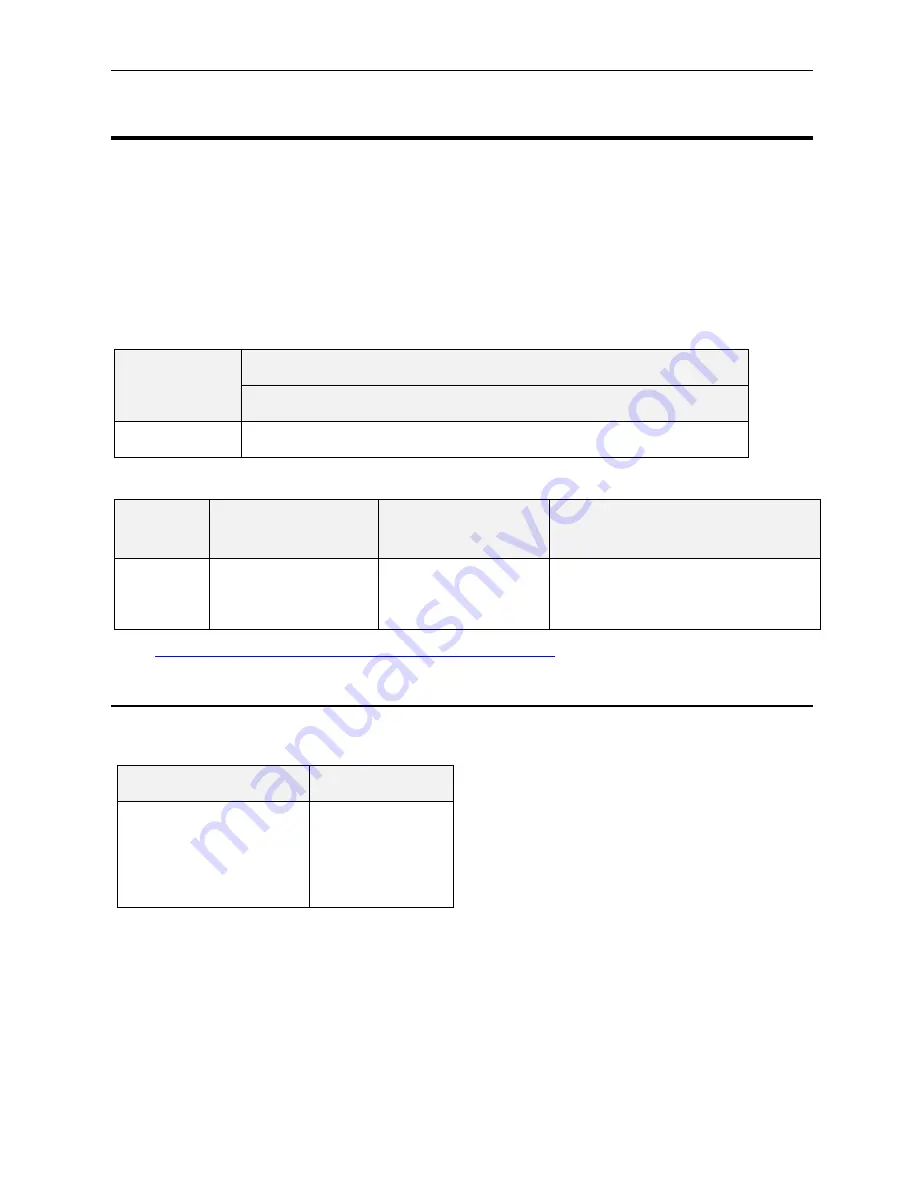
28
Operation
Lambda and Air Fuel Ratio
Lambda gives a measure of the Air to Fuel Ratio (AFR) that is independent of
the type of fuel being used.
Lambda 1.00
Stoichiometric ratio: no excess fuel and no excess air
Lambda > 1.00 Lean: excess air
Lambda < 1.00 Rich: excess fuel
Stoichiometric Air Fuel Ratio for various fuels
Lambda
Air Fuel Ratio
Petrol
Alcohol
LPG
Diesel
1.0
14.7
6.4
15.5
14.5
Calculations with Lambda
Fuel
Stoichiometric
AFR
Measured
value
Calculated value
Petrol
14.7
AFR = 14
Lambda = 14/14.7 = 0.95
Diesel
14.5
Lambda = 1.1
AFR = 1.1 x 14.5 = 16
See
Appendix F – Lambda to Air Fuel Ratio Table
for a quick reference table.
Engine Tuning with Lambda
When tuning the engine, the target Lambda (or AFR) is dependent on the
tuning objective. The following table can be used as a guideline.
Tuning objective
Lambda
Maximum power
0.84 to 0.90
Economy
1.05
Emissions
1.00
Normally the engine is tuned for maximum power at full load and for emissions
or economy at light loads.
The exact requirements for a specific engine and fuel can only be found by
experimentation. On turbo engines extra fuel may be desirable to reduce
exhaust temperatures and help avoid knock. If the vehicle is fitted with a
catalytic converter, extra fuel may be required to ensure the catalyst does not
overheat when not operating at Lambda 1.00
Summary of Contents for LTC
Page 34: ...34 Appendices Appendix C Dimensions...
Page 35: ...MoTeC Appendices 35...
Page 36: ...36 Appendices...