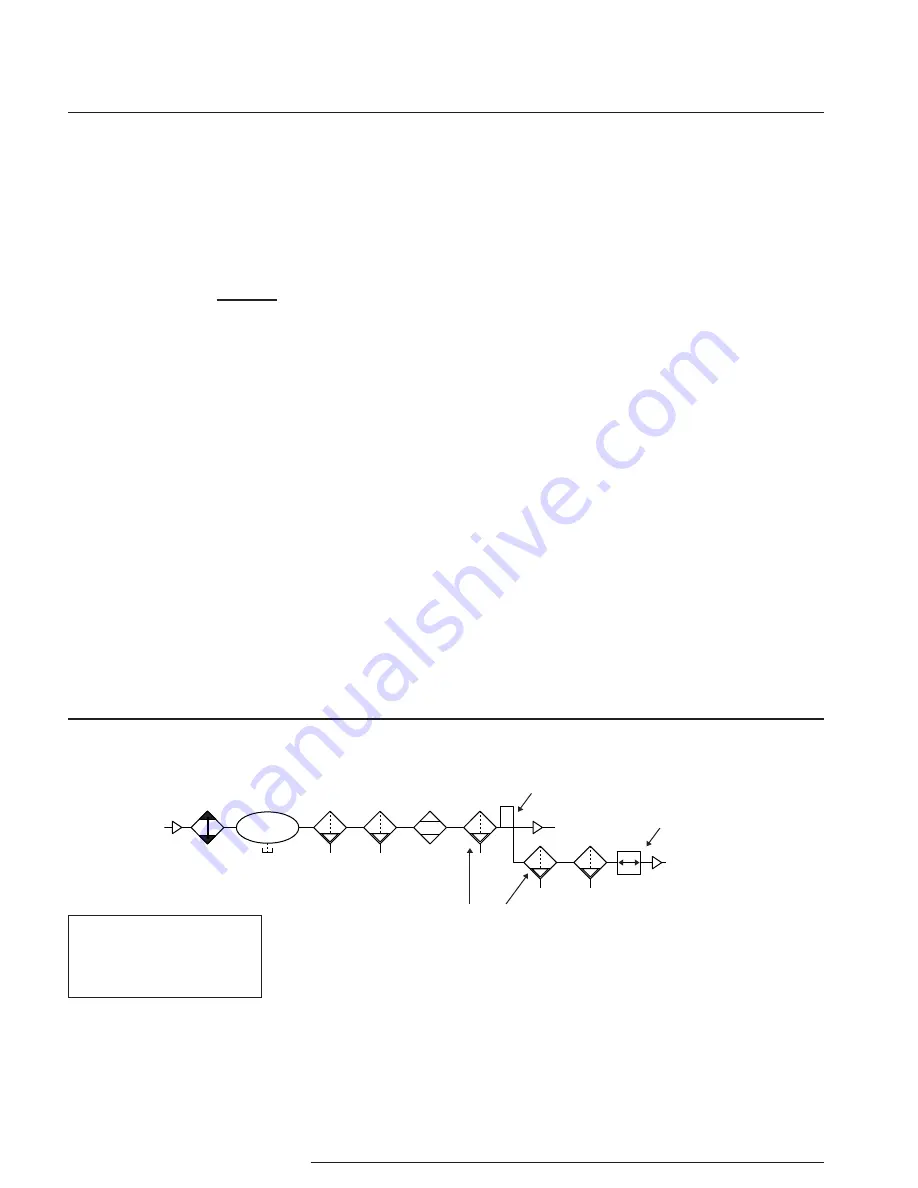
IPT
2
6
The Interface Solution Experts
Cooler
Receiver
5-Micron General
Purpose Filter
High-Efficiency
Coalescing
Filter
5-Micron General
Purpose Filter(s),
One Main or Multiple
on Branch Lines
Dessicant
Dryer
Extend Branch Line(s) Above Main
Line to Avoid Passing Liquids
0.01-Micron
High Efficiency
Coalescing
Filter(s)
{
Purified Air
For IPT
2
's
Main Line to
Other Branches
Keep Short
Pressure
Regulator
D
The use of coalescing fi lters with retention of 0.01
micron particles and droplets is recommended;
they remove all undesirable traces of oil and water
droplets. Proper placement with respect to the
regulator may eliminate the need for dryers, except
when coalescing fi lters are exposed to freezing
temperature (keeping in mind that the dew point of the
purifi ed air must be kept below worst case ambient).
Figures 1 and 2 illustrate typical non-redundant
systems with multiple branch lines. They both work
in any environment above freezing and diff er only
in the placement of the general purpose fi rst-stage
fi lter. Gauges, valves, and diff erential pressure
indicators (for fi lter service monitoring) are not shown.
It is recommended that fi lters with integral service
life indicators or diff erential pressure indicators be
used to help ensure proper servicing, as well as
redundancy to avoid shutdown during servicing.
Figures 1 and 2 diff er in the method used to
remove water. The use of a desiccant type dryer
(Figure 2) requires upstream fi ltration to prevent
oil contamination of the desiccant, as well as
downstream fi ltration, to prevent desiccant fi nes from
introducing new contamination.
The service life of an IPT
2
is directly proportional to
the cleanliness and dryness of its air supply. The
small cost of providing high-quality air ensures a
longer, more trouble-free service life for the unit.
Application Information
Any approach to providing good instrument air
quality should evaluate the worst case air fl ow and
ambient temperature of the location. This is required
to determine sizing of the air system elements. A
knowledge of yearly humidity cycles is also important
for this evaluation.
Caution:
Before placing IPT
2
s in service, all pneumatic lines
and mounting blocks or headers (SIRs or RIRs)
should be "blown down" to purge contamination and
condensation deposited during piping and installation.
Also blow down lines to loads, since all output air
vents back through the IPT
2
, and there are never
fi lters installed to trap these contaminants (normally
only present at start-up). It is recommend this be
done for at least an hour, longer if there is evidence of
water or oil coming through.
The IPT
2
requires periodic maintenance. Service in
the fi eld is limited to visual inspection and cleaning of
the input nozzle fi lter screen on the IPT
2
and servicing
of the compressed instrument air fi ltration system.
The unit may be returned to the factory for complete
disassembly, cleaning, and servicing on a periodic
basis.
Figure 1. Non-Redundant System with Desiccant Dryer
Note: All fi lters should have
automatic drains and service
life indicators to show when
elements need changing.