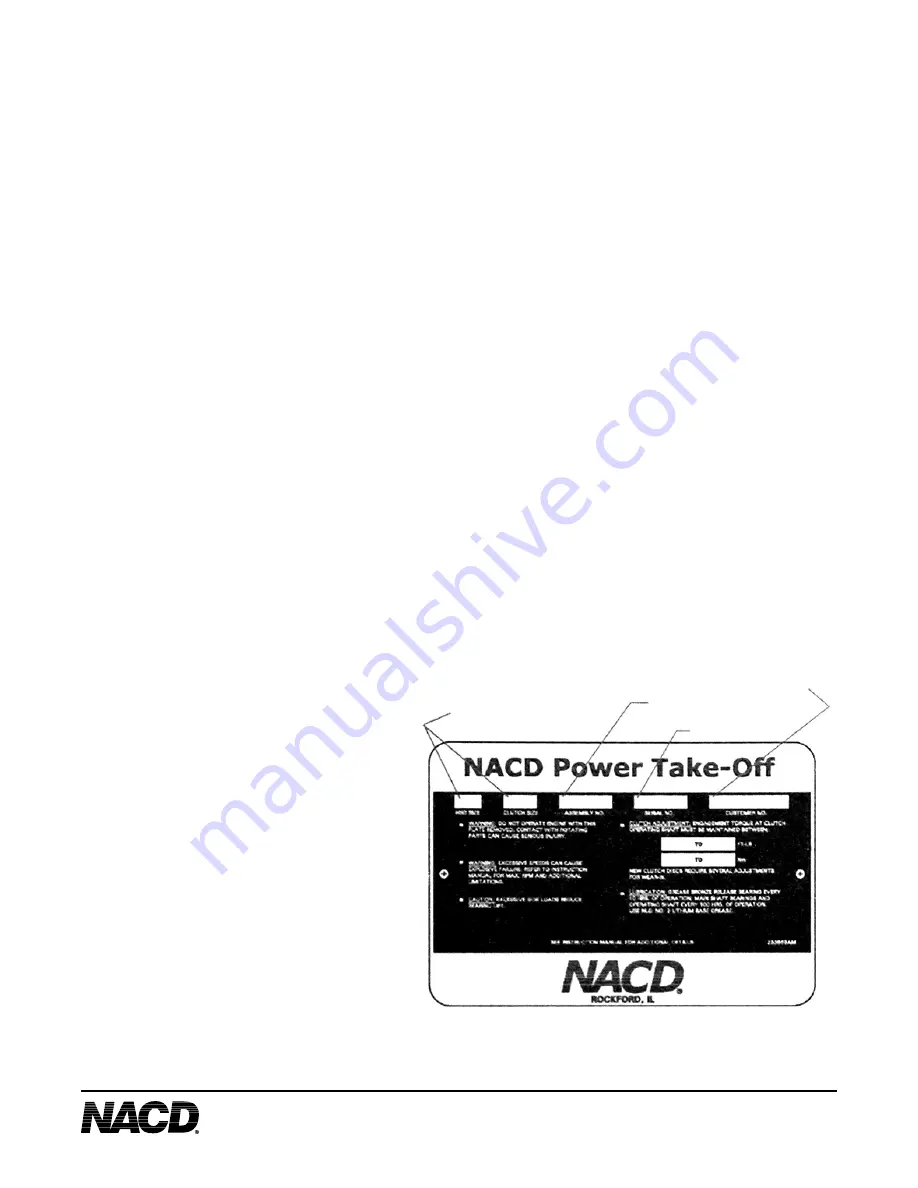
North American Clutch & Driveline
Rockford, Illinois
Phone: (800) 383-9204
(815) 282-7960
Fax (815) 282-9160
www.naclutch.com
99
WARRANTy
Equipment for which this manual was written has a limited warranty. For details of the warranty,
refer to the warranty statement at the end of this manual.
DeSCRIPTION AND SPeCIfICATIONS
geNeRAl INfORMATION
The SP214AM and SP314AM Series NACD Power Take-Offs are engine-mounted power take-
offs that use cast iron one-piece housings and contain an integral clutch 14 inches in diameter.
The engine drives the clutch through a drive ring that is bolted to the engine flywheel and
connected to the clutch through internal teeth that mesh with external teeth on the clutch
friction plate(s). Clutch engagement and disengagement for most units is accomplished by use
of the external hand lever assembly. Some units may use other actuation methods.
Main bearings are lubricated and cooled with grease , depending upon the design specifications.
Most units use pilot bearings that are pre-lubricated and sealed for life.
fINDINg THe NACD POWeR
TAKe-Off MODel AND
SeRIAl NUMBeR
The nameplate identifies the
housing size, clutch size,
assembly number and the
serial number of the unit. The
assembly and serial numbers are
necessary to identify the correct
parts for your Power Take-Off.
SAE Housing Size
& Clutch Size
NACD Part #
Customer Part #
Serial #