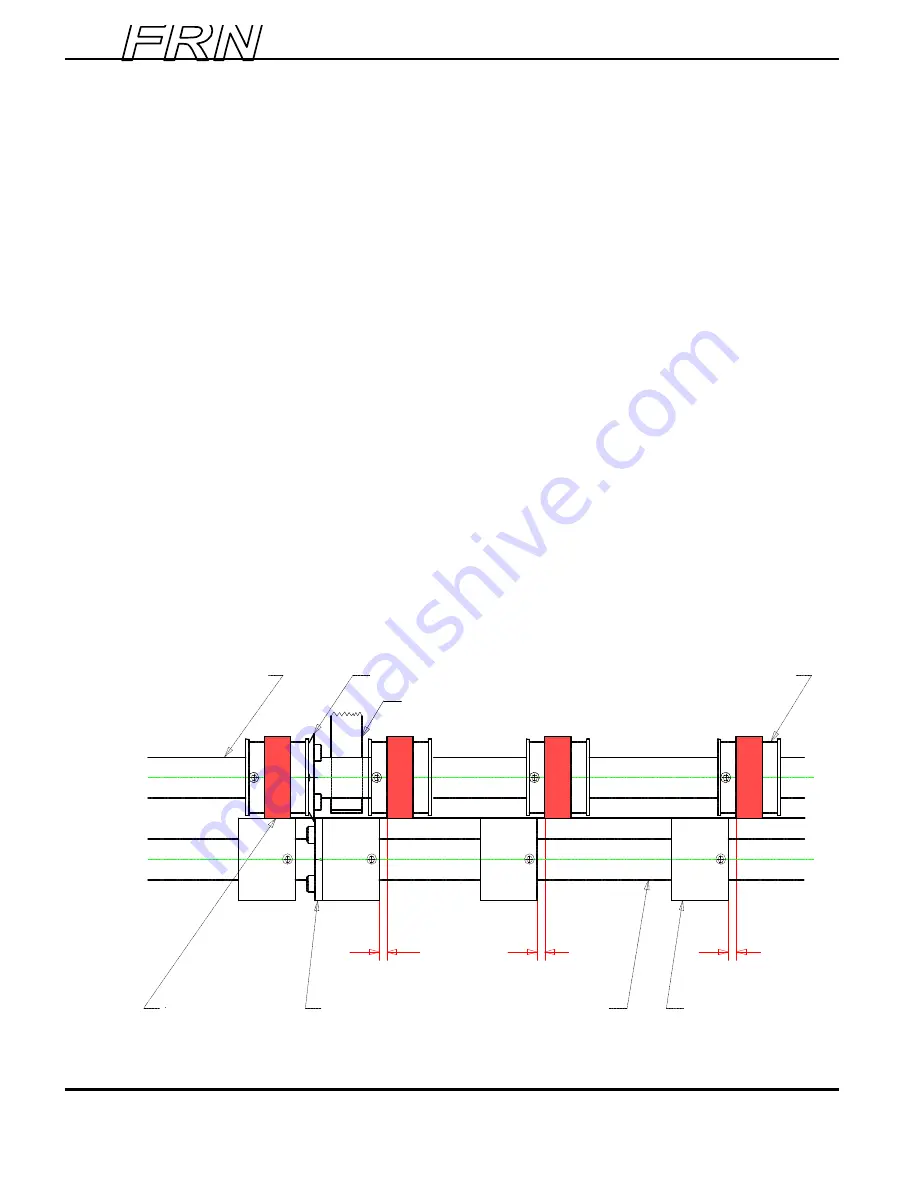
N U M B E R E R
PAGE 25
7.2 .......Setting up
To set a perforator in the required position, follow these steps:-
- Set up the feed bed as described previously in section 3.1.
- Loosen the hub with the perforating blade fitted and all other
hubs on the shaft.
- Wind a sheet through the machine until the sheet is near the
blade.
- Tighten the hub with the blade in the exact position to the job.
- Wind the sheet out of the machine and set the stacker guides and
backstop. ( see section 3.6 on page 13 )
- Set all the other hubs as shown in the drawings,(Figs 7.11 & 7.12)
noting the gaps between upper tyres and lower hubs. THIS
SETTING IS IMPORTANT to ensure perforating accuracy.
- Fit a perforation stripper as close as possible to the perforating
blade (as shown in Figs. 7.11 & 7.12.) This will prevent the sheets
wrapping around the blade.
See section 8.1 (Slitting) for an
important note about setting stacker guides & sheet smoothers.
Section 7
PERFORATING
Perforating - Carbonless Sets ..................................... Fig 7.12
PERFORATION STRIPPER
3,00 mm
( 1/8")
GLUED EDGE OF SET
ANVIL
PERFORATING BLADE
LOWER HUBS (SOLID)
LOWER OUTPUT SHAFT
UPPER OUTPUT SHAFT
UPPER TYRE AND HUB ASSEMBLIES
3,00 mm
( 1/8")
3,00 mm
( 1/8")