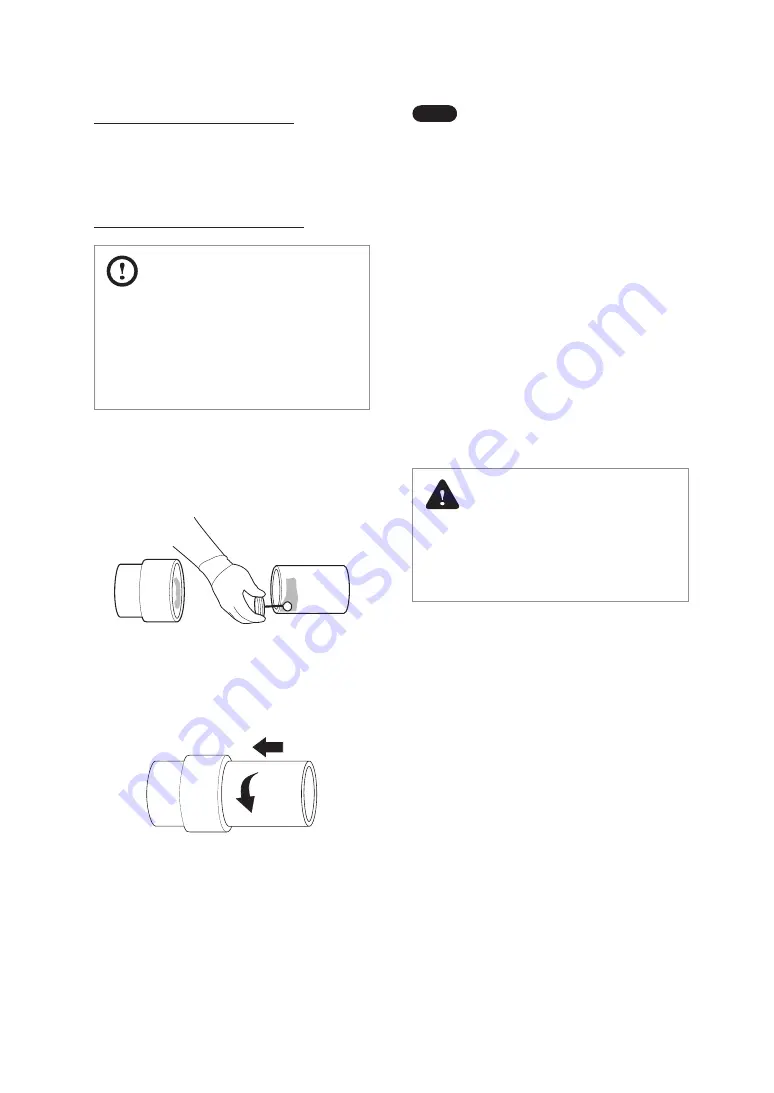
85
Installing a Common Vent System
Note
●
Use approved solvent type cement
for the proper vent materials.
●
Use solvent type cement only.
●
Check the date of manufacture
before using the cement. Ensure that
cement was not manufactured more
than 2 years prior to using it.
●
Ensure that the inside of the pipe
fitting and the outside of the pipe,
where cement will be applied, is
clean.
●
Apply an even layer of cement over
all mating surfaces.
●
Use solvent cement in room
temperatures higher than 32
℉
(0
℃
).
●
Use primer when temperatures are
lower than 32°F (0°C).
●
Installing vent pipe with cement
in cold ambient temperatures can
result in longer cure times.
DANGER
Be careful not to apply force or impact to pipes
after making connections. An impact may break
the bond and harmful gas might leak inside the
room.
Vent Pipe Pitch and Supports
For horizontal runs, slope the horizontal section
upward toward the vent termination at a rate of
1
/
4
”
per foot (2% slope).
Connecting Pipes with Cement
CAUTION
The vapors from primers and solvent cements
can cause nausea and can be dangerous to
your health. Ensure that the work area is well
ventilated, or wear an approved organic vapour
respirator when working with primers and
solvent cements.
To connect the vent pipes using cement:
1. Spread an even layer of solvent cement on the
inside of the pipe fitting and the outside of the
pipe.
2. Align the pipe with the pipe fitting and twist
the pipe a quarter turn as you insert it into the
fitting. Twisting the pipe spreads the solvent
cement evenly to ensure a solid joint.
3. Hold the pipe and pipe fitting together for
about 15 seconds until the cement sets.
Summary of Contents for NCB-190/060H
Page 141: ...141 Appendixes 12 6 4 Fan Gas Assembly 10 9 12 8 7 3 1 2 4 5 6 13 11 11 14 15...
Page 143: ...Memo...
Page 144: ......