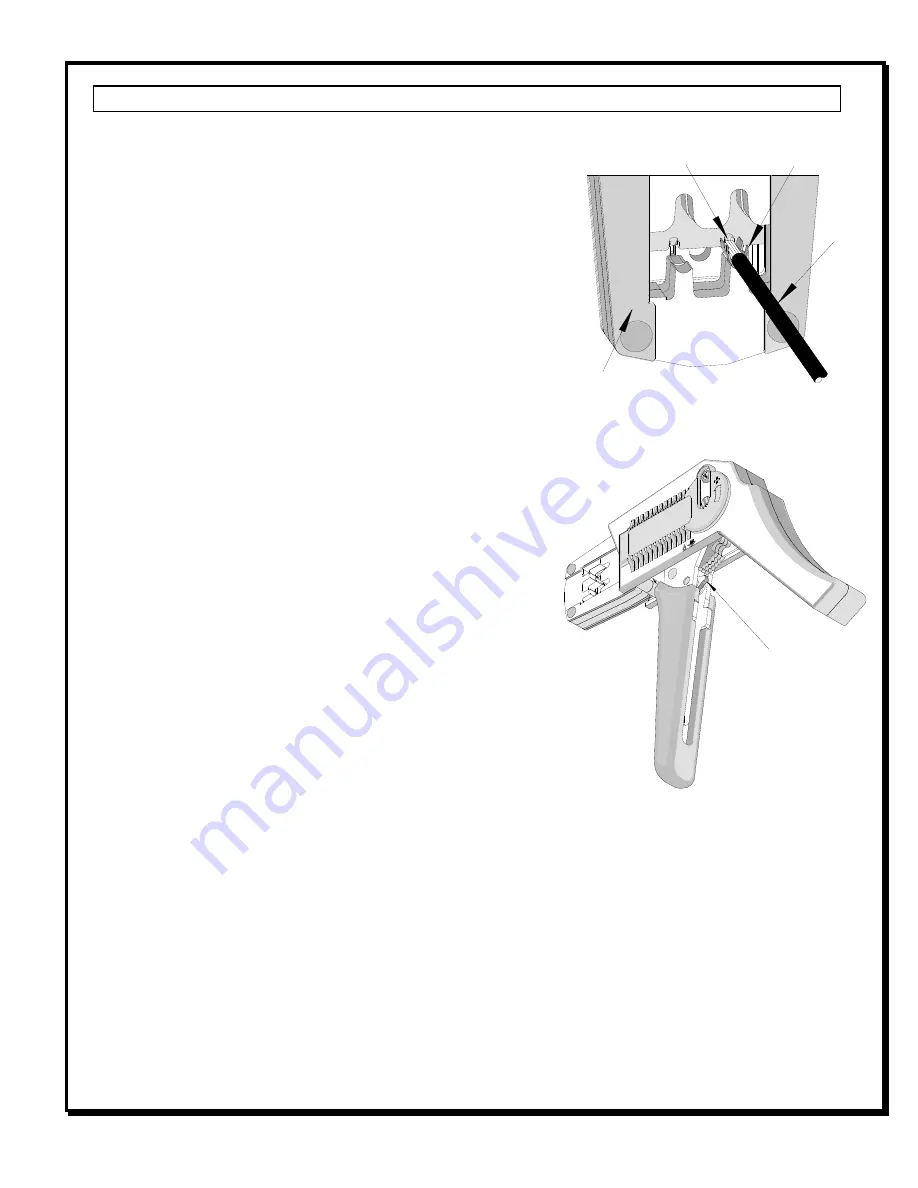
Hand Crimp Tool for CP 1.5 Series Crimp Terminals
Doc No: ATS-638118900
Release Date: 02-12-07
UNCONTROLLED COPY
Page 3 of 6
Revision: D
Revision Date: 11-22-10
Note: The tamper proof ratchet action will not release the tool until it has been fully closed.
6.
Remove the crimped terminal from the terminal locator.
7.
Visually inspect the crimped terminal for proper crimp location.
Maintenance
It is recommended that each operator of the tool be made aware
of, and responsible for, the following maintenance steps:
1.
Remove the plastic handles from the metal tool frame by
removing the screws and remove dust, moisture, and other
contaminants with a clean brush, or soft, lint free cloth.
2.
Do not use any abrasive materials that could damage the tool.
3.
Make certain all pins; pivot points and bearing surfaces are
protected with a thin coat of high quality machine oil. Do not
oil excessively. The tool was engineered for durability but like any fine piece of equipment it needs cleaning
and lubrication for a maximum service life of trouble free
crimping. Light oil used at the pivot points every 5,000 crimps
or 3 months, will significantly enhance the tool life.
4.
Wipe excess oil from hand tool, particularly from crimping area.
5.
When tool is not in use, keep the handles closed to prevent
objects from becoming lodged in the crimping dies, and store
the tool in a clean, dry area.
Miscrimps or Jams
Should this tool ever become stuck or jammed in a partially closed
position,
Do Not
force the handles open or closed.
The tool will
open easily by pressing the ratchet release lever up. See Figure 3.
How to Adjust Tool Preload
It may be necessary over the life of the tool to adjust tool handle
preload force. Listed below are the steps required to adjust the crimping force of the hand tool to obtain proper
crimp conditions:
1.
Remove the 2mm locking screw from the numbered adjusting wheel using a screw driver. See Figure 4.
2.
Using the same screw driver turn the adjustment wheel to the next highest number.
Note: The uneven numbers are in clockwise (CW) direction and the even numbers are counter clockwise
(CCW).
3.
Example: If the preload is set at number 5, then to increase the preload, turn the adjustment wheel until the 6
th
position is located over the 2mm locking screw tapped hole. If it is necessary to move to the 7
th
position, then
the adjustment wheel should be turned counter clockwise (CCW) until the 7
th
position is over the 2mm locking
screw tapped hole.
RATCHET
RELEASE LEVER
Figure 3
WIRE
Figure 2
WIRE IS UP AGAINST
THE WIRE STOP
FRONT OF THE
HAND TOOL
TERMINAL