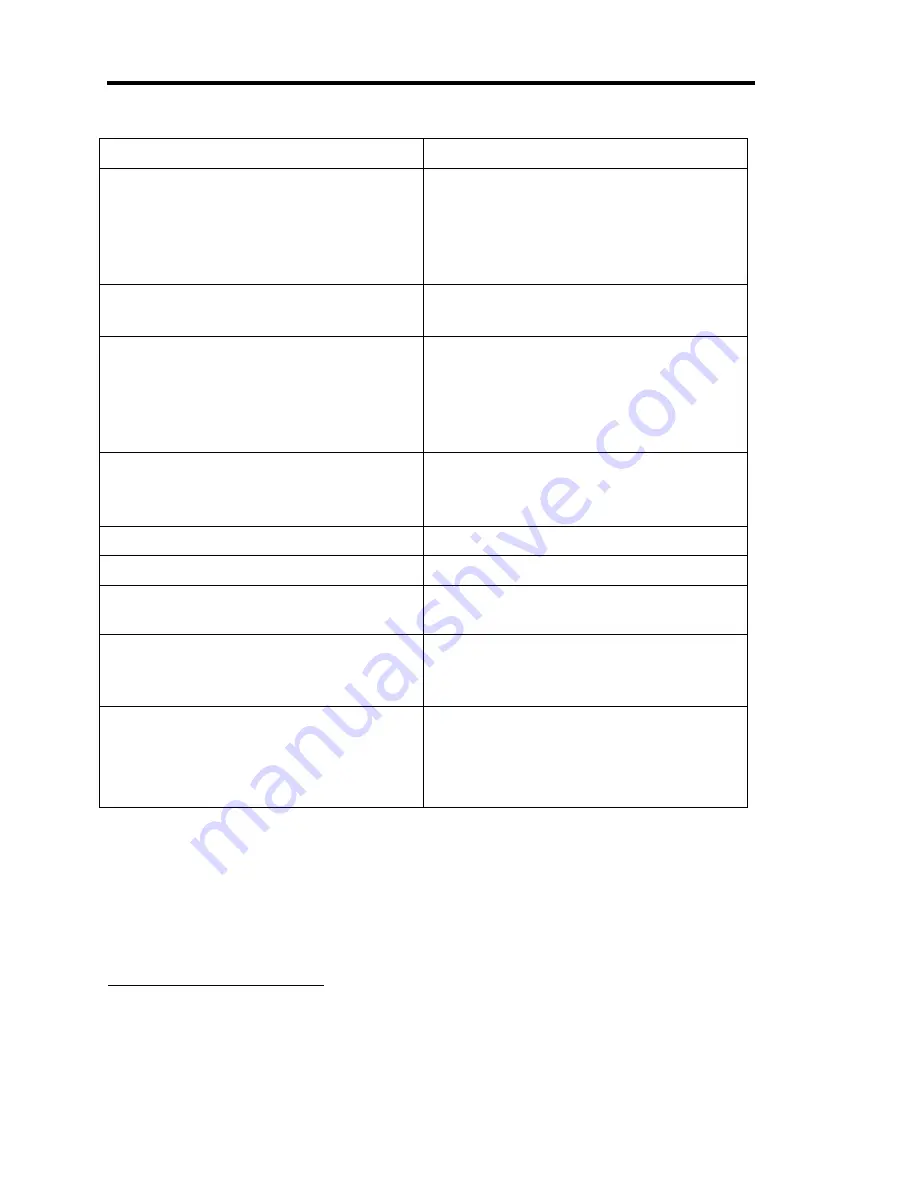
Appendix A: Product Specifications
132
External Set Point Signal
5 Volts or 10 Volts
*
, selectable
Fuses
Low power unit: 90 to 132 VAC
180 to 264 VAC
High power unit: 90 to 132 VAC
180 to 264 VAC
0.63A (T), 250V, 5 x 20 mm
0.315A (T), 250V, 5 x 20 mm
1.25A (T), 250V, 5 x 20 mm
0.63A (T), 250V, 5 x 20 mm
Maximum relative humidity
80% for temperatures up to 31
°
C,
decreasing linearly to 50% at 40
°
C
Input Power
Low power unit
High power unit
90 to 132 or 180 to 264 VAC @50/60 Hz
75 VA (max)
90 to 132 or 180 to 264 VAC @48/62 Hz
150 VA (max)
Output Power
Low power unit
High power unit
±15 VDC @ 0.5 Amps (max)
4
±15 VDC @ 1.5 Amps (max)
Overrange Pressure
±10.5 Volts
Pressure Input Signal
0 to +10 Volts DC
Pressure Units
Torr, mTorr, mBar, µBar, Pascal, kPa,
cmH
2
0, inH
2
0
Set Points
Internal
External
5, each one pressure or position selectable
1, pressure or position selectable
Weight
Low power unit
High power unit
Optional valve failsafe battery backup
7 lbs. 3 oz. (3.26 kg)
6 lbs. (2.04 kg)
3 lbs. 8 oz. (1.25 kg)
Due to continuing research and development activities, these product specifications are subject to change without notice.
4
Derated to 0.4 Amps with 90 to 99 or 180 to 198 VAC input.
Summary of Contents for 651D Series
Page 1: ...118965 P1 Preliminary 5 02 MKS Type 651D Pressure Controller...
Page 8: ......
Page 10: ......
Page 12: ......
Page 20: ...Customer Support Chapter One General Information 8 This page intentionally left blank...
Page 50: ...Labels Chapter Three Overview 38 This page intentionally left blank...
Page 78: ......
Page 149: ...Appendix C Initial Settings 137 This page intentionally left blank...
Page 150: ......
Page 158: ...Appendix E RS 232 Message Summary 146 This page intentionally left blank...