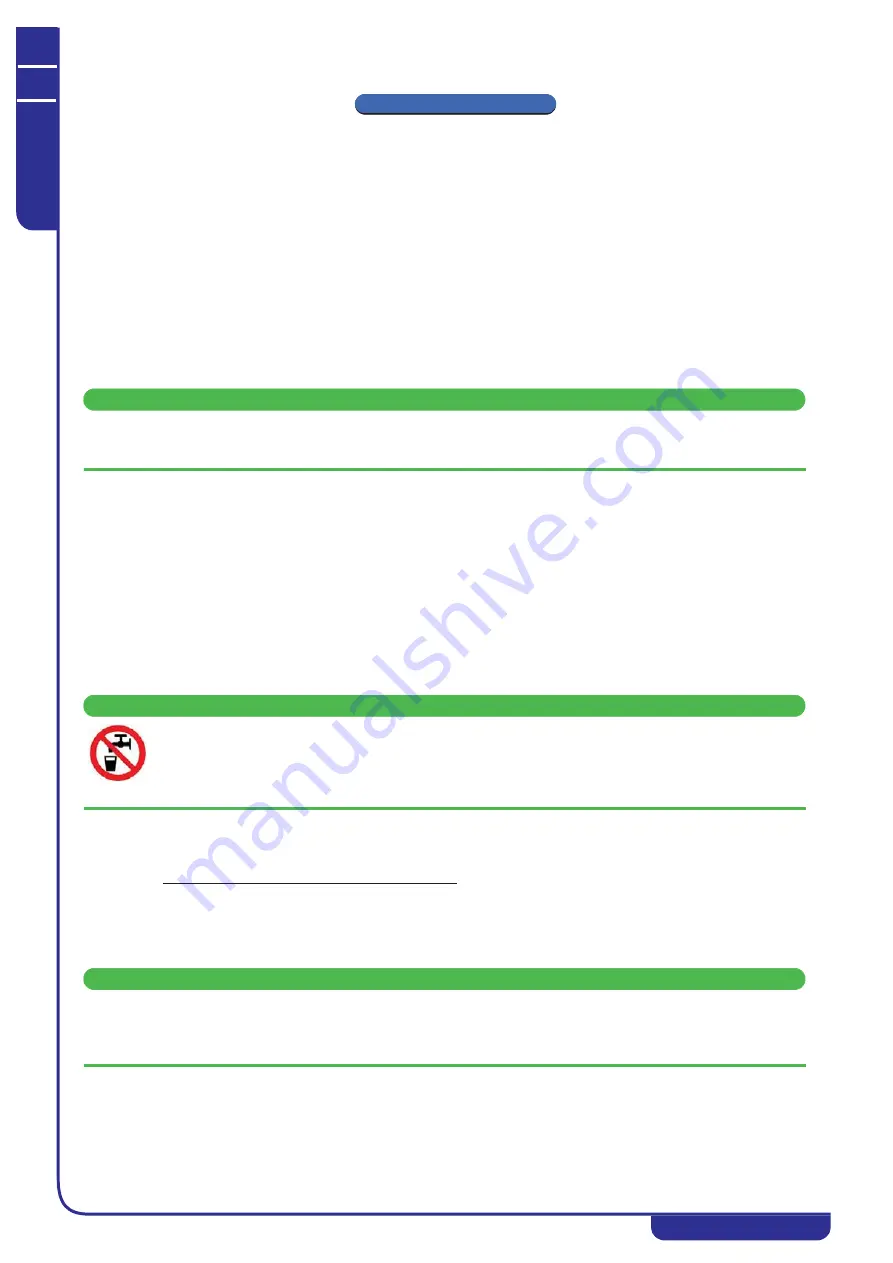
OPERATING AND MAINTENANCE MANUAL
Chapter 2 - Safety
TAEevo Tech MINI 02÷10
5
The data in this manual are not binding and they can be modified by the manufacturer without notice.
Reproduction of this manual is strictly prohibited
EN
ENGLISH
C
HAPTER
2
S
AFETY
This unit is designed to ensure the best guarantees of safety and efficiency in its intended use, on the condition that it is
installed, commissioned, and serviced in compliance with the instructions given in this manual.
The manual must therefore be studied by all those who want to install, use or maintain the unit.
The unit contains electrical components that operate at mains voltage and also moving parts.
All work on the unit must be carried out only after disconnecting the electrical supply. Maintenance operations involving
work inside the unit must be performed by skilled and adequately qualified personnel equipped with suitable protection
means (active and passive, e.g. work gloves) to ensure maximum safety.
Keep unauthorized persons (e.g. children) away from the place of installation of the unit.
2 . 1
G e n e r a l
When handling or maintaining the unit and all auxiliary equipment, personnel must operate with care observing all
instructions concerning health and safety at the installation site.
ATTENTION
Numerous accidents that occur during operation and maintenance of the units are caused by failure to comply with
basic safety rules and precautions.
An accident can often be avoided by recognising a situation that is potentially hazardous.
The user must ensure that all personnel involved in operating and servicing the unit have read and understood all the
warnings, precautions, prohibitions and notes given in this manual and affixed to the unit. Improper operation or maintenance
of the unit and auxiliary equipment can be dangerous and can cause serious or fatal accidents.
We cannot anticipate every possible circumstance which might constitute a potential hazard.
The warnings in this manual are therefore not all-inclusive.
If the user adopts operational procedures or uses tools or working procedures that are not specifically recommended, he must
take care to ensure that the unit and the auxiliary equipment are not damaged or made unsafe and that no risks emerge in
relation to persons or property. Any improper use of the unit will relieve the manufacturer from any liability for possible
personal injury or property damage.
Arbitrary modifications made to the unit will automatically invalidate all forms of guarantee provided by the manufacturer.
ATTENTION
The hot / chilled water produced by units cannot be used for hygiene/sanitary or food applications. If it is
used for the above purposes, the installer must install an intermediate exchanger.
If the intermediate exchanger is not present, the installer must affix a warning notice to the effect “non potable
water”.
2 . 2
L i q u i d s t o b e c o o l e d
The liquids to be cooled must be compatible with the materials used.
These can be water or mixtures of water and glycol, for example. In case of distilled or demineralised water, check the
compatibility with materials.
It is advisable to work with pH between 7 and 8. If using chemical additives consult your supplier for more information
concerning compatibility with materials in contact with the process fluid of the chiller.
The liquids to be cooled must not be flammable.
ATTENTION
If the liquids to be cooled contains dangerous substances (e.g. ethylene glycol) it is very important to collect any liquid
which leaks because it could cause damages to the ambient. Furthermore, when the chiller is no longer used, dangerous
liquids must be disposed of by firms specialised and authorised for treating them.
Summary of Contents for TAEevo Tech MINI
Page 36: ......