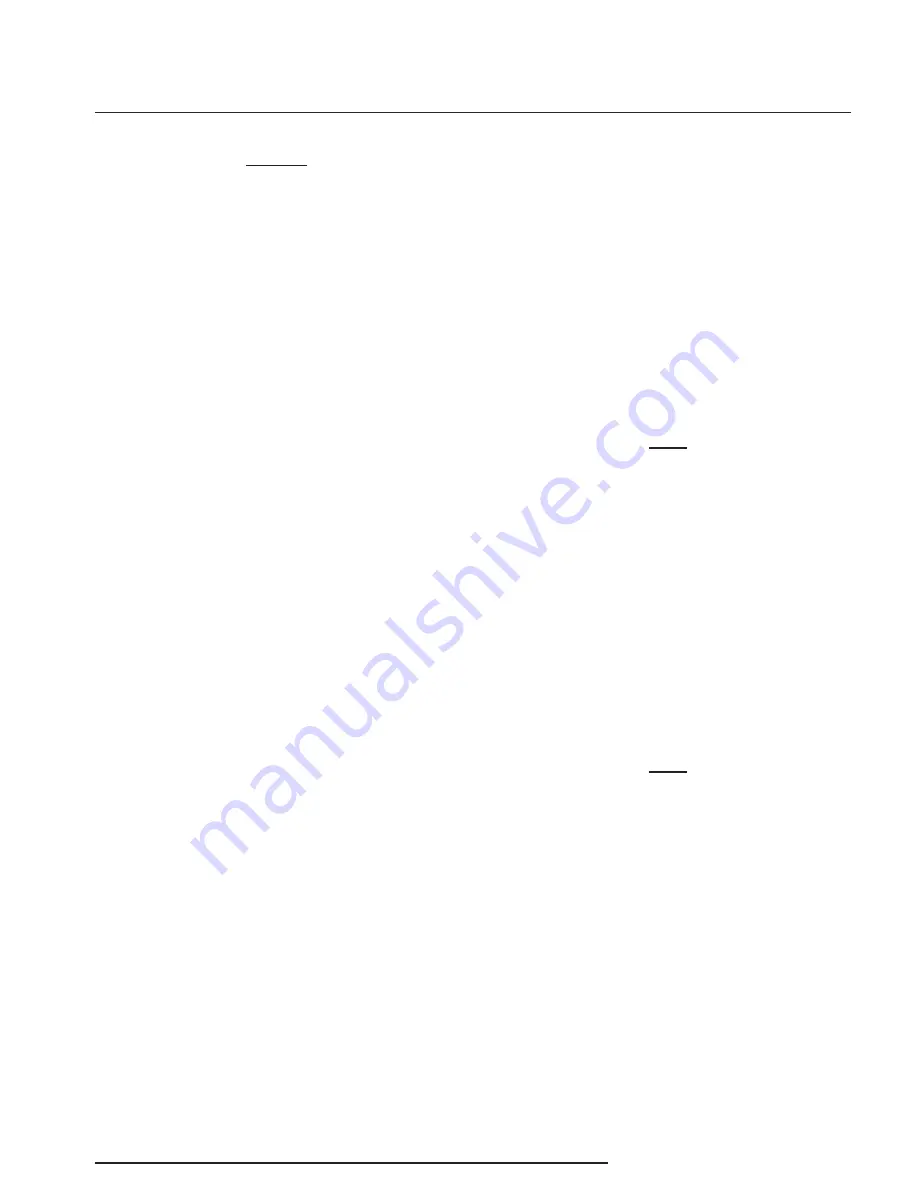
IPT
2
The Interface Solution Experts
9
Installation
Installation of the IPT
2
is divided into three phases:
mounting, electrical connections, and pneumatic con-
nections. In most cases, it is easier to mount the IPT
2
before completing the electrical and pneumatic con-
nections.
Mounting
Individual IPT
2
s consist of two parts: the transmitter
and the mounting block. Units without a mounting
block snap onto a header. IPT
2
s with a mounting block
are rail mounted. Ensure that the unit is mounted in
an area free of dust, moisture, and corrosive elements.
See Figure 4 for mounting dimensions.
Note:
It is recommended that mounting blocks and headers
be purged of any debris prior to mounting the IPT
2
. In-
sert a small diameter, blunt tip probe into the fi tting and
unseat the ball-check valves for a few minutes with the
fi ltered instrument air supply in operation.
Rack- or surface-mounted IPT
2
s should be ordered
with a Moore Industries' rack-mounted header (RIR) or
a surface-mounted header (SIR). This eliminates the
need for an interlocking mounting block and rail. 5, 10
or 15 units can be snapped onto one header, allowing
multiple units to receive supply air from one supply
pipe. To mount an IPT
2
onto a header, push the unit
into place until the retaining lever snaps up fl ush be-
neath the handle. To remove an IPT
2
, press down on
the retaining lever and lift the unit out by the handle.
Note:
Check valves in the headers prevent the loss of
supply or output air during mounting or removal
of IPT
2
s.
Rail-mounted IPT
2
s must use a pneumatic mounting
block. Pneumatic mounting blocks are 1.39 inches
wide. Using a 0.17 inch wide gauge between blocks
provides uniform spacing while occupying minimum
rail length.
Caution:
Coupler must be kept lubricated to prevent
damage to O-rings in test jacks. Te
fl
on
lubricant is recommended. If grease is used,
keep out of air passage.
If the unit is not supplied with the output test jacks, use
an air pressure gauge to measure the output air supply
pressure (e.g., read 3psig for a 3-15psig unit or 15psig
for a 15-3psig unit).
4. Any deviation in the output pressure (e.g., 3 psig
for a 3-15 psig unit or 15 psig for a 15-3 psig unit),
can be corrected by using the Zero potentiomenter
in a range of ±10%.
5. Set the current input signal for 100 percent output
(e.g. 20mA for a 4-20mA input, 3-15psig output;
4mA for a 4-20mA input, 15-3psig reverse output).
6. Any deviation in the output pressure (e.g., 15 psig
for a 3-15 psig unit or 3 psig for a 15-3 psig unit),
can be corrected by the Span potentiometer over
the range of ±10%.
7. Repeat steps 1 through 6 (as applicable) until no
further adjustments are required.