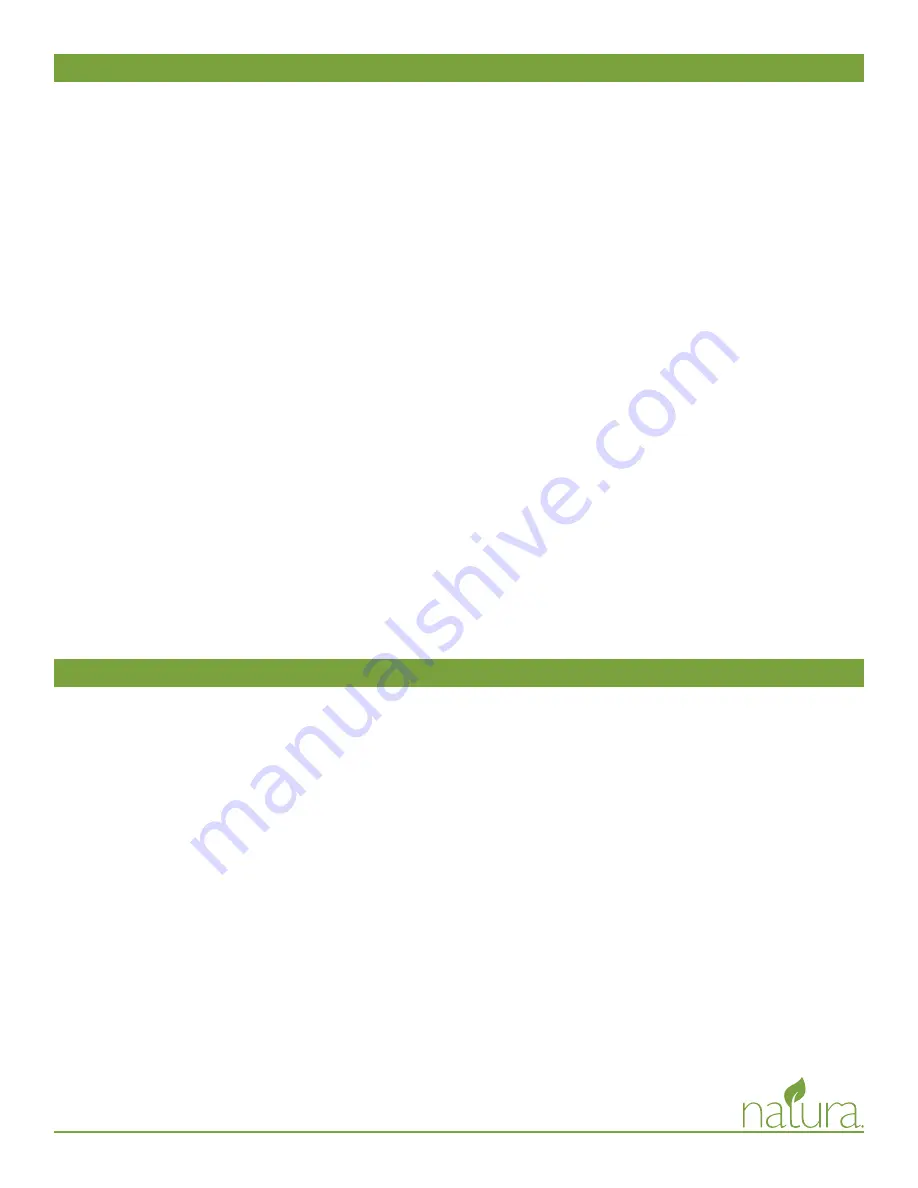
3
Installation and Maintenance Manual
o
Use only original and new parts to guarantee the reliability, optimization, and
performance of the Natura water machine.
o
Always wear proper protection when performing any type of service or
maintenance.
o
Do not expose the CO
2
Cylinder to direct sun light, to sources of heat, or to
temperature below 32° F (0° C).
o
Always keep the CO
2
Cylinder in a vertical position while in use and secure
properly with a chain or strap.
o
To properly carbonate the water, make sure that CO
2
Cylinder valve is
completely
open.
o
Use only food grade CO
2
(UN1013) gas.
o
Adjust the CO
2
Pressure Regulator to a target of 60 PSI with a 65 PSI maximum.
o
When cleaning the unit, do not use corrosive, acidic products, or metal brushes.
o
Do not wash the unit using high-pressure water.
o
Connect to a water supply with a pressure of 45 to 120 PSI.
.
o
The unit must be connected to a 115 VAC, 15 amp GFCI power supply. Operating
voltage is listed on the equipment data label.
o
The unit must be protected by a properly installed circuit breaker. Verify that
the electrical current is correct for the power of the unit, which is listed on
the machine data label.
o
To avoid electrical shock always unplug the unit from the electrical outlet before
servicing.
o
All packaging materials (plastic bags, foam, etc.) should never be left within the
reach of small children. These items are potentially hazardous and may cause
severe injury or death.
o CO
2
is a high pressure gas – use caution when moving or making connections.
2. IMPORTANT REQUIREMENTS
:
3. SAFETY WARNINGS: