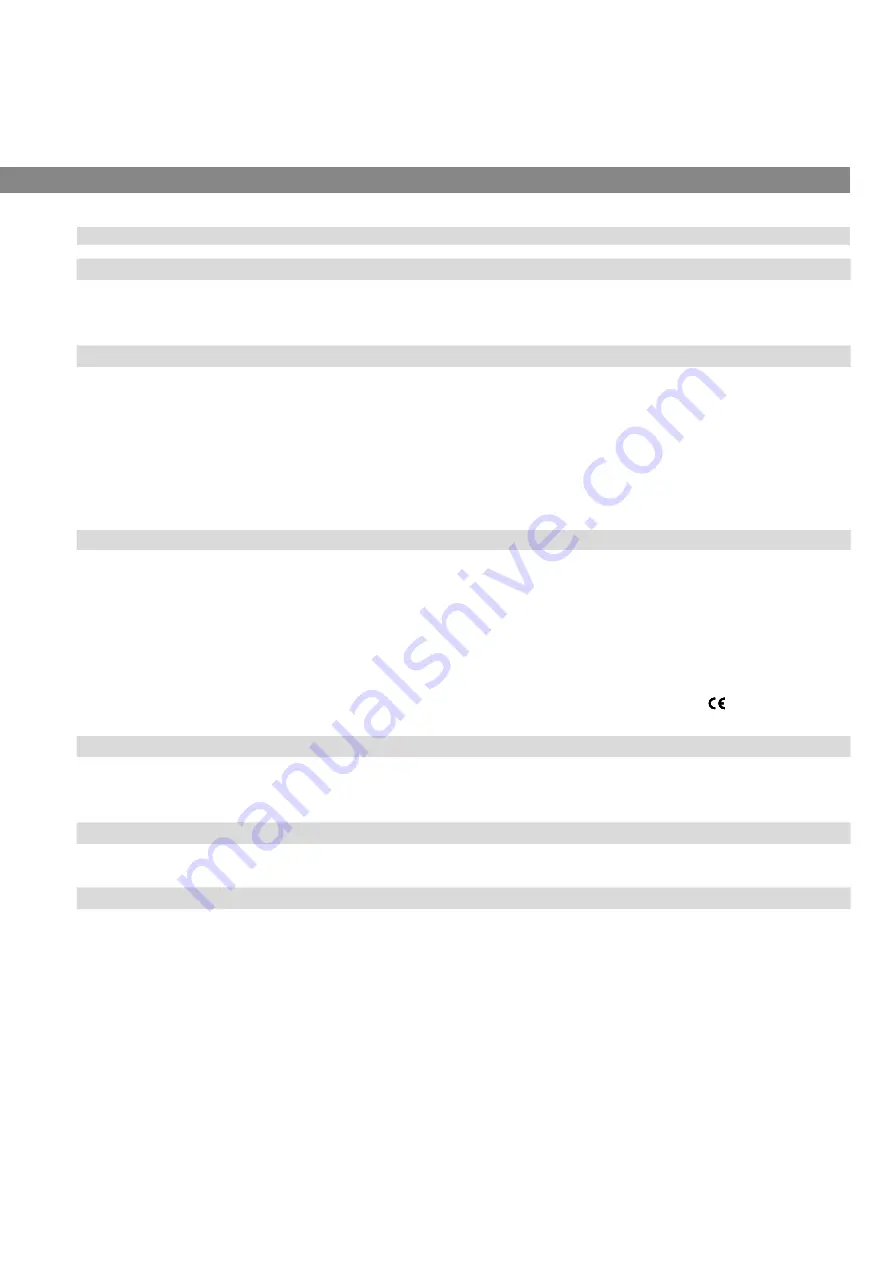
8/
With position magnet # 252 182
9/
The IP rating is not part of the UL approval
10/
Power supply must be able to provide current of 1A for power up process
11. Technical data
Output
Interface
Ethernet POWERLINK
Data protocol
POWERLINK V2 according to IEEE 802.3
Measured value
Position, velocity / option: multi-position measurement (2…4 positions)
Measurement parameters
Resolution
1 μm, 2 μm, 5 μm, 10 μm, 50 μm or 100 μm (selectable)
Cycle time
1.0 ms up to 2400 mm stroke length,
2.0 ms up to 4800 mm stroke length,
4.0 ms up to 5080 mm stroke length
Linearity
8
< ±0.01 % F.S. (minimum ±50 µm)
Repeatability
< ±0.001 % F.S. (minimum ±2.5 µm) typical
Hysteresis
< 4 µm typical
Temperature coefficient
< 15 ppm/K typical
Operating conditions
Operating temperature
−40…+75 °C (−40…+167 °F)
Humidity
90 % rel. humidity, no condensation
Ingress protection
9
IP65 (if mating connectors are correctly fitted)
Shock test
100 g (single shock), IEC standard 60068-2-27
Vibration test
15 g (10…2000 Hz), IEC standard 60068-2-6 (resonance frequencies excluded)
EMC test
Electromagnetic immunity EN 61000-6-2
Electromagnetic emission EN 61000-6-3
The sensor meets the requirements of the EC directives and is marked with
Magnet movement velocity
Any (with magnet slider: max. 10 m/s)
Design / Material
Sensor electronics housing
Aluminum
Sensor profile
Aluminum
Stroke length
25…5080 mm (1…200 in.)
Mechanical mounting
Mounting position
Any
Mounting instruction
Please consult the technical drawings
Electrical connection
Connection type
2 × M12 female connector (4 pin), 1 × M8 male connector (4 pin)
Operating voltage
10
+24 VDC (−15 / +20 %); UL Recognition requires an approved power supply with energy limitation
(UL 61010-1), or Class 2 rating according to the National Electrical Code (USA) / Canadian Electrical Code.
Ripple
≤ 0.28 V
PP
Current consumption
10
110 mA typical
Dielectric strength
500 VDC (DC ground to machine ground)
Polarity protection
Up to −30 VDC
Overvoltage protection
Up to 36 VDC
11.1 Technical data of Temposonics
®
RP
Temposonics
®
R-Series Powerlink V2
Operation Manual
I 47 I