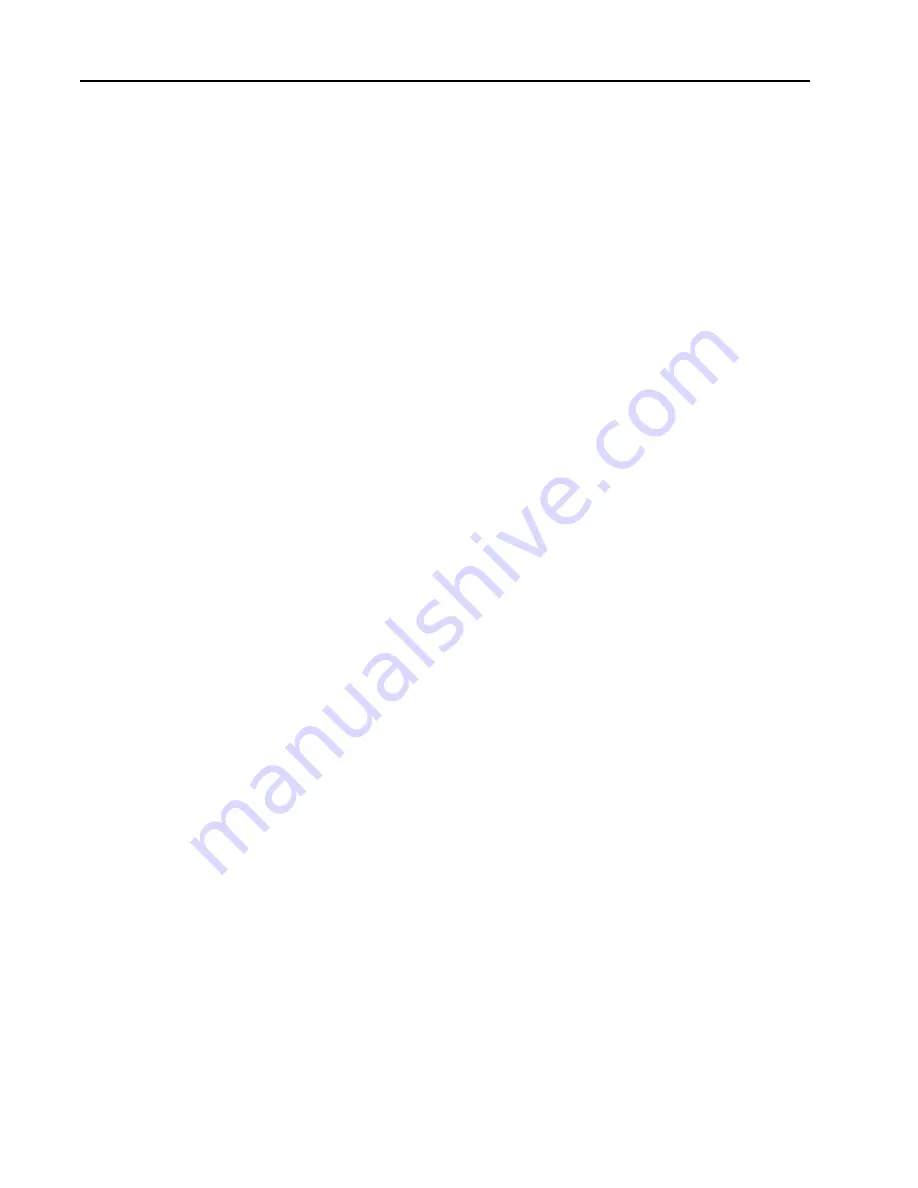
Performing MFC Installation
Chapter Two: Installation
24
4)
Flow clean, dry purge gas across the fittings to minimize particle contamination prior to and during
installation. Use only purge gases that are approved for your process.
5)
Connect the process gas supply remembering to tighten the seal gaskets according to the fitting
manufacturer’s or seal gasket manufacturer’s recommendation. Use appropriate gasket material for the
application. Seal gaskets are not included with the MFC.
DO NOT over-tighten connections.
The process fittings in the IE500A / IE1000A High Flow Rate Mass Flow Controller are screwed into the
main flow path mechanical parts and sealed with the appropriate o-ring (consistent with the material
ordering code). Use a backing wrench when tightening the process fitting to the MFC to prevent
loosening of the factory installed fittings on the MFC.
6)
Perform appropriate leak checking of your gas lines and MFC connections to verify the integrity of the
gas seals prior to supplying power to the MFC. Verify the leak integrity of both the process fitting
connection and the fitting-to-main flow path connection prior to running process gas.
7)
Before connecting the cable leading to the MFC, verify that all pins for power and signal match those for
the interface I/O type being used. Information on each I/O type’s pinouts are found in the following
chapter.
8)
Connect cable and power up the MFC.
9)
Allow minimum one (1) hour warm-up prior to performing a flow zero operation.
10)
Apply gas slowly to the MFC by turning on the regulator. Some leak by the main flow valve may
occur while inlet line pressure equalizes across the diaphragm to provide the needed pressure to
achieve full closure.
11)
When purging the line, provide a valve open signal to the MFC. Allow a long pump down time
so that the pressure upstream of the MFC can drain to the appropriate low level. Gas will need to
drain through the much smaller pilot valve orifice once the MFC inlet pressure drops below that
needed to overcome the mechanical closing force of the main flow valve.
For other hazardous gases, consider pumpng the process line from both the inlet and outlet side
of the MFC. Cycle purge the system and backfill with an inert gas for optimum safety.
Summary of Contents for MKSINST IE1000A
Page 18: ...10 MKS Instruments Inc MKS Calibration and Service Center...
Page 20: ...12 MKS MKS Calibration and Service Center...
Page 22: ...14 This page intentionally left blank...
Page 26: ...18 This page intentionally left blank...
Page 48: ...40 This page intentionally left blank...
Page 74: ...66 This page intentionally left blank...
Page 75: ...Appendix C Health and Safety Form Model Code Description 67 Appendix C Health and Safety Form...