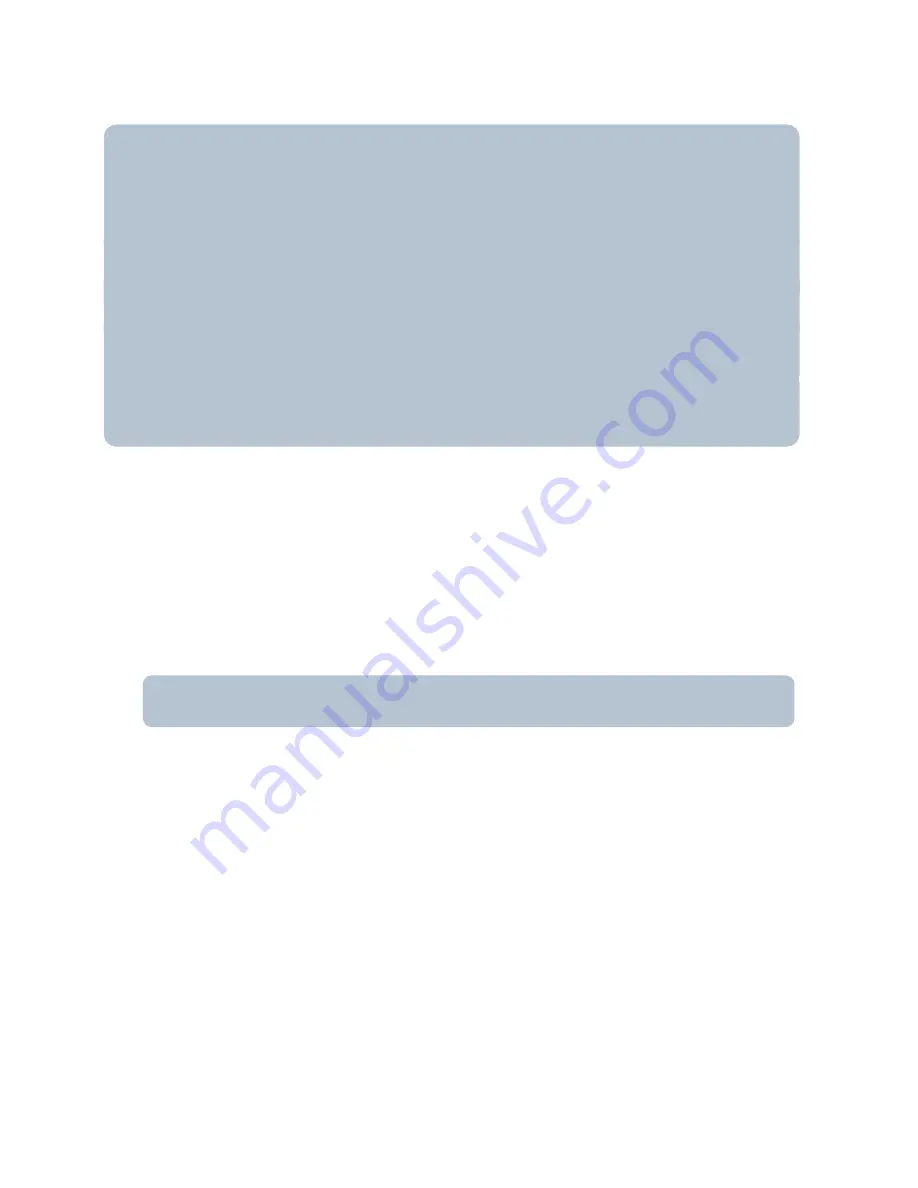
MKS Instruments UK Ltd
Microvision2 Hardware Manual – SP101015.102 August 2010
16
Interfacing Notes
The 120mA maximum load for the power supply outputs is shared between the Digital and Analogue
connectors.
When interfacing digital signals between units the preferred method is to:-
a)
Have a pull-up resistor/current source on all inputs to the local power supply rail. Often this feature
is provided by the digital input chip itself.
b)
Use an open collector/drain/contact closure to ground as the output drive signal.
c)
Where appropriate, arrange the hardware/software configuration so that an input Hi state is a safe
condition. This ensures that if a connection should be unplugged the system will go into a fail-safe
state.
d)
In cases where the external equipment is some distance away and/or is likely to have a different
ground potential the fitting of opto-couplers on the interfacing should be implemented.
Using this approach allows for easily interfacing between different voltage levels and logic families.
4.10 Ethernet
A standard RJ45 type 10/100 Base-T Ethernet connector used to connect the
Microvision2 to a host PC,
hub, switch or network.
Ensure you read through the network scenarios starting on Page 21 before connecting the unit to
your network
4.11 External Multiplier Protection
The multiplier (if fitted) can be externally protected against damage from high temperatures or pressures if
required. Pin1 of the Digital IO connection is dedicated to this purpose.
Pin1
LOW (0V)
Multiplier Enable
Pin2
HIGH (3.3v)
Multiplier Inhibit
If the Microvision2 forms part of an integrated system, this function may already be in use.