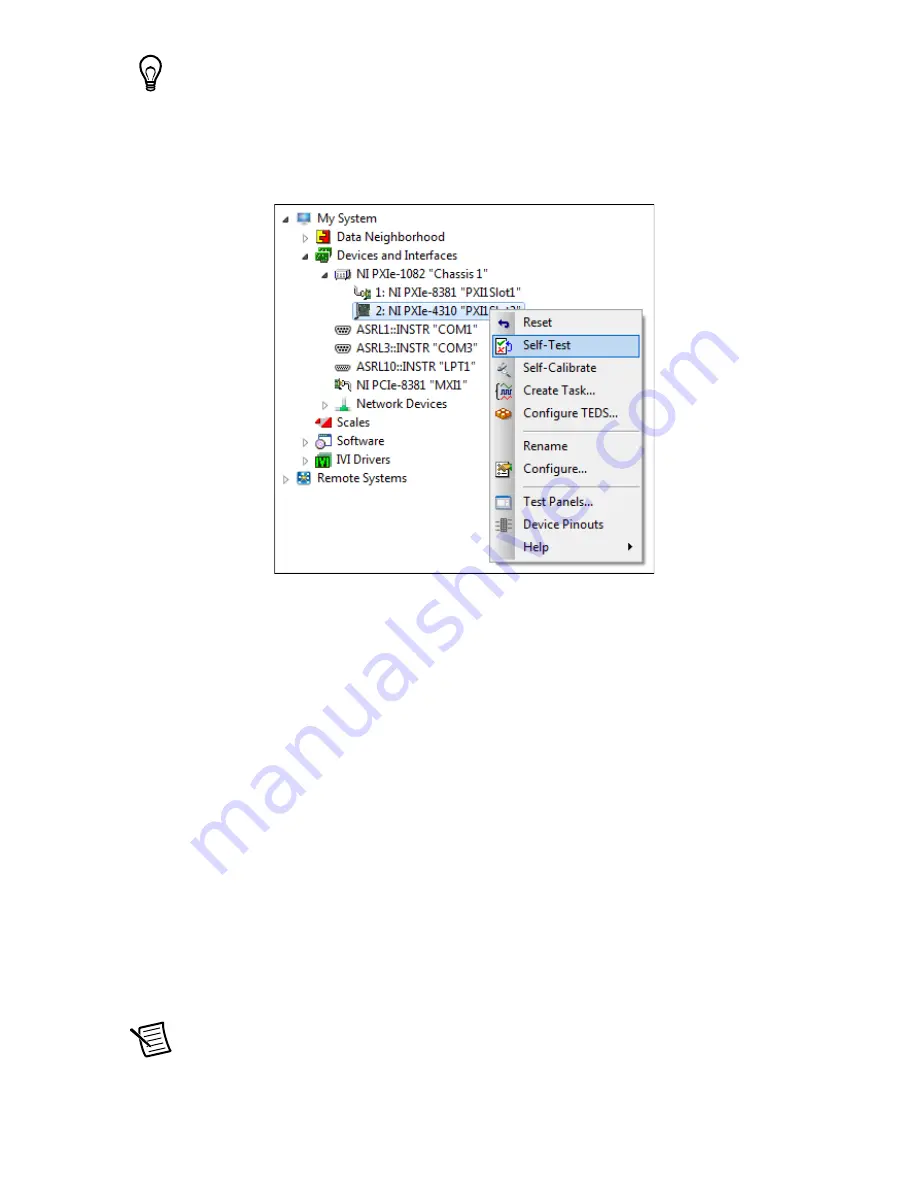
PXIe-4310 and TB-4310 (10V)/TB-4310 (600V)
|
© National Instruments
|
11
Tip
Using an NI-DAQmx simulated device, you can test NI-DAQmx applications
without installing hardware. Refer to the
Create a Simulated Device
section for
instructions for creating NI-DAQmx simulated devices.
4.
Right-click the module name and select
Self-Test
. When the self-test completes, a
verification message appears. If an error occurs, refer to
ni.com/support/daqmx
.
Device Self-Calibration
NI recommends that you self-calibrate your PXIe-4310 module after installation and whenever
the ambient temperature changes. Self-calibration should be performed after the device has
warmed up for the recommended time period. Refer to the device specifications to find your
device warm-up time. This function measures the onboard reference voltage of the device and
adjusts the self-calibration constants to account for any errors caused by short-term fluctuations
in the environment.
You can initiate self-calibration using Measurement & Automation Explorer (MAX), by
completing the following steps:
1.
Launch MAX.
2.
Select
My System»Devices and Interfaces»
your device
.
3.
Initiate self-calibration using one of the following methods:
•
Select the PXIe-4310 in the MAX configuration tree and click the
Self-Calibrate
button located on the MAX toolbar.
•
Right-click the name of the device in the MAX configuration tree and select
Self-Calibrate
from the drop-down menu.
Note
You can also programmatically self-calibrate your device with NI-DAQmx,
as described in
Device Calibration
in the
NI-DAQmx Help
or the
LabVIEW Help
.