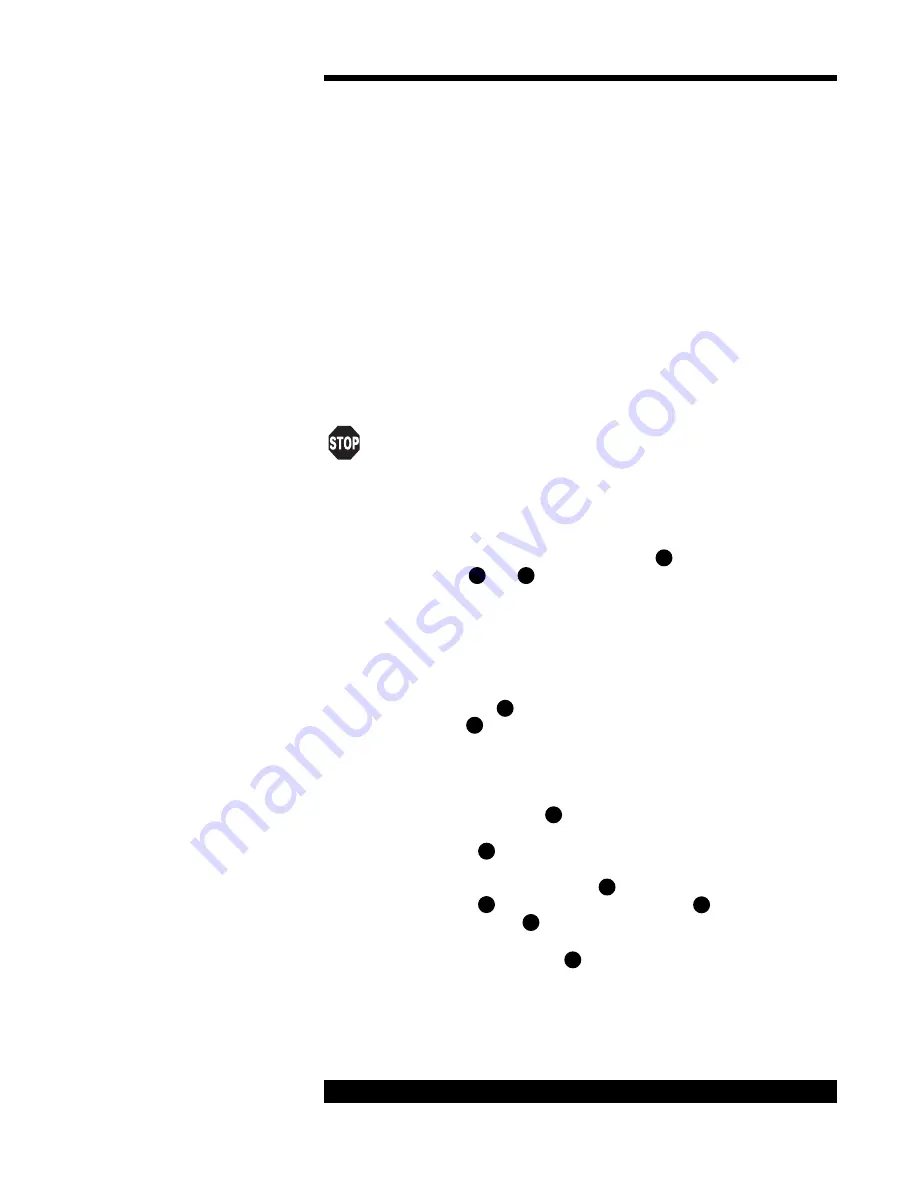
13
Cold Cathode Ionization Vacuum Sensor
Cleaning
If ultrasonic cleaning, use high quality detergents compatible with
aluminum, such as ALCONOX
®
.
Scrubbing with mild abrasives can remove most contamination.
Scotch-Brite™ or a fine emery cloth may be effective. Rinse with alcohol.
Clean aluminum and ceramic parts chemically in a wash, such as a 5 to
20% sodium hydroxide solution (not for semiconductor processing), at room
temperature (20°C) for one minute. Follow with a preliminary rinse of
deionized water. Remove smut (the black residue left on aluminum parts
due to this process) in a 50 to 70% nitric acid dip for about 5 minutes.
Chemical cleaning should not be used to clean the anode; mild
abrasives or ultrasonic cleaning are acceptable.
Do not damage the leaf spring while cleaning the Sensor.
Each of the above cleaning methods should be followed with multiple rinses
of deionized water.
Dry all internal components and the
sensor body in a clean oven. The
two
ceramic spacers, and , are slightly porous and will require longer
drying time in the oven to drive off the absorbed water.
Assembly
Wear gloves and assemble with clean tools.
1
Check the
anode . It should be straight and centered with the
sensor body for proper operation.
2
Roll the
sensor body on a flat surface and look for any radial
run out motion.
3
Install the
ground shield using tweezers. Make sure that at the
groove of its larger diameter, the
ground shield interlocks with the
locating collar .
4
Slide the
small ceramic spacer over the small end of the
ground shield . Check that the leaf spring will contact the
base of the
cathode as shown to the right. If not, remove the
small ceramic spacer and the ground shield. Gently bend the leaf
spring towards the anode , and then replace the ground shield
and
ceramic spacer.
F
F
F
F
F
F
F
F
F
F
2
5
6
11
4
7
8
7
5
6
9
8
Summary of Contents for HPS I-MAG 423 Series
Page 6: ...Cold Cathode Ionization Vacuum Sensor...
Page 21: ...15 Cold Cathode Ionization Vacuum Sensor 2 1 3 5 6 7 8 9 10 11 12 13 14 15 4...
Page 24: ...18 18 Cold Cathode Ionization Vacuum Sensor NOTES...
Page 25: ......
Page 26: ......