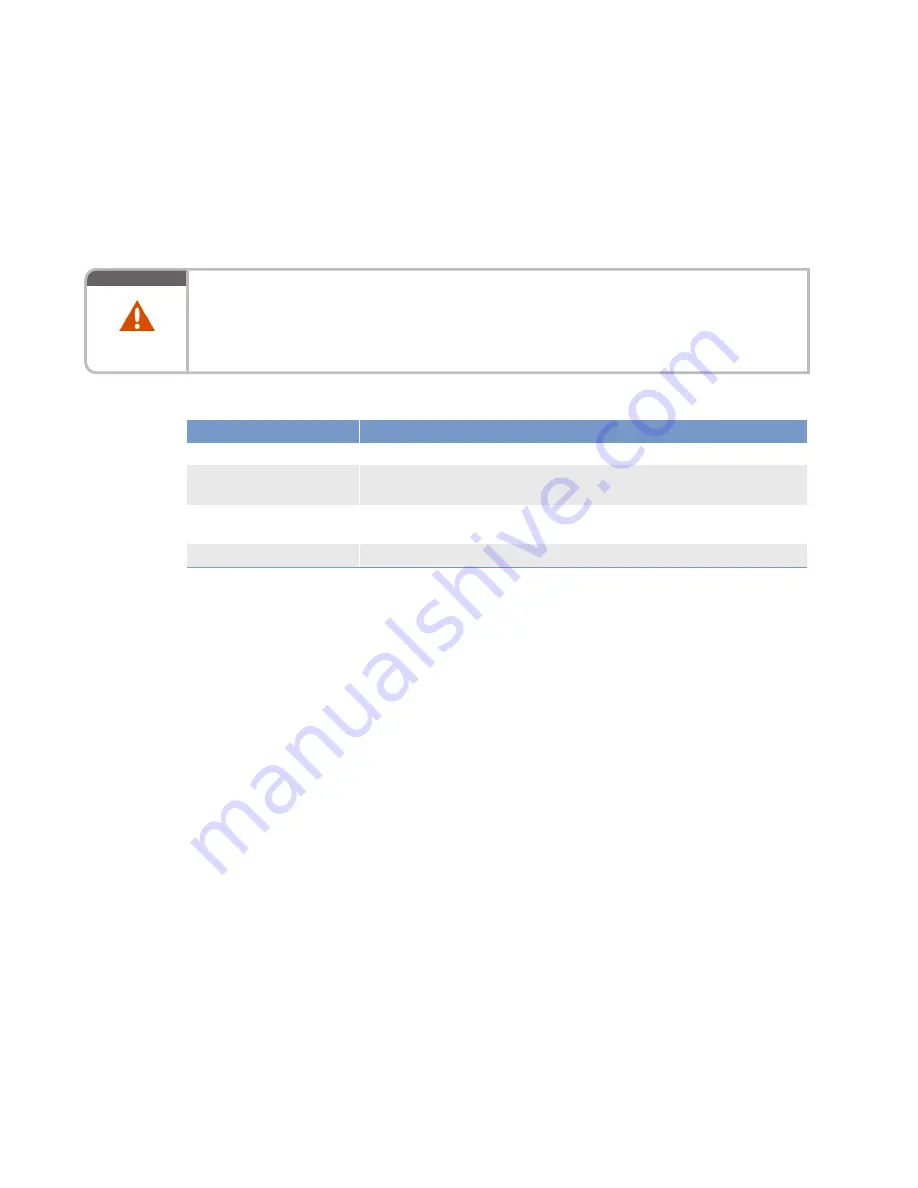
5.2 Putting the engine into operation after scheduled out-of-
service-period
Preconditions
☑
Engine is stopped and starting disabled.
WARNING
In case of out-of-service periods of more than one week: Possible corrosion of components carrying air
or exhaust gas due to weather conditions, e.g. rain or snow.
Risk of injury by flying debris when putting the engine into operation!
• Check the components carrying air and exhaust for corrosion.
• Do not put the engine in operation if corrosion was detected.
Putting into operation
Item
Measure
Engine oil system
Check engine oil level (→ Page 120).
Coolant circuit
Check engine coolant level (→ Page 131);
Check charge-air coolant level (→ Page 141).
Coolant circuit
Heat coolant with coolant preheater (if available; see manufacturer's docu-
mentation).
Engine control system
Put into operation (see manufacturer's documentation).
38 | Operation | MS15043/00E 2016-04
TIM-ID: 0000002683 - 007
Summary of Contents for 20V4000C55
Page 1: ...Operating Instructions Diesel engine 20V4000C55 20V4000C65 Application group 5B MS15043 00E...
Page 168: ...168 MS15043 00E 2016 04...
Page 170: ...170 Manufacturer s Documentation MS15043 00E 2016 04...
Page 182: ...182 Manufacturer s Documentation MS15043 00E 2016 04 TIM ID 0000083486 002...
Page 184: ...184 Manufacturer s Documentation MS15043 00E 2016 04 TIM ID 0000098598 001...
Page 185: ...MS15043 00E 2016 04 Manufacturer s Documentation 185 TIM ID 0000098598 001...
Page 186: ...186 Manufacturer s Documentation MS15043 00E 2016 04 TIM ID 0000098598 001...
Page 187: ...MS15043 00E 2016 04 Manufacturer s Documentation 187 TIM ID 0000098598 001...
Page 188: ...188 Manufacturer s Documentation MS15043 00E 2016 04 TIM ID 0000098598 001...
Page 189: ...MS15043 00E 2016 04 Manufacturer s Documentation 189 TIM ID 0000098598 001...
Page 190: ...190 Manufacturer s Documentation MS15043 00E 2016 04 TIM ID 0000098598 001...
Page 191: ...MS15043 00E 2016 04 Manufacturer s Documentation 191 TIM ID 0000098598 001...
Page 192: ...192 Manufacturer s Documentation MS15043 00E 2016 04 TIM ID 0000098598 001...
Page 193: ...MS15043 00E 2016 04 Manufacturer s Documentation 193 TIM ID 0000098598 001...
Page 194: ...194 Manufacturer s Documentation MS15043 00E 2016 04 TIM ID 0000098598 001...