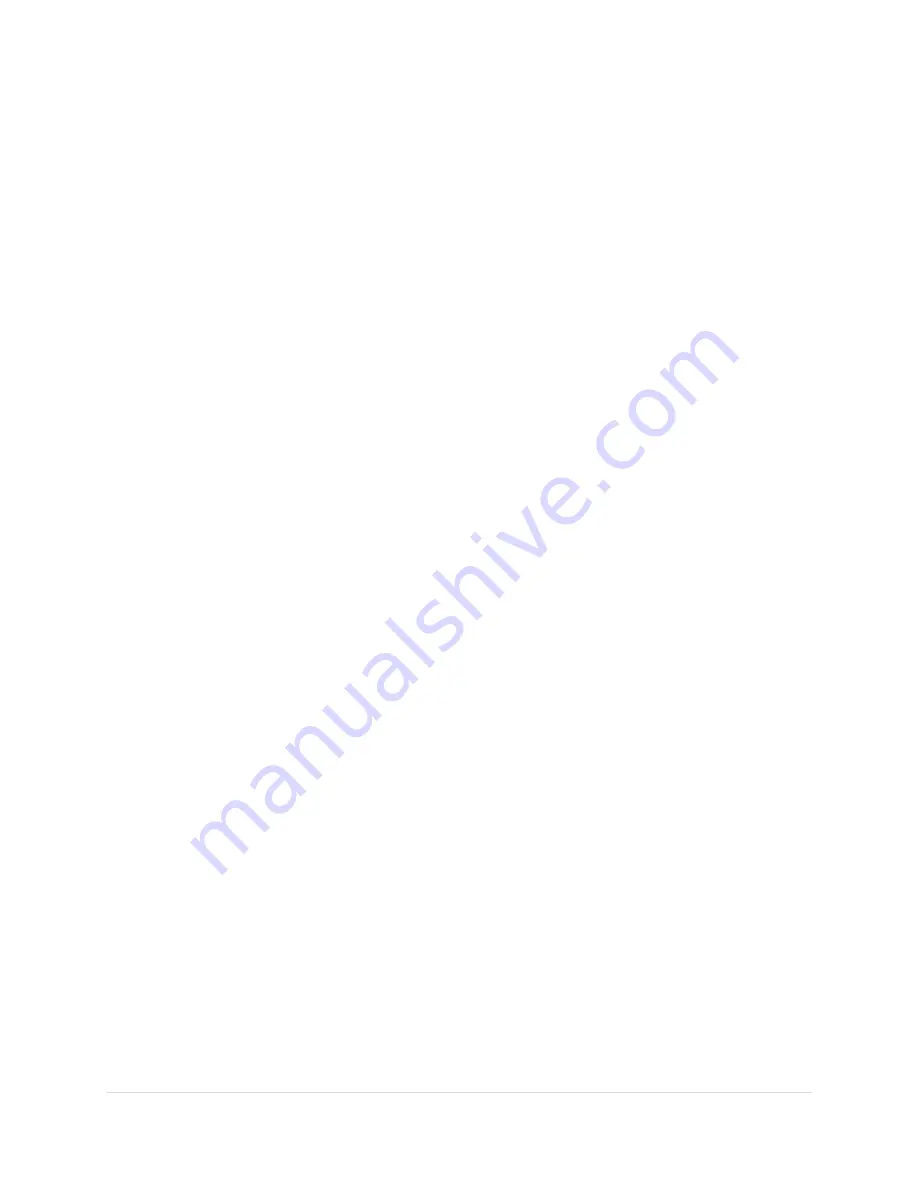
TG110DL User’s Manual
20 |
P a g e
NDT Systems, Inc.
5542
Buckingham Drive
,
Huntington Beach, CA 92649
,
PH: 714-893-2438
7.Compound Contours: For gaging elbows on cylinders, (also see Paragraph 5), rock the probe for a minimum
reading in both the circumferential and longitudinal directions and then use the smaller of the two minimum
readings. On spherical sections, rock the probe for a minimum reading in one direction and, again. or another
minimum reading with the cross-talk barrier perpendicular to the first. Use the smaller of the two minimum
readings. Compound contours are difficult to gauge, so if successful results cannot be obtained, try using an
ultrasonic flaw detector such as the NDT Systems Raptor or a thickness gauge
with ‘A’ Trace capability such as NDT
Systems' TG410.
8. Non-Parallel Surfaces: The surfaces on either side of a section must be relatively parallel or concentric in order
to obtain a satisfactory ultrasonic echo for a thickness reading. Non-parallel or tapered surfaces will produce less
accuracy or no reading at all.
9.Material Temperature Effects: Both the dimensions and the ultrasonic velocity of a material change with
temperature, which, in turn affect calibration. This undesirable effect holds true for the material being gauged as
well as for the probe. Although it is always good practice to re-calibrate when a noticeable change in ambient
temperature occurs, the effect can normally be ignored for modest changes in ambient temperature.
The situation becomes more complex when the material temperature is considerably different than ambient. One
solution is to calibrate on a reference sample at the same temperature as the material. Another solution is to
calibrate on a reference sample at ambient temperature and then add an experimentally derived correction factor
for the temperature of the material.
The gaging of hot steel products is an application where high temperatures will produce significant thickness
readout errors (gauge typically reads thicker than actual), unless some temperature correction or compensation
technique is used.
10.Excessively Attenuative Materials: Some materials (fibrous, porous, large-grained, etc.) may absorb or scatter so
much ultrasound that either a reading cannot be obtained or some abnormal reading (usually abnormally thin)
occurs. In such cases, try a Hi-Power Probe. If gaging is still unsuccessful, use an ultrasonic flaw detector such as
NDT Systems' Avenger EZ or Raptor.
11.Grain Directionality Effects: In many wrought and cast metals, the micro structural properties are directional.
This means the ultrasonic velocity (and calibration) may differ, depending upon the beam direction with respect to
the grain direction. For improved accuracy, always calibrate and subsequently gauge in the same material grain
direction
.