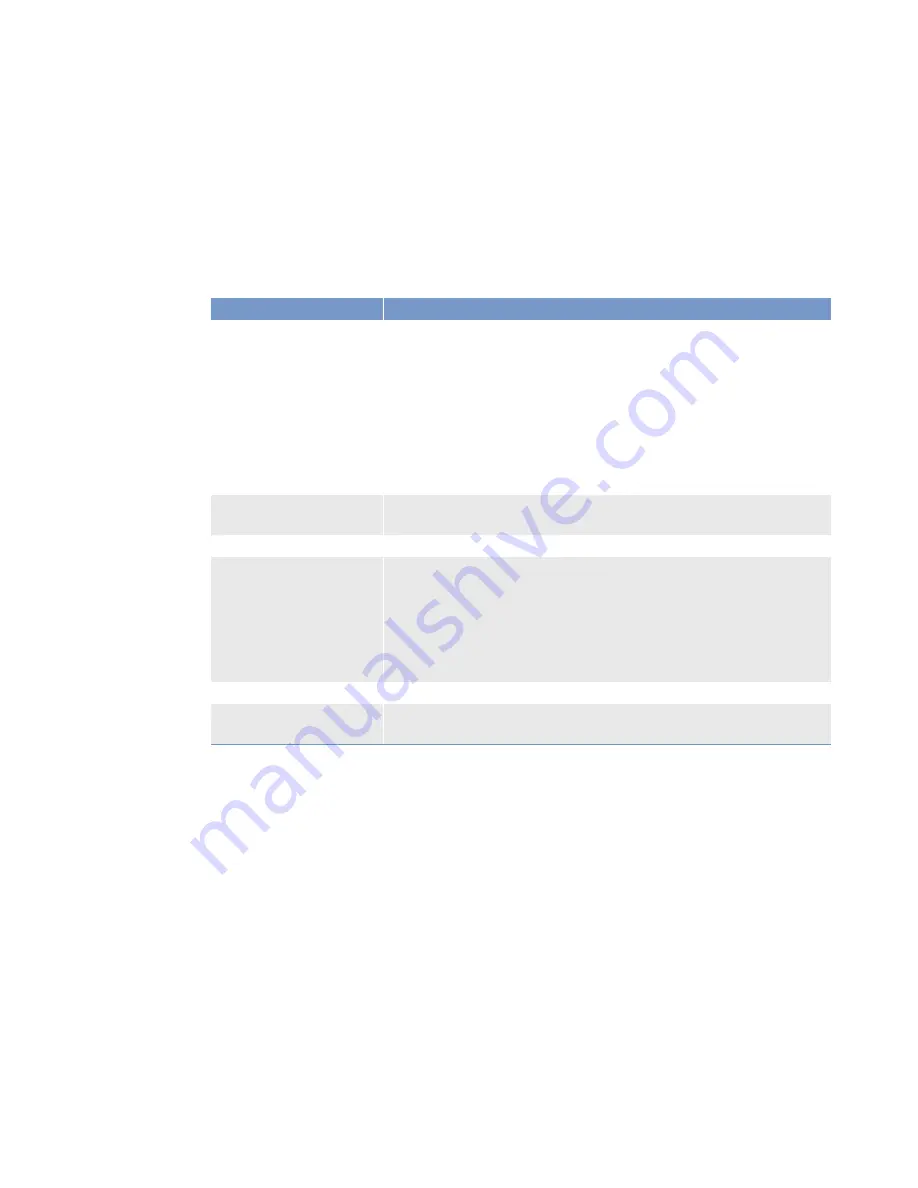
3.11 After stopping the engine – Putting the engine out of
operation
Preconditions
☑
MTU Fluids and Lubricants Specifications (A001061/..) are available.
After stopping the engine
Item
Action
Coolant circuit
Drain engine coolant (→ Page 179)
Drain mixture coolant (→ Page 184) if:
•
freezing temperatures are expected and the engine is to remain out of
service for an extended period, but coolant has no antifreeze additive;
•
the engine room is not heated;
•
the engine coolant is not maintained at a suitable temperature;
•
the antifreeze concentration is insufficient for the engine-room tem-
perature;
•
antifreeze concentration is 50 % and engine-room temperature is be-
low -40 °C.
Power supply to engine con-
trol system
Switch off.
Gas supply
Close gas shut-off valve.
Air intake and exhaust sys-
tems
If the engine is to remain out of service for more than 1 week, seal the en-
gine's air and exhaust sides. If the engine is to remain out of service for more
than 1 month, carry out preservation (→ MTU Preservation and Represerva-
tion Specifications A001070/..).
The corrosion-inhibiting effect of the engine coolant may be used as an alter-
native in case of out-of-service periods lasting for more than 1 month, by run-
ning the engine for at least 2 hours at rated power once a month.
Starter battery (batteries)
Charge regularly (trickle charge).
Control-voltage battery (bat-
teries)
If fitted: Charge regularly (trickle charge).
Table 36: After stopping the engine
MS15027/00E 2013-10
| Operation | 47
TIM-ID: 0000043160 - 003