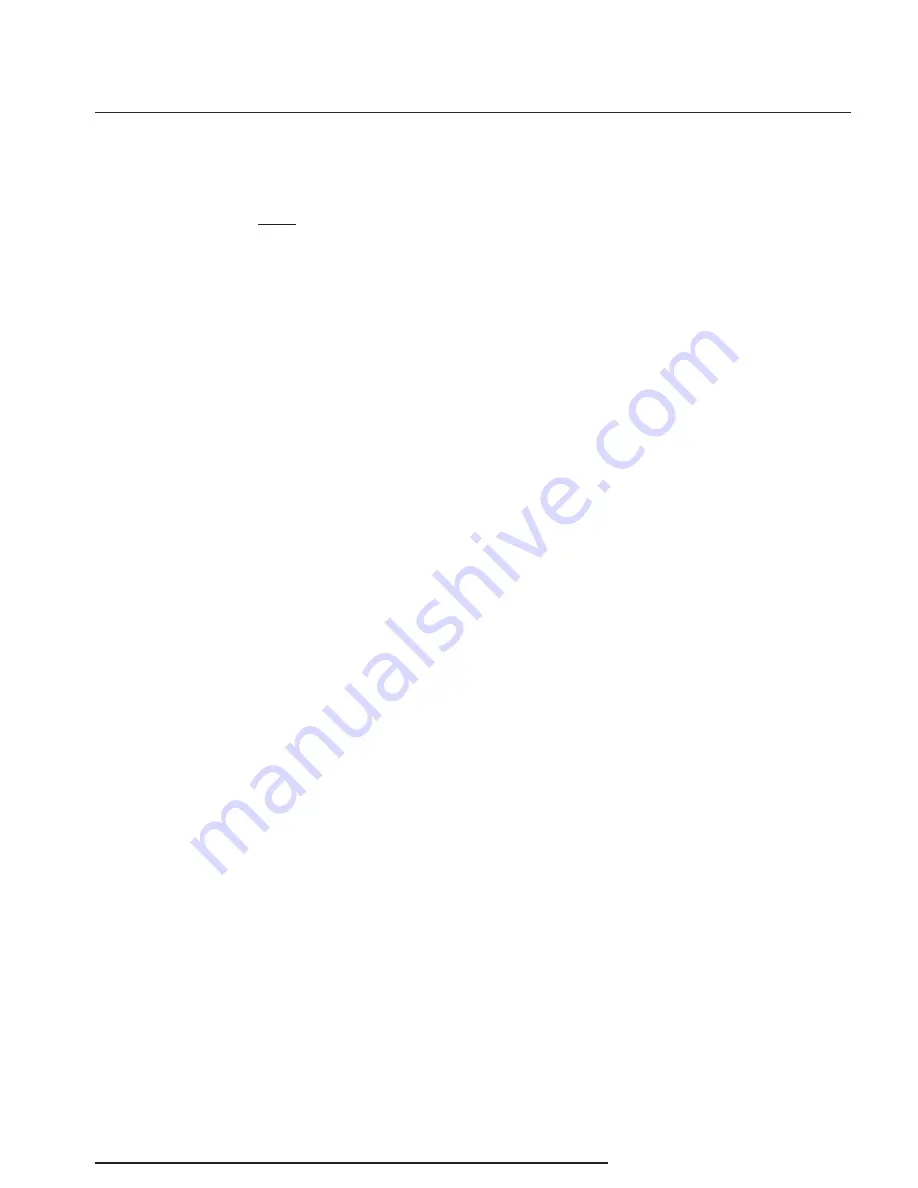
IPT
2
The Interface Solution Experts
5
Instrument Air and
Filtration Information
Note:
For optimum performance, the selection and
use of a good quality air fi ltration system is
essential. Most users fi nd that it is much less
expensive and troublesome to design a system
that includes good air fi ltration than deal with
downtime and repairs later.
A clean, dry air supply is important to assure the
maximum service life of an IPT
2
. Good air quality in-
volves removing solids, oil and water from the air after
compression. The cleaner the air, the longer the time
before servicing is needed.
Oversizing elements avoids performance abberations
and reduces maintenance time. Redundancy should
be used where possible to avoid shutdown during
maintenance.
Solids: Random solid dirt, such as pipe scale and rust,
is rarely a problem in compressed air instrument sys-
tems. A good fi lter removes these solids. However, if
there is a desiccant dryer in the line, a high-effi ciency
sub-micron fi lter is recommended to remove the highly
abrasive sub-micron particles produced by the dryer.
Liquid Oil: Liquid oil is the most common problem in
compressed air instrument systems. A coalescing fi lter
removes sub-micron liquid droplets from the air, and is
usually supplied with an automatic drain.
A coalescing fi lter works by trapping oil and water
droplets in a bed of microfi bers. The droplets run
together at fi ber cross-over points, form large liquid
drops, and are forced by air fl ow to a drain. A fi lter
system consisting of a general purpose fi rst-stage fi lter
(about 5 micron) and a high-effi ciency coalescing fi nal
fi lter is recommended to obtain contaminant-free air.
The exact location of the fi rst-stage fi lter is not im-
portant; it can be located just ahead of each fi nal
fi lter, or a single fi rst-stage fi lter can be located on a
main line to protect a number of fi nal fi lters on branch
lines. Each fi nal fi lter (coalescing) should be located
just ahead of each pressure regulator. In a new plant
installation, an oilless compressor may be used to
eliminate this problem.
Water: The amount of water in an air system
depends on temperature, pressure and the relative
humidity of the air.
Suffi cient water must be removed to lower the dew
point of the air to a temperature below ambient. The
dew point (at line pressure) is expressed as the tem-
perature at which any moisture in the system begins to
condense.
Water may be removed using a number of techniques,
including coalescing fi lters, refrigeration dryers and
desiccant dryers. In addition, a variety of combina-
tions and modular systems may be used for special
circumstances.
Care must be taken in the selection and location of
the fi lter, because cooling downstream of the fi lter can
cause more condensation of water. A coalescing fi lter
should be installed immediately upstream of the pres-
sure regulator. This type of fi lter removes most of the
water before the air enters the regulator.
For systems subjected to freezing temperatures, the
portion of the system that runs outdoors should have a
dryer installed. The dryer reduces the dew point below
the lowest expected outdoor temperature. A desic-
cant dryer is used with a coalescing fi lter upstream to
keep the desiccant dryer from being damaged by oil or
overloaded with excessive condensed water. Another
high-effi ciency coalescing fi lter is recommended down-
stream of the dryer, to remove the desiccant particles.
ISA Specifi cations: The Instrument Society of America
standard ISA-S73, 1975 (ANSI MC11.1-1975) covers
the air quality requirements for instrument grade air for
use in pneumatic installations.
The dew point in outdoor installations must be at least
7.8°C (18°F) below the minimum local ambient tem-
perature. For indoor installations, the dew point must
be at least 7.8°C (18°F) below the minimum interior
temperature or 2°C (35°F), whichever is greater.
Although the ISA standard calls for a 35°F dew point,
this is often unnecessary indoors, and may be unsatis-
factory outdoors under freezing conditions.
Filters that exceed the ISA specifi cation provide very
inexpensive protection. Although the ISA specifi cation
calls for particle size not to exceed 3 microns and oil
content not to exceed 1ppm, most fi lter manufacturers
supply a line of coalescing fi lters that remove particles
down to sub-micron sizes (often 0.01 micron) while
also removing oil to below ISA 1ppm specifi cation
(often to 0.01ppm).