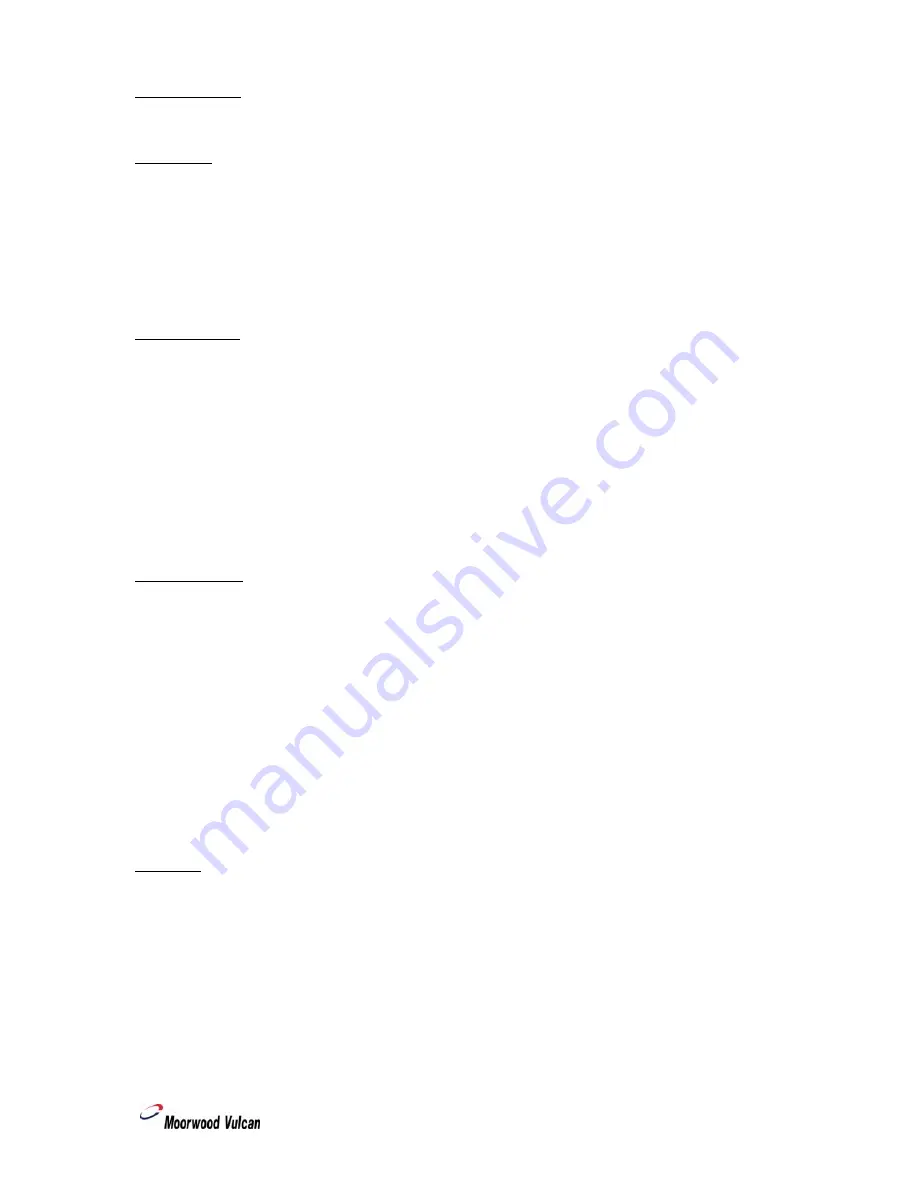
Manual Part No: 930009-01
HD Gas Fryer
- 9 –
Manual Rev No: 1
INSTALLATION (cont.)
Positioning (cont.)
If the fryer is to be positioned in such a way that it is possible to touch the rear of the fryer when
hot, then a Heat Shield (available as an accessory)
MUST
be fitted to the back panel.
Accessory Kit:-
HD30F-HS Heat Shield Kit (300 Fryer)
HD60F-HS
Heat
Shield
Kit
(600
Fryer)
Important Note
The appliance
MUST NOT
be connected
DIRECTLY
to a flue or ventilating system, although the flue
products of two or more appliances may be directed into a common outlet when building a suite of
appliances (see separate instructions for suiting appliances).
Ensure that the appliance is level in two places - front to rear and side to side. To check the level it is
recommended that a spirit level be placed on a shelf in the open oven - NOT on top of the cooker! Level
can be achieved by adjusting any or all of the screw in feet in each corner of the base. Turn anti-
clockwise to lower and clockwise to raise the corner.
Gas Connection
Natural Gas: The size of the supply pipe should be no smaller than ¾” BSP and an easily accessible
stopcock must be fitted in the gas line adjacent to the appliance.
An armoured flexible pipe of a
GAS COUNCIL APPROVED PATTERN
is recommended.
Ensure that all the pipes to the appliance are clean and free from swarf etc,
BEFORE
making the final
connection.
Propane Gas: Follow the same procedure as that for Natural Gas EXCEPT that the Gas Governor
MUST
NOT
be fitted, - the Gas Supply Tank or Cylinders are already fitted with a Gas Regulator.
Leak Test
Clean off any protective film from the stainless steel panels.
AT THIS STAGE, LEAK TEST THE WHOLE SYSTEM. THE GAS SAFETY REGULATIONS
require that
ALL
connections in the gas supply line between the Gas Meter and the appliance is tested for gas leaks.
THIS MUST BE DONE BEFORE COMMENCING TO COMMISSION THE APPLIANCE
.